Crusher jaw plates are pivotal components in the mining and aggregate industries, where heavy-duty machinery is tasked with crushing massive rocks and ores into manageable sizes. These plates are crucial for the efficiency and longevity of crushers, making the selection and maintenance of jaw plates vital for production optimization.
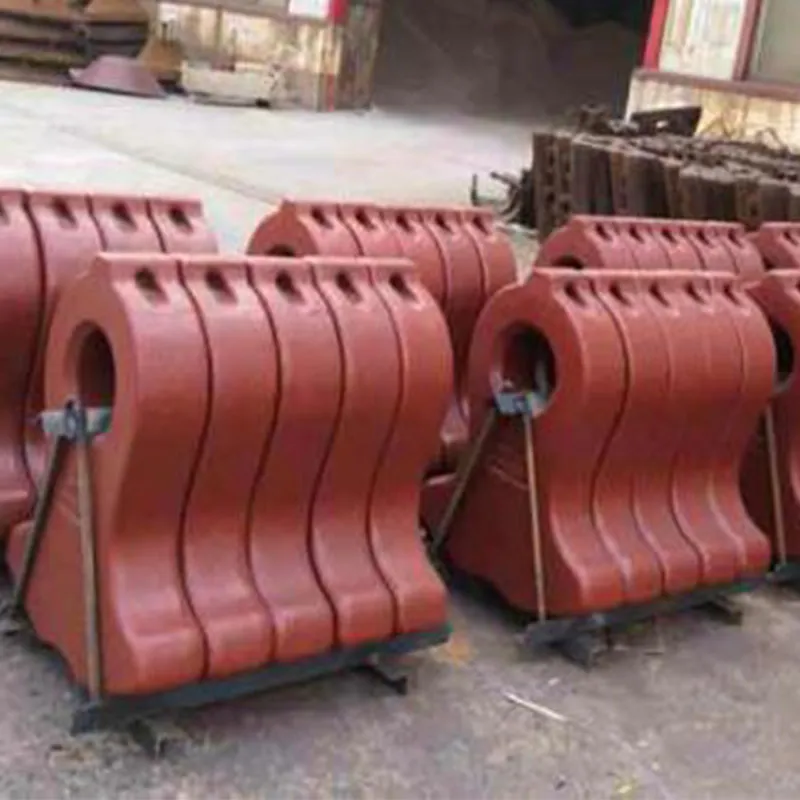
When choosing crusher jaw plates, the type of material being processed is the primary consideration.
Different materials, such as hard granite, slag, and soft limestone, each possess unique properties that influence their interaction with the jaw plates. For instance, harder materials demand jaw plates made from high manganese steel to withstand the substantial wear and tear. This material is known for its impact strength and resistance to abrasion, allowing the jaw plates to sustain high-impact conditions without compromising performance.
The design of the crusher jaw plate also influences performance. Curved and corrugated jaw plates offer increased surface area, enhancing the gripping action on aggregates and ensuring a better crush. Advanced computational simulations in design optimization allow for maximizing the power efficiency while minimizing wear. The right design offers increased throughput and uniform product size, which are critical for operational efficiency.
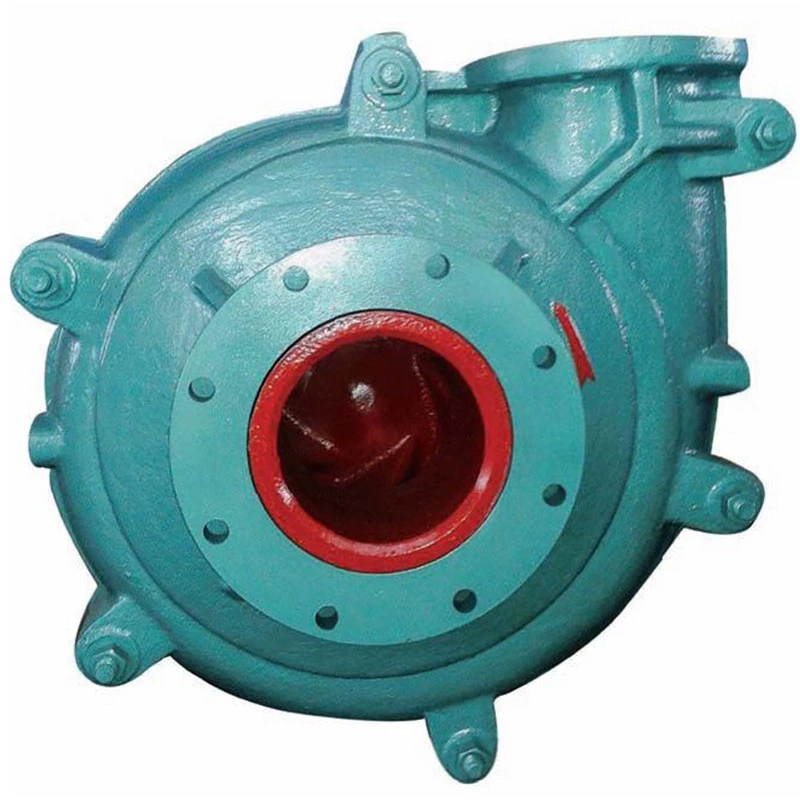
Proper installation and maintenance of jaw plates are essential for achieving optimal life expectancy and performance. Incorrect installation can lead to improper plate alignment, causing undue stress and premature wear. Regular maintenance, including the rotation of plates and monitoring of wear patterns, helps in predicting replacement schedules and avoiding unexpected downtime. Ensuring the correct torque on bolts and proper seating of plates can dramatically improve the lifespan of crusher jaw plates.
crusher jaw plate
It's also important to purchase jaw plates from reputable manufacturers who stand behind their products with warranties and support. Manufacturers who provide detailed wear analyses and material properties data add an extra layer of assurance. Additionally, manufacturers who invest in research and development often deliver enhanced jaw plate designs which contribute significantly to the efficiency of crushing operations.
User experience with crusher jaw plates points towards a strong preference for those that offer not only durability but also ease of replacement and minimal maintenance. User feedback reveals that quick-release designs and easily accessible components contribute substantially to operational smoothness and reduced downtime, which is crucial in high-production environments. Operators value jaw plates that provide consistent performance over extended periods and reduce the frequency of replacements, ultimately leading to cost savings and increased profitability.
Finally, leveraging digital platforms to share and gain reference from real-world case studies and testimonials about jaw plate performance can greatly aid in making informed purchasing decisions. Users who incorporate comprehensive feedback loops into their operations often report a higher satisfaction rate with their jaw plate performance. Such networks not only enhance trustworthiness but also promote continuous improvement and innovation within the industry.
In conclusion, the choice and maintenance of crusher jaw plates significantly impact the crushing performance and efficiency in mining operations. It is imperative to consider material compatibility, design, manufacturer credibility, and user experience when making decisions. Investing in the right jaw plates ensures enhanced performance, reduced operational costs, and reliable output, thus proving essential for sustained success in crushing operations.