The swing jaw plate is an essential component in the complex mechanism of a jaw crusher, often employed in aggregate and mining sectors for its efficient breaking of rocks and minerals. Understanding the detailed workings and importance of the swing jaw plate can significantly enhance the operational efficiency and durability of the machinery, which subsequently leads to cost savings and improved productivity.
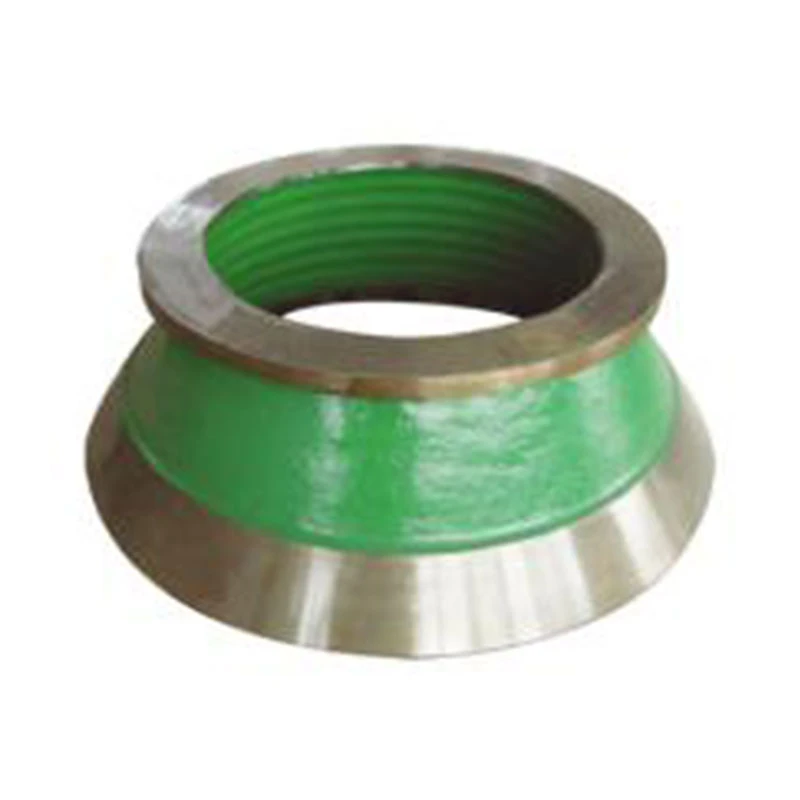
The operation of a jaw crusher hinges on its ability to crush materials using compressive force generated by two jaw plates the fixed jaw plate and the swing jaw plate. The latter, often referred to as the movable jaw, oscillates and exerts pressure against the fixed plate, prompting the material fed into the crusher to fracture upon impact. This principled yet straightforward mechanism underpins the critical need for a robust and efficiently designed swing jaw plate.
A key aspect of swing jaw plates is their composition. Typically crafted from high-manganese steel, these plates are renowned for their superior toughness and resistance to wear and tear – factors indispensable to enduring the harsh environments of ore and rock crushing operations. The high manganese content provides a reduction in brittleness coupled with the ability to work-harden, which means the plate becomes progressively harder with continuous use.
This unique characteristic prolongs the life of the plate considerably.
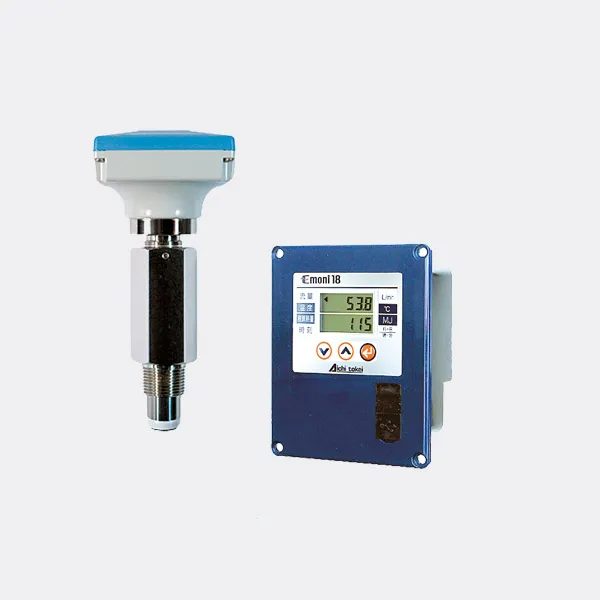
Another feature that sets high-quality swing jaw plates apart is their adaptability. They can be customized based on specific operational requirements or material compositions, allowing for diverse applications ranging from soft limestone to hard granite. Engineers and operators prioritize the precise calibration of jaw plates based on the material to be crushed in order to optimize efficiency and minimize unnecessary strain on the machinery.
swing jaw plate
The design considerations of the jaw plate play a pivotal role in its functionality and upkeep. Angles, or the nip angle between the plates, must be finely tuned for optimal performance. A properly calculated nip angle ensures that the material is efficiently gripped and crushed, preventing issues such as excessive wear or slippage. Subsequently, the key to maximizing crusher productivity often lies in simple, yet diligent, attention to these mechanical nuances.
Durability and maintenance are equally vital when evaluating swing jaw plates. Regular inspections should be incorporated into standard operating procedures to identify any early signs of wear, cracks, or distortion. Operators trained in the subtleties of swing jaw plate wear patterns and maintenance can extend the lifespan of the equipment profoundly, avoiding costly downtime. Moreover, interchangeable plates underscore the practicality of modern jaw crushers, as this functionality allows for quick replacements, ensuring that operations continue seamlessly despite wear-related setbacks.
In the realm of innovation, ongoing advancements in metallurgy and design have ushered in new possibilities for swing jaw plate manufacturing. Novel composites and heat-treatment processes are being explored, targeting improved performance and further reduction in operational costs. Intelligent design software has become an invaluable tool for engineers, refining dimensions and stress distribution across the plates to usher in a new era of efficiency and reliability in jaw crushers.
Whether approached from the standpoint of engineering design or operational application, the swing jaw plate represents an intriguing convergence of material science, mechanical engineering, and practicality. It exemplifies the necessity of each component within mining equipment, from its role in roasting rock slabs to its subtle influence on the economic bottom line. Optimization and innovation in swing jaw plate technology perpetuate its undisputed authority and trustworthiness as a cornerstone in crushing processes. Thus, with a constant emphasis on experience, expertise, authoritativeness, and trustworthiness, investing in the right swing jaw plate brings unparalleled returns in productivity, reliability, and operational excellence.