Navigating the complex landscape of slurry pumping systems requires a deep understanding of both the operational environment and the technology involved. These systems are crucial in industries such as mining, dredging, and wastewater management, where the movement of viscous or abrasive fluids is essential. The following article explores the intricacies of slurry pumping systems, providing insights based on industry expertise and real-world experience.
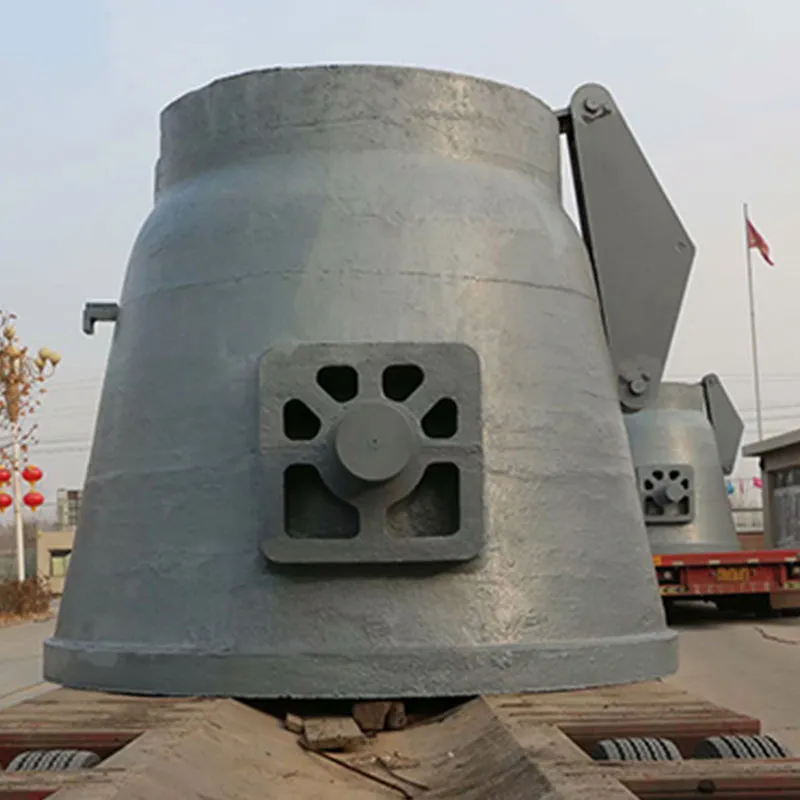
Slurry pumping systems are designed to handle fluid mixtures that contain solid particles, often resulting in significant wear and tear on the pumping equipment. The design of these pumps must account for factors such as particle size, density, and the corrosive nature of the slurry. For example, in mining operations, slurry pumps must efficiently transport mineral-rich slurry across substantial distances, requiring robust construction to withstand abrasive wear.
The key to optimizing slurry pumping systems lies in selecting the right pump and ancillary equipment. Centrifugal slurry pumps are commonly used due to their ability to handle high volumes and variable particle sizes. However, other types of pumps, such as positive displacement pumps, may be more suitable for highly viscous slurries or when precise control of flow rate is required.
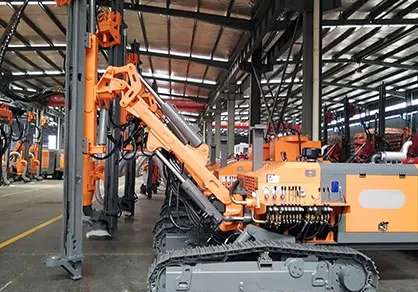
Expertise in the field reveals that regular maintenance is vital to prolonging the lifespan of slurry pumps.
Abrasive slurries can quickly degrade pump components, leading to frequent failures and costly downtime. Implementing a proactive maintenance schedule that includes regular inspections, component replacements, and condition monitoring can significantly enhance system reliability and performance.
slurry pumping systems
In terms of authoritativeness, renowned industry standards such as those set by the Hydraulic Institute and ISO provide valuable guidelines for slurry pump design and operation. Adhering to these standards ensures that systems meet safety and efficiency benchmarks, thereby establishing trust with stakeholders. Manufacturers often leverage these standards to innovate and refine their product offerings, ensuring they meet the evolving needs of industrial operations.
Trustworthiness in slurry pumping systems is also closely linked to the materials used in pump construction. High-chrome alloys, rubber linings, and advanced ceramics are commonly employed to resist abrasive and corrosive wear. By choosing pumps constructed from materials suited to the specific slurry characteristics, operators can minimize the risk of premature failures and ensure consistent performance.
Real-world experience highlights the importance of considering the entire slurry pump system, including ancillary components such as pipes, valves, and fittings. Hydraulic calculations are essential to ensure the compatibility of all system components, preventing bottlenecks or undue pressure loss. Collaboration with experienced engineers during the design phase can lead to a more cohesive and efficient system, further underscoring the importance of expertise in achieving superior outcomes.
Ultimately, slurry pumping systems are a testament to the intricate blend of engineering precision and material science. With evolving technologies and a commitment to adhering to industry standards, the future of slurry pumping systems holds significant potential for innovation. By leveraging collective experience and expertise, companies can achieve sustainable and cost-effective solutions, reinforcing their position as industry leaders.