Navigating the intricate landscape of drill rod thread types is crucial for anyone involved in drilling operations. The diverse range of thread types can significantly affect the performance, efficiency, and durability of drilling equipment. Whether you are a seasoned driller or a procurement specialist, understanding the nuances of drill rod threads can enhance operational success and ensure alignment with industry standards.
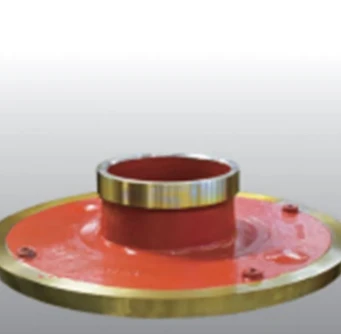
Drill rod thread types are an integral part of the drilling apparatus, serving as the connective mechanism that joins various drilling components. These threads must ensure seamless tool joints, and maintain the structural integrity under high-pressure conditions. Recognizing the right thread type not only prevents mechanical failures but also optimizes the economic aspects of any drilling operation.
The most commonly used drill rod thread types are the API (American Petroleum Institute) standard threads, which include threads like API IF (Internal Flush), API NC (Numbered Connection), and API REG (Regular Connection). These threads are renowned for their reliability and widespread acceptance in the oil and gas industry. Their standardized dimensions and compatibility with a wide range of equipment make them a go-to choice for many professionals.
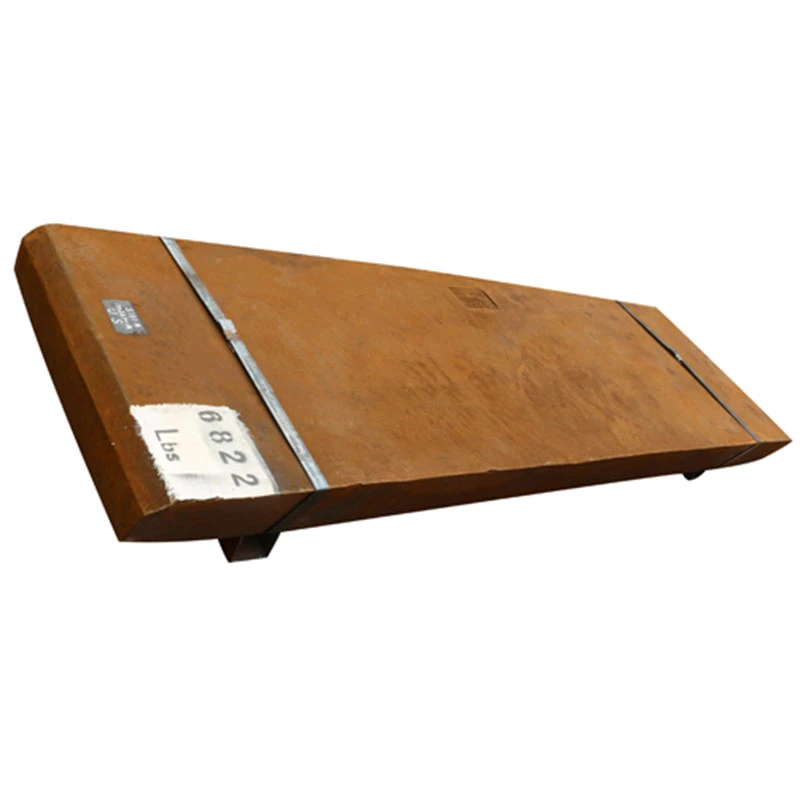
However, in specialized applications such as mineral exploration or geothermal drilling, proprietary thread types often come into play. Examples include Atlas Copco's T-thread series or Boart Longyear's Q-series. These threads are designed to meet specific environmental challenges and operational demands. The engineering behind proprietary threads often focuses on enhanced durability, smoother connections, and optimized torque distribution, which collectively reduce the risk of rod failure and operational downtime.
Choosing the correct thread type requires an analysis of the drilling environment. Environmental conditions such as temperature, pressure, geological formations, and the presence of corrosive elements can all influence thread selection. In harsh environments, selecting a thread type with added corrosion resistance or a special locking mechanism can significantly extend the life of the drill string.
drill rod thread types
Operational parameters also play an essential role in thread selection. The depth of drilling, required torque levels, and rotation speed all impact which thread type will best deliver sustained performance. For example, high-torque environments may benefit from the robust design of API NC threads, known for their ability to handle greater torsional stress. Conversely, applications needing quick assembly and disassembly might lean towards threads with fast-tapered designs.
In the process of thread selection, consultation with thread manufacturers or experts is invaluable. These professionals offer insights based on empirical data and field experience, ensuring that the chosen thread will fit seamlessly with existing equipment and operational conditions. A misstep in this selection process can lead to significant financial losses due to equipment damage or halted operations.
Maintaining thread integrity is another vital aspect of this arena. Regular inspection, proper storage, and adherence to recommended torque settings are essential practices. Using thread protectors during transportation and storage reduces the risk of physical damage, while lubrication can prevent galling and corrosion, thus prolonging thread life.
Ultimately, understanding the thread types and their specific applications is not just about machinery. It's about forging a path to more efficient, safe, and cost-effective drilling operations. Investing time in learning about different thread types and consulting with experts fosters an atmosphere of trust and reliability with stakeholders. This attention to detail not only safeguards assets but also increases the credibility of professionals within the industry, reinforcing the pillars of experience, expertise, authoritativeness, and trust.