The vertical centrifugal pump, a pivotal component in many industrial systems, operates based on a set of fundamental principles that ensure efficiency and reliability. Its unique design and functioning have made it indispensable in sectors such as manufacturing, wastewater management, and energy production.
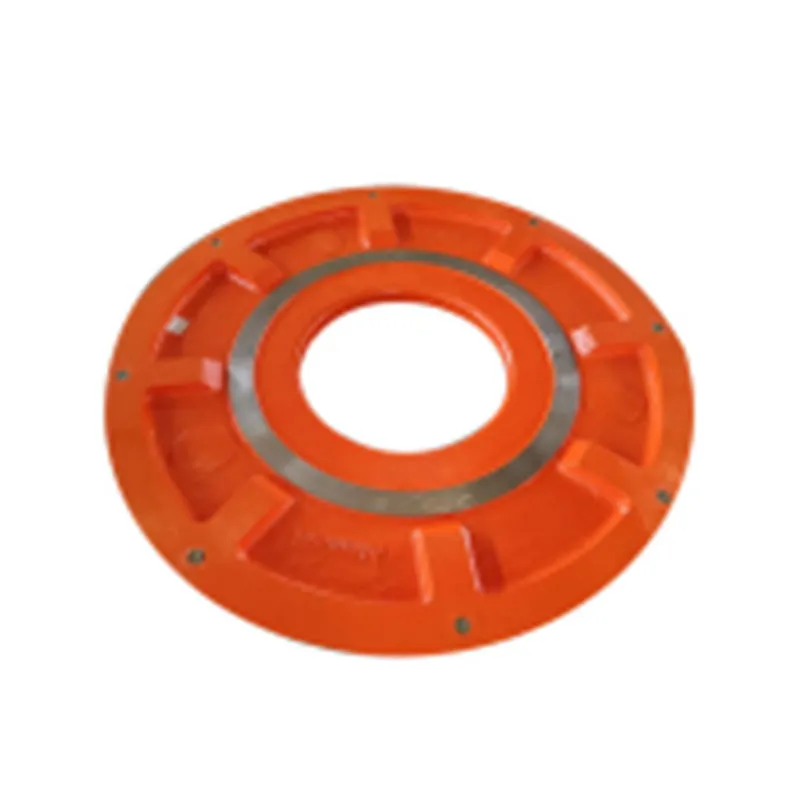
At the core of a vertical centrifugal pump's operation is Newton's Second Law of Motion, which guides the transformation of mechanical energy into kinetic energy. This transformation begins when the pump's impeller, a central rotating component, is set into motion by a motor. As the impeller spins, the fluid present in the pump casing is forced outward due to centrifugal force. This outward movement of fluid creates a region of low pressure at the impeller's center, allowing more fluid to flow into the pump from the source. Subsequently, the fluid accelerates through the impeller's channels and is expelled through the discharge outlet at high velocity.
One of the defining characteristics of vertical centrifugal pumps is their vertical alignment, which offers significant advantages in specific applications. The vertical orientation allows for a smaller footprint, making them ideal for environments where space is limited. Additionally, their design facilitates easy maintenance, as the motor and critical components are located above the fluid being pumped, reducing the risk of damage from flooding or contamination.

Another critical aspect of vertical centrifugal pumps is their flexibility and adaptability. These pumps can handle a wide range of fluid types, from water and oils to corrosive chemicals and slurries. This adaptability is due, in part, to materials used in construction, such as stainless steel, cast iron, and specialized alloys, which are selected based on the fluid's properties to enhance durability and performance.
vertical centrifugal pump working principle
Efficiency in the operation of vertical centrifugal pumps is paramount. Modern advancements have led to the development of variable frequency drives (VFDs) that allow for precise control of the pump's speed and pressure output. This technological integration not only optimizes energy consumption but also prolongs the lifespan of the pump by reducing wear on internal components.
Furthermore, the design of the impeller is crucial in determining the pump's performance characteristics. Engineers often employ computational fluid dynamics (CFD) simulations to refine impeller shapes and sizes, ensuring the desired flow rates and head are achieved with minimal energy wastage. Such expertise underscores the scientific rigor involved in the production of these pumps and highlights the importance of selecting a pump tailored to specific operational needs.
Trust in vertical centrifugal pumps comes from their proven track record and the authority of leading manufacturers who have continuously refined their designs over decades. Brands with ISO certifications, adhering to rigorous international standards, provide the assurance needed by industries worldwide, further reinforcing the reliability of these pumping solutions.
In conclusion, vertical centrifugal pumps are an essential component in various industries, owing to their robust design, adaptability, and efficiency. Their ability to handle diverse fluids and conditions underscores their role as a cornerstone in operational processes. Trust in their capability is backed by years of technological advancement and expert design, ensuring that industries operate smoothly and efficiently.