Designing a slurry pump requires a thorough understanding of both the fundamental principles of fluid dynamics and the specific requirements of transporting viscous, abrasive materials. Precision in design not only optimizes performance but also extends the pump's lifecycle, making it an invaluable tool in industries like mining, wastewater treatment, and construction. Drawing from decades of expertise, the following considerations form the bedrock of effective slurry pump design.
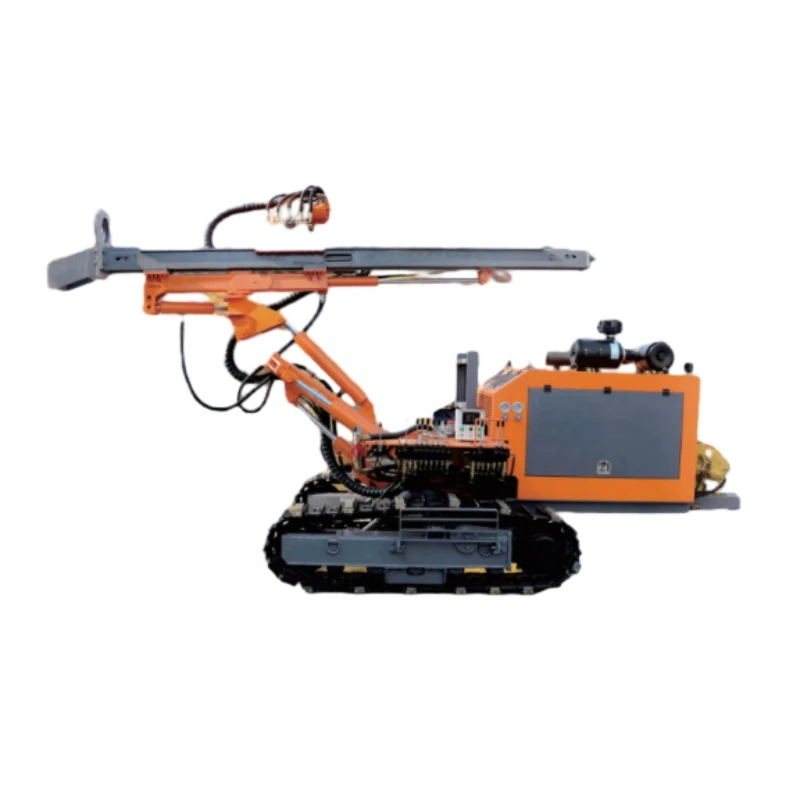
A critical aspect of slurry pump design is the selection of appropriate materials. Given the abrasive nature of slurry mixtures, materials must withstand considerable wear and tear. Metallic alloys with high chromium content, cost-effective due to their durability, are often favored for components like impellers and liners. Alternatively, elastomers like natural rubber offer exceptional resistance to certain corrosive compounds found in slurry, though they may not sustain extensive abrasion. The selection should thus be a nuanced decision, balancing the chemical properties of the slurry with expected operational conditions.
Equally crucial is the geometric design of the pump components. The impeller, often regarded as the heart of the pump, requires meticulous attention. Backward-curved vanes can reduce the speed of abrasive particles, minimizing erosion while enhancing the pump's energy efficiency. The impeller clearance—the space between the impeller and the casing—must also be optimized to prevent solids from settling and reducing performance. Small clearances minimize leakage but can lead to blockages if improperly spec'd, underscoring the need for precision.
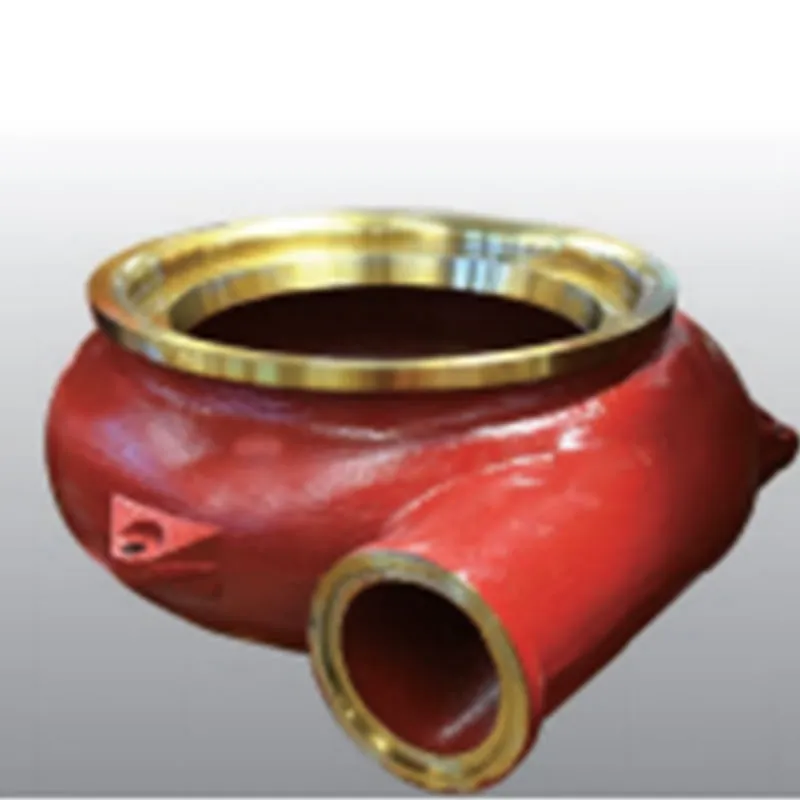
Hydraulics play a pivotal role in ensuring the pump delivers the required flow rates while maintaining pressure. Computational Fluid Dynamics (CFD) has revolutionized slurry pump design, allowing engineers to simulate conditions and prevent issues before they arise in practice. By adjusting variables such as the impeller diameter and the volute casing shape, designers can fine-tune the pump’s head and efficiency curves, ensuring optimal operation across varying loads and speeds.
slurry pump design
A sophisticated understanding of operational dynamics underpins successful slurry pump implementation. The Net Positive Suction Head (NPSH) must exceed the minimum required to avoid cavitation, a phenomenon that can severely damage the pump. Designers must account for factors like the slurry's specific gravity, which affects pressure calculations. Additionally, the piping system's layout, including its length and diameter, influences the total head required and should be incorporated early in the design phase.
Reliability in harsh environments predicates ongoing maintenance plans as part of the design strategy. Features like adjustable impeller spacing and replaceable liners facilitate more straightforward maintenance, extending the pump's lifecycle. Additionally, integrating sensors for conditions such as vibration and pressure allows real-time monitoring, enabling preventative measures over reactive repairs.
Ultimately, the integrity of a slurry pump design rests on combining in-depth material knowledge, advanced computational techniques, and a strategic understanding of operational parameters. The longevity and efficiency of these pumps directly correlate with how well these elements are harmonized. Through expert design and proactive maintenance planning, industries can achieve seamless operations, ensuring the reliability and effectiveness of their slurry transport systems.