Drill rods are a cornerstone in the realm of drilling technology, playing a pivotal role in industries that range from mining to construction, and even geothermal energy exploitation. Understanding the material properties of drill rods is crucial for optimizing their performance, enhancing their longevity, and ensuring operational safety.
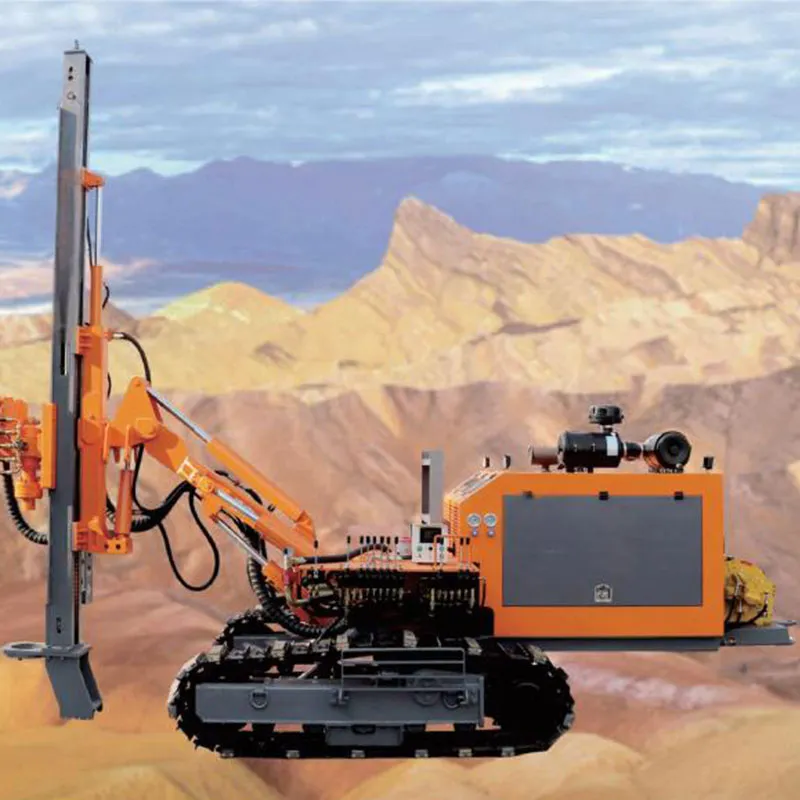
At the heart of drill rods are the materials used in their construction. Typically, high-grade alloy steels such as 4130 or 4140 are preferred due to their exceptional strength and durability. These alloys are known for their ability to endure high torque and tension, characteristics that are essential for resisting deformation under substantial loads. Their composition includes chromium and molybdenum, making these steels particularly hard and resistant to wear, a vital property when considering the abrasive environments in which drill rods often operate.
Heat treatment is another significant factor influencing the material properties of drill rods. Through processes like quenching and tempering, the mechanical properties of the steel can be significantly enhanced. Quenching increases the hardness and strength, whereas tempering ensures that the steel maintains a balance between hardness and toughness. This heat treatment process must be meticulously controlled, as improper heat treatment can lead to excessive brittleness, increasing the chances of rod failure.
