Mud pumps are a crucial component in the drilling industry, primarily used to circulate drilling fluid, often referred to as mud, to the drill bit and back up to the surface. This process is essential for maintaining pressure in the well, cooling the drill bit, and carrying the drill cuttings to the surface. Understanding the different types of mud pumps and their applications can significantly impact the efficiency and success of drilling operations.
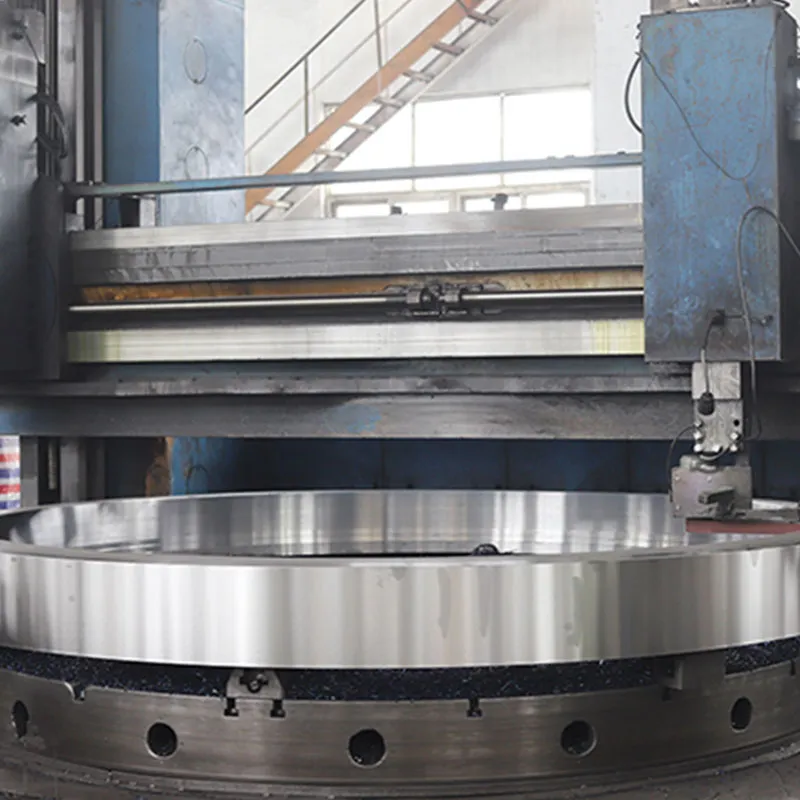
One of the most common types of mud pumps is the reciprocating piston/plunger pump, which is subdivided into various categories based on their configuration, mechanism, and capabilities.
1. Triplex Mud Pumps
Triplex mud pumps have three pistons or plungers that work in a reciprocating motion to circulate the drilling fluid. As the most commonly used mud pumps, they are praised for their efficiency, compact design, and relatively lightweight construction. Their simple mechanical structure allows for easier maintenance and repair, reducing downtime during drilling operations. Triplex pumps are ideal for medium to high-pressure applications, making them versatile across different drilling scenarios.
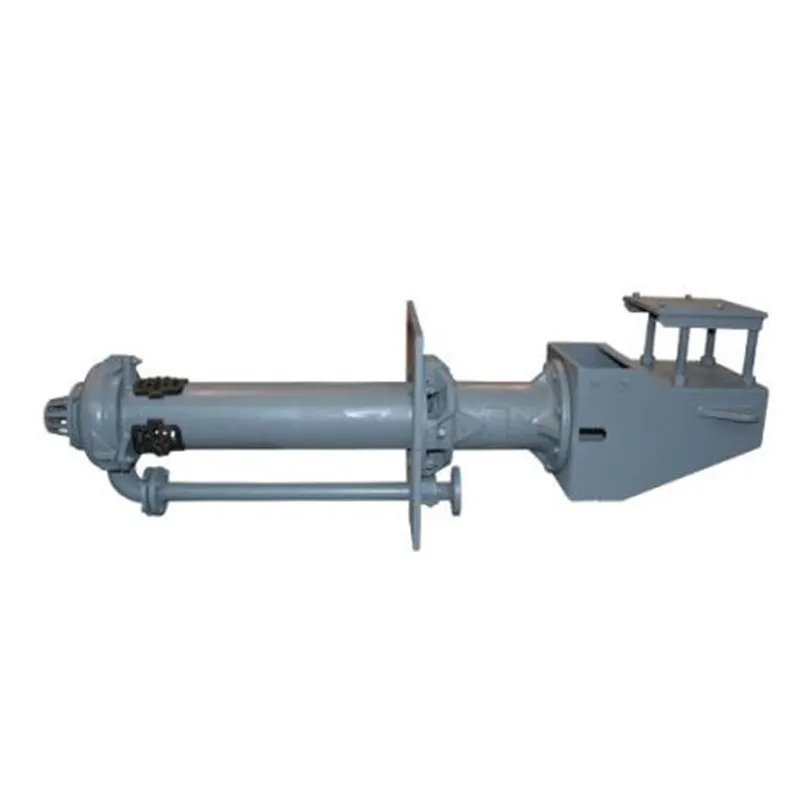
2. Duplex Mud Pumps
Duplex mud pumps feature two pistons or plungers, capable of moving large volumes of fluid but operating at lower pressures compared to triplex pumps. Their robust and durable build makes them suitable for well drilling and other demanding industrial processes requiring substantial fluid movement. Despite their larger size and weight, duplex pumps are preferred in operations where fluid volume is prioritized over pressure.
3. Quintuplex Mud Pumps
For drilling operations that demand even higher pressure and efficiency, quintuplex mud pumps, equipped with five pistons or plungers, are an ideal choice. These pumps deliver smoother fluid flow with less pulsation, offering an advanced solution for high-pressure demands. The quintuplex configuration provides enhanced operational smoothness and consistent output, reducing the stress on the drill bit and other drilling components.
tipos de bombas de lodo
When selecting a mud pump, several factors must be considered, including the nature of the drilling operation, required pressure, fluid volume, and environmental conditions. Each type of pump has its advantages and is suited to specific tasks, making expert assessment crucial in determining the optimal choice.
The material used in constructing mud pumps also affects their performance and longevity. High-quality, corrosion-resistant materials are essential to withstand the harsh, abrasive nature of drilling fluids and extend the lifespan of the pumps. Stainless steel and other hard alloys are commonly used to enhance durability and reliability.
Another critical consideration is the pump's maintenance requirements. Regular inspection and maintenance routines are vital in preventing breakdowns and ensuring continuous operation. Factors such as easy accessibility to key components, availability of spare parts, and the technical expertise required for maintenance play a significant role in the overall efficiency and operational costs of mud pumps.
Innovations in mud pump technology are focused on improving efficiency and reducing environmental impact. Eco-friendly options that minimize fluid wastage and energy consumption are gaining popularity in the industry. Implementing advanced monitoring systems to track performance and anticipate maintenance needs is also a growing trend, enabling proactive management and optimization of drilling equipment.
In conclusion, a comprehensive understanding of the various types of mud pumps, along with careful consideration of operational requirements and conditions, is critical for optimizing drilling efficiency. Collaborating with industry experts to evaluate and select the appropriate equipment can lead to enhanced performance and reduced operational costs, thereby contributing to the success and profitability of drilling projects.