Jaw plate crushers represent a paradigm of modern engineering and innovation, critical to operations in industries ranging from mining to recycling. By understanding the intricacies of these mighty machines, companies can optimize their use, gaining improved efficiency and cost savings. This article delves into the elements that make jaw plate crushers vital, as well as expert guidance on maximizing their use.
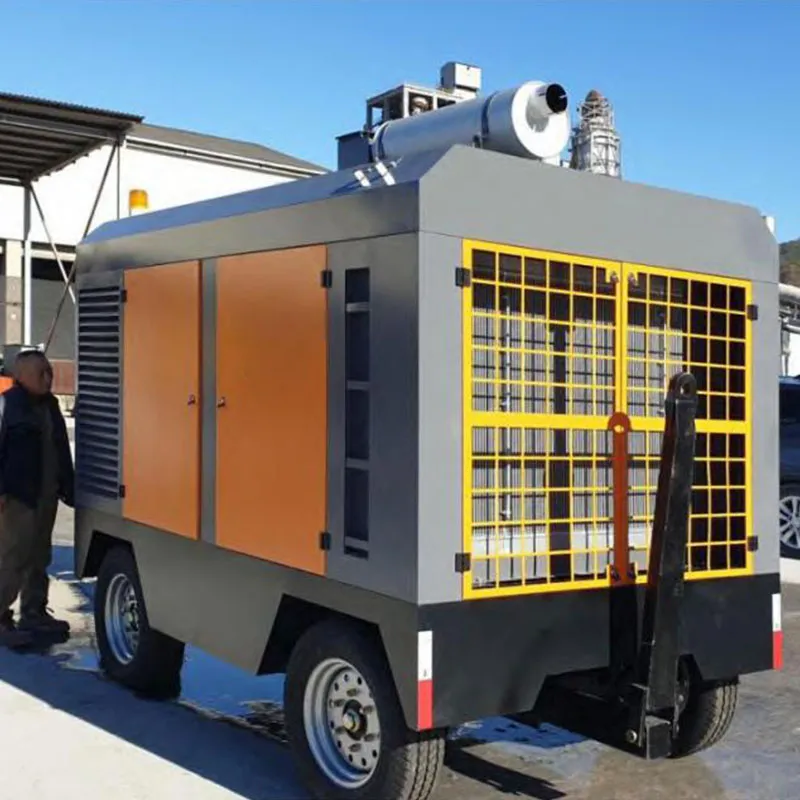
At the heart of a jaw plate crusher lies the jaw itself, an intricate component that demands a refined understanding of material science and engineering. The jaw plates, typically constructed from manganese steel due to its incredible wear-resistance and durability, play an instrumental role in the crushing process. By compressing materials against a fixed surface, the jaw plate pulverizes them, allowing for the processing of everything from concrete to granite with unparalleled efficiency.
Industries seeking to leverage jaw plate crushers must prioritize the maintenance and correct operation of these machines. Proper alignment is crucial to preventing uneven wear, which can lead to decreased efficiency and unexpected breakdowns. Regular inspections and adjustments, based on comprehensive data analytics, can help predict wear rates, allowing for timely interventions and prolonging the lifespan of the equipment.
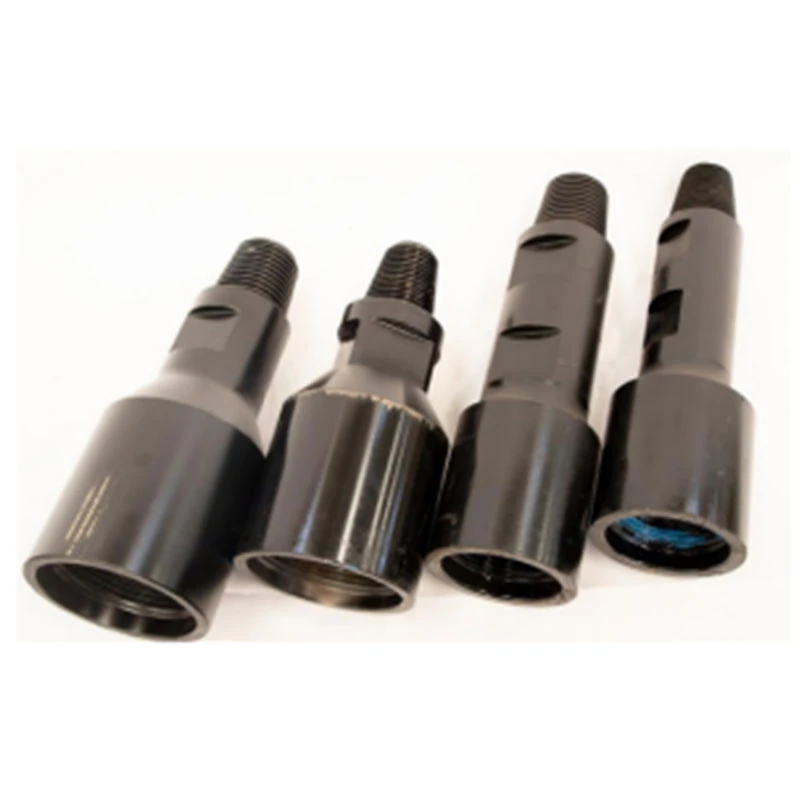
Companies can further enhance their operations by investing in customized jaw plates tailored to specific applications. These tailor-made solutions consider factors like material hardness and abrasiveness, offering improved performance by balancing wear life with crushing power. Furthermore, advancements in metallurgy can provide jaw plates with coatings or compositions that extend their lifespan even further, reducing the need for frequent replacements and offering a more economical option in the long run.
Authority in jaw plate crusher operation extends beyond simple maintenance. Professionals in the field advocate for a holistic approach, encompassing the full spectrum of necessary adjustments and optimizations. For instance, the feed mechanism plays an essential role. By regulating the size and rate of material fed into the crusher, companies can control the load exerted on the jaw plates, optimizing crusher performance and ensuring consistent output quality.
jaw plate crusher
Moreover, the integration of technology offers insights that can significantly enhance crusher operation. Utilizing tools such as advanced load sensors and predictive maintenance software can help in monitoring the stress levels of jaw plates and detecting potential faults before they lead to catastrophic failures. This positions companies at the cutting edge of operational efficiency, reducing downtime, and ensuring a continuous workflow.
In terms of environmental considerations, jaw plate crushers offer an opportunity for sustainable practices. By implementing recycling processes, companies can utilize these crushers to reclaim valuable materials, aligning operations with growing environmental standards and enhancing corporate social responsibility efforts.
Trust remains fundamental when procuring jaw plate crushers. Selecting reputable manufacturers who adhere to stringent quality control and industry standards is critical. These manufacturers not only supply durable equipment but also offer guidance on best practices and technical support, establishing a partnership that extends beyond transactional interactions.
Embrace advancements in jaw plate crusher technology to evolve operations. With an informed, expert approach focused on maintenance, customization, technological integration, and sustainable practice, companies can harness the full potential of these formidable machines. A commitment to excellence in these areas ensures that jaw plate crushers remain an indispensable tool across diverse industrial landscapes, promising sustained growth and success.