Selecting the optimal pump for slurry applications is crucial for industries that rely on transporting mixtures of solid and liquid materials. Slurry pumps are specialized and robust devices designed to handle the abrasive nature of slurry, reducing downtime and enhancing operational efficiency. This article delves into the essential factors to consider when choosing a slurry pump, while also highlighting the importance of expertise, experience, authoritativeness, and trustworthiness in making informed decisions.
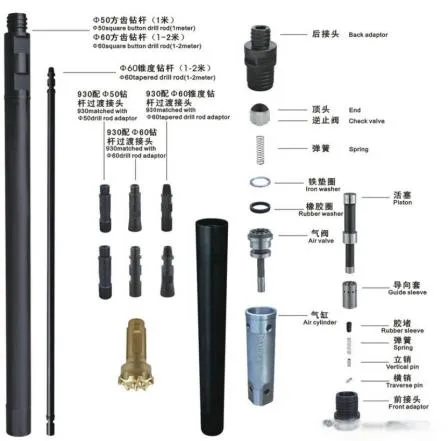
In any industry dealing with mineral processing, manufacturing, or wastewater treatment, understanding the composition of the slurry is the first step in selecting the right pump. Slurries can be broadly classified into two types settling and non-settling. Settling slurries contain coarse particles and are more abrasive, whereas non-settling slurries have fine particles that carry a different set of challenges. An in-depth analysis of the slurry's characteristics, including particle size, concentration, and corrosivity, guides the decision-making process in pump selection.
The experience gleaned from field operations highlights that mechanical seals, impeller type, and pump material significantly affect a slurry pump's performance. Mechanical seals need to withstand the rigors of abrasive materials while maintaining an adequate seal to prevent leakage. From the expertise of seasoned engineers, it's understood that impeller design—such as the choice between closed, semi-open, and open configurations—impacts efficiency and wear, ultimately influencing total cost of ownership.
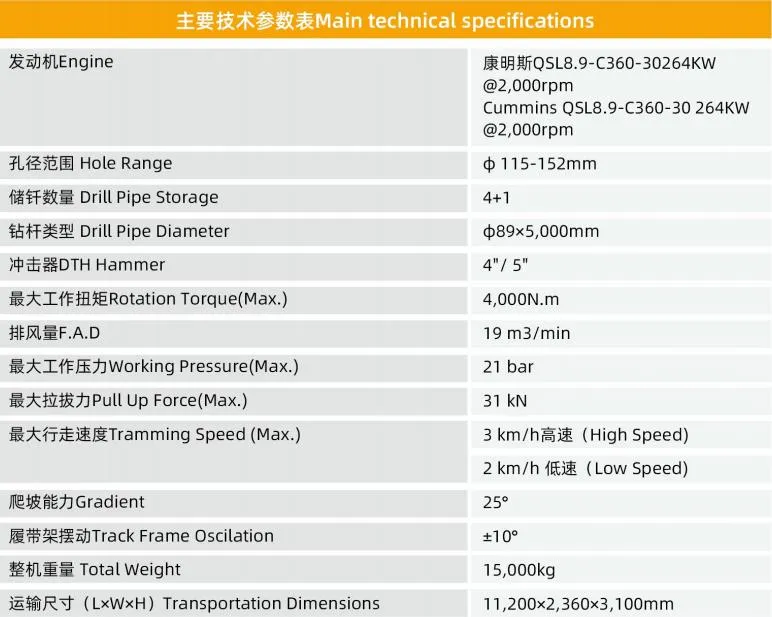
Material selection is another critical aspect underlining the authoritativeness of pump manufacturers.
High-chrome alloys and polymers are commonly used in constructing slurry pumps due to their excellent resistance to abrasion and corrosion. Research and development efforts in material science have led to innovations like the introduction of wear-resistant coatings, which significantly prolong the service life of pump components. Trustworthy manufacturers often provide compatibility charts and detailed guidelines, demonstrating their commitment to transparency and customer success.
pump used for slurry
A vital factor contributing to the trustworthiness of a pump selection is the expertise behind the design and customization of pumps to meet specific industry requirements. Consulting with experts who possess extensive knowledge in hydraulic modeling and system analysis ensures that pumps are not just theoretically suitable but also proven in real-world applications. These practitioners employ advanced computational fluid dynamics (CFD) tools to anticipate pump behavior under different operating conditions.
In recent technological advancements, the integration of smart sensors and condition monitoring systems in slurry pumps has revolutionized preventive maintenance strategies. By providing real-time data on vibration, pressure, and temperature, operators can preemptively address issues, maximizing uptime and reducing repair costs. Investing in such intelligent systems underscores a company's dedication to leveraging state-of-the-art technology to improve reliability and performance.
The selection of slurry pumps extends beyond mere technical specifications; it encompasses an intricate balance between product features, practical field data, and authoritative insights. For industries where downtime means significant losses, choosing the right pump is a pivotal decision that directly influences productivity and profitability. By relying on seasoned experience, specialized expertise, credible sources, and reliable partnerships with manufacturers, industries can ensure the longevity and efficiency of their slurry handling systems.