Driving a ground rod is a critical task in ensuring proper electrical grounding for various applications, from residential homes to industrial complexes. Among the myriad methods available today, using a rotary hammer has gained traction for its efficiency and effectiveness. This article delves into the nuances of this approach, offering insights rooted in expert opinions, real-world experiences, and authoritative guidance to bolster its credibility and enhance its utility for users.
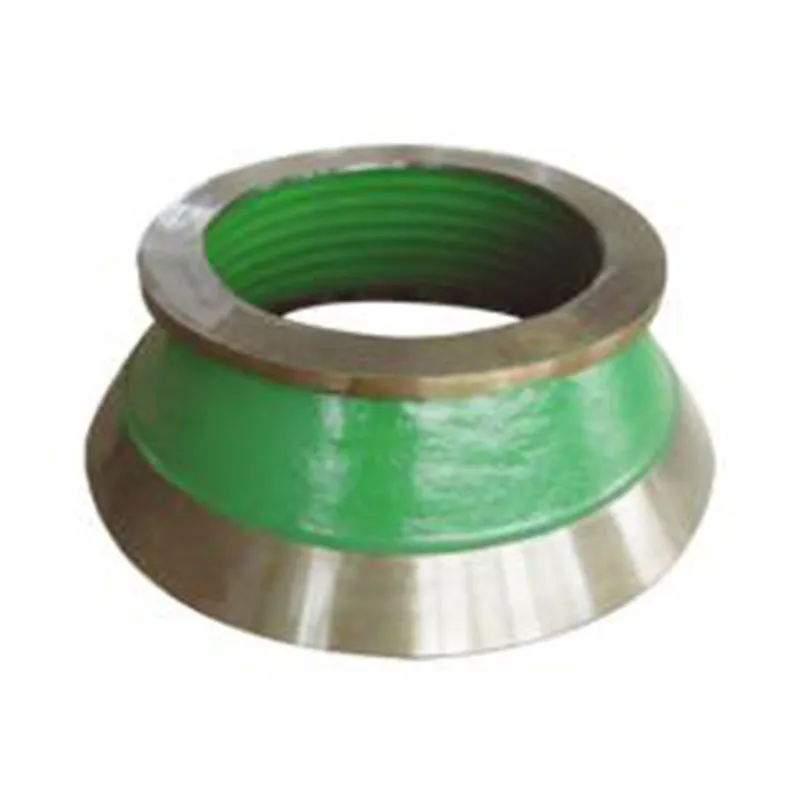
Grounding plays a pivotal role in safeguarding electrical systems by providing a path for fault currents and thereby minimizing the risk of electrical shock. Traditional methods, such as manual driving of ground rods with a sledgehammer, often present challenges, including physical fatigue, inefficiency, and uneven installation depths. Enter the rotary hammer—a tool that has revolutionized the process by merging functionality with precision.
A rotary hammer, distinct from a regular hammer drill, uses a piston mechanism to generate a powerful hammering action, making it particularly suitable for driving resilient materials like metal ground rods into tough terrains. With its robust build and ergonomic design, it significantly reduces the time and effort required to achieve optimal results.
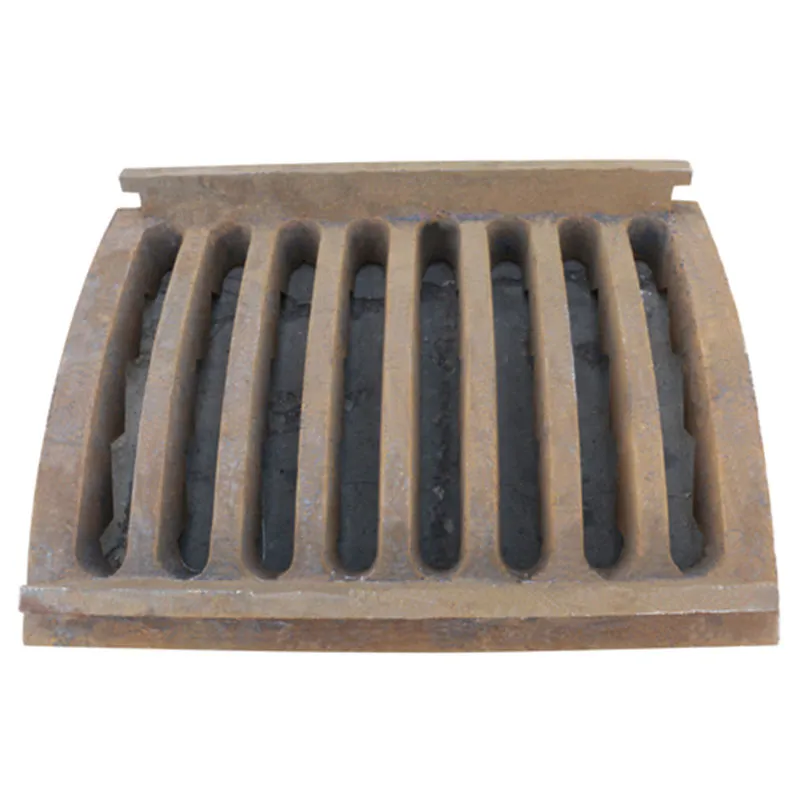
When opting for a rotary hammer to drive a ground rod, expertise in choosing the right attachment is paramount. The ground rod driver bit, specifically designed for this task, is essential. It fits into the tool's chuck seamlessly, allowing for steady pressure and consistent hammering action. This bit, typically forged from high-strength steel, is engineered to withstand the rigors of driving a rod deep into the earth, thus preventing wear and tear over extended use.
Real-world experiences underscore the benefits of this method. Electricians and contractors who have transitioned to using rotary hammers emphasize the precision and control it offers. Particularly in areas with rocky or compacted soil, a rotary hammer boasts the muscle to penetrate such challenging substrates where manual methods falter.
driving ground rod with rotary hammer
Safety, a cornerstone of trustworthiness, is inherently enhanced when using a rotary hammer. The controlled power minimises the risk of erratic movements that can occur with manual driving, reducing the likelihood of accidents or injuries. Moreover, contemporary rotary hammers are equipped with vibration control systems, further diminishing operator fatigue and enhancing user safety.
Economically, the adoption of a rotary hammer proves beneficial in the long run. While the initial investment may be higher than for traditional methods, the efficiency gained translates into reduced labor costs and quicker completion times for projects. This makes rotary hammers a cost-effective solution for both small-scale installations and larger, more demanding projects.
As expertise evolves,
so does the implementation of best practices in driving ground rods with a rotary hammer. Experts recommend conducting soil tests beforehand to determine the optimal depth and placement, ensuring effective grounding. Additionally, periodic inspections and maintenance of both the tool and the installed rods are advised to sustain performance and prolong lifespan.
Rounding out the experience, user manuals and manufacturer guidelines serve as authoritative resources, offering step-by-step instructions and safety protocols. Adhering to these enhances both the skillset of operators and the overall reliability of the grounding setup.
In conclusion, the use of a rotary hammer for driving ground rods is a method that combines expertise with innovative design to offer a superior solution in electrical grounding. Emphasizing precision, safety, and efficiency, it not only simplifies a traditionally labor-intensive task but does so with a professionalism that inspires confidence. As more practitioners embrace this approach, the benefits continue to multiply, marking the rotary hammer as an indispensable asset in the domain of electrical installations.