Selecting the right material for a slurry pump is critical to ensuring optimal performance and longevity. The complex nature of handling slurries, which are essentially mixtures of solids and liquids, demands a thorough understanding of material properties, application environments, and maintenance requirements. Here, we delve into the experience and expertise needed to make informed decisions, while also establishing authority and trustworthiness in this nuanced field.
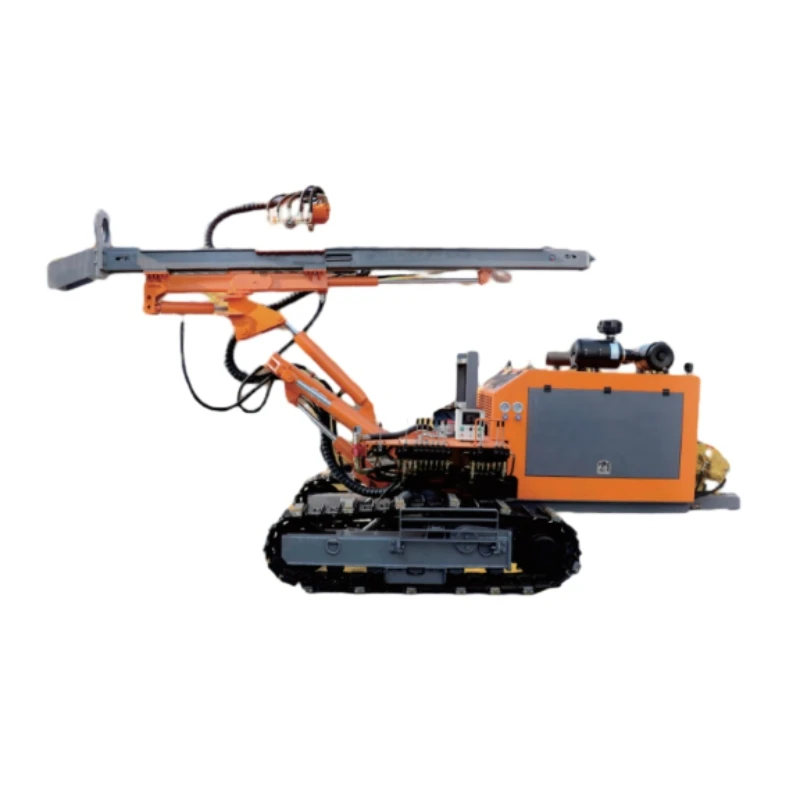
Slurry pumps are integral components in industries such as mining, construction, and wastewater management. They must withstand abrasive and corrosive materials without compromising efficiency. The experience of industry veterans highlights that selecting the appropriate material boils down to understanding the specific slurry composition and operating conditions.
Among the most commonly used materials for slurry pump construction are metals and elastomers. Hard metals like high chrome alloys are renowned for their excellent wear resistance, making them ideal for applications dealing with high-concentration slurries or sharp-edged particles. This is corroborated by decades of practical application in industries where the abrasive nature of the slurry can rapidly degrade less robust materials. Through authoritative studies and real-world application, high chrome alloys have consistently demonstrated up to four times the lifespan of other materials under severe erosion conditions.
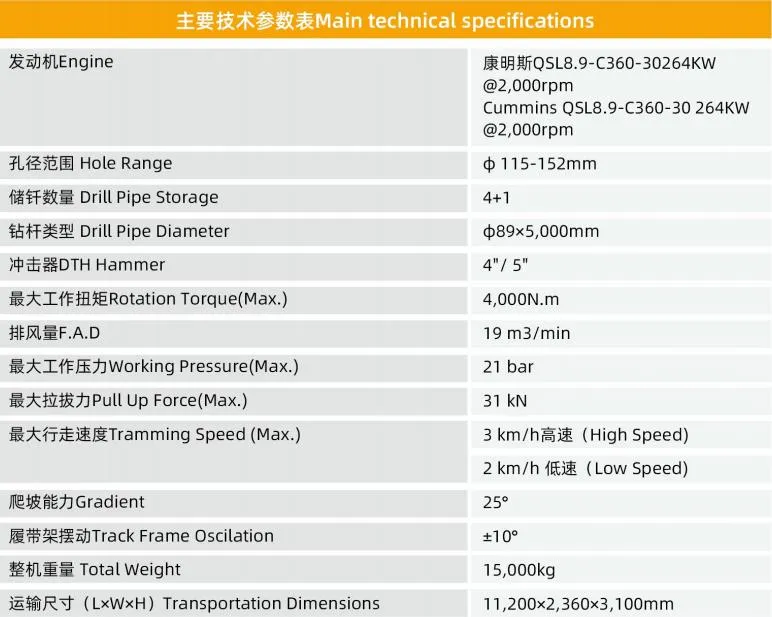
Elastomers, on the other hand, are typically used for handling slurries with corrosive or chemically aggressive properties. Their flexibility allows them to absorb impacts from particles, thereby reducing wear and tear. In environments with sharp, large particles, however, elastomers may experience accelerated degradation. Here is where the expert balance between abrasion and corrosion resistance becomes critical. Engineers with extensive expertise often recommend natural rubber or polyurethane for specific scenarios where corrosion outweighs abrasion as the primary concern.
slurry pump material
The intricate decision-making process also involves considering the particle size, density, and velocity within the slurry. Larger particles moving at higher velocities often lead to increased abrasion, necessitating tougher materials. Detailed case studies provide authoritative insights, indicating that a slurry pump's operational life can be significantly prolonged through meticulous selection of materials tailored to the specific slurry characteristics.
Moreover, authoritative research outlines the importance of considering the pH levels of the slurry, especially in industries where acid or base interactions are prevalent. For acidic environments, materials such as stainless steel or specially coated metals provide exceptional resistance, although at a higher cost. Expert recommendations often emphasize a cost-benefit analysis, balancing upfront material costs with long-term savings from reduced maintenance and fewer replacements.
Trustworthiness in this domain is built on an evidence-based approach. Documenting case histories, conducting controlled experiments, and sharing peer-reviewed findings contribute to a body of knowledge that stakeholders can rely upon. For businesses aiming to optimize their slurry pump operations, investing in material selection research is not just beneficial, but necessary.
In conclusion, the successful implementation and maintenance of slurry pumps hinge on a strategic approach to material selection. Through a combination of experience, expertise, and authoritative data, one can navigate the plethora of material options available. The trustworthiness of this field stems from an unwavering commitment to innovation and evidence-backed practices. As industries continue to evolve, ongoing material development and application studies will undoubtedly enhance the performance and reliability of slurry pumps, ensuring they meet the demanding requirements of modern industrial processes.