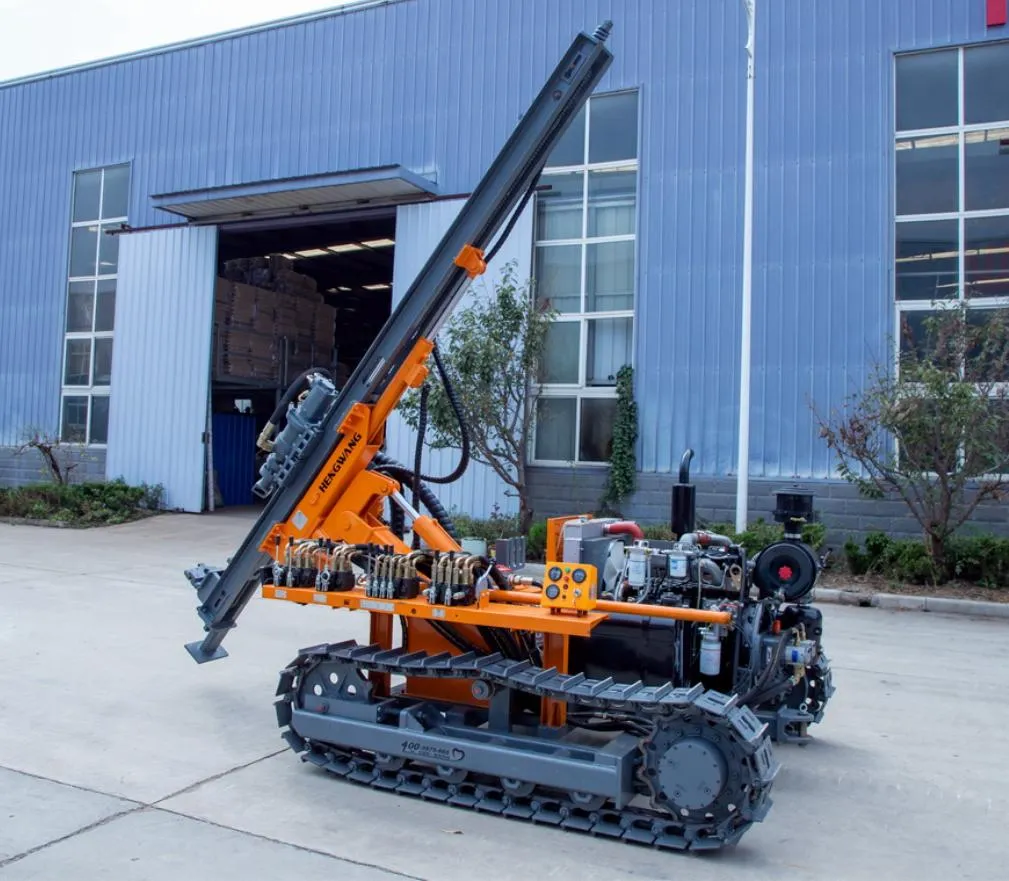
Corrosion resistance is often overlooked, yet it remains a critical property for drill rods, especially in corrosive environments or applications such as offshore drilling. Many drill rods are coated or treated chemically to enhance their resistance to corrosive elements such as water, salt, and various chemicals they might encounter. Techniques such as phosphating, galvanization, or using corrosion-resistant alloys play a pivotal role in extending the life span of the rods and maintaining their structural integrity.
The dimension and surface finish of these rods also contribute to their overall performance and durability. Precision in their diameter ensures that the energy is efficiently transferred from the drill to the bit, minimizing energy loss and enhancing drilling efficacy. Furthermore, a superior surface finish reduces friction when the rod operates inside a drill hole, lessening wear over time.
When considering drill rods, fatigue resistance is a crucial property, given the repetitive stress cycles they endure. Fatigue resistance can often dictate the service life of a drill rod. Manufacturers achieve improved fatigue resistance by employing specific alloy compositions and incorporating design improvements such as stress-relief grooves and surface peening. These enhancements mitigate the risks of fatigue fractures, which are one of the common failure modes for drill rods in demanding applications.
drill rod material properties
Reliability in extreme conditions is also mandatory in assessing the suitability of drill rod material properties. The ability of a drill rod to maintain its structural integrity in environments characterized by high temperatures, increased pressures, or severe mechanical shock defines its operational versatility. This reliability is often achieved through a combination of material selection, heat treatment, and surface engineering.
Furthermore, in high-precision applications like horizontal directional drilling (HDD), the mechanical property of flexibility may sometimes be as important as strength. This flexibility is crucial for allowing the drill to navigate around obstacles or alter the drilling direction without fracturing the rod. Specialty composite materials are sometimes integrated with steel to provide a strategic bend in the rod without compromising its overall strength.
Overall, the choice of material properties for drill rods directly impacts their performance and the efficiency of drilling operations. Optimal material selection not only serves economic interests by reducing downtime and maintenance costs but also supports safety measures by minimizing unexpected failures that could lead to catastrophic incidents.
As technology continues to evolve, smart materials and advanced composites are gradually finding their way into drill rod manufacturing, promising enhancements in performance that were once deemed unachievable. Future research and development into these areas will likely focus on further strengthening against fatigue, enhancing corrosion resistance, and improving overall energy efficiency in drilling operations.
The depth of understanding in drill rod material properties allows operators to maximize their rigs' capabilities, driving both innovation and efficiency across various industries. Addressing the intricate balance of these properties ensures that drill rods remain reliable, safe, and cost-effective, cementing their use in many modern engineering applications.