Choosing the right slurry pump impeller is crucial for the performance and longevity of your pumping system, especially in industries handling abrasive, highly viscous, or chemically aggressive fluids. Understanding the intricacies of impellers can mean the difference between prolonged equipment life and frequent maintenance shutdowns. Leveraging decades of experience, industry expertise, and reliable data, we explore the key aspects involved in selecting, operating, and maintaining slurry pump impellers.

Slurry pumps are engineered to handle abrasive mixtures which pose unique challenges compared to standard water pumps. Within these systems, the impeller plays a pivotal role. It is the heart of the pump, responsible for moving the slurry and impacting factors like flow rate, efficiency, and wear. The effectiveness of a slurry pump is highly dependent on the impeller's characteristics, which include material, design, and size.
Material Matters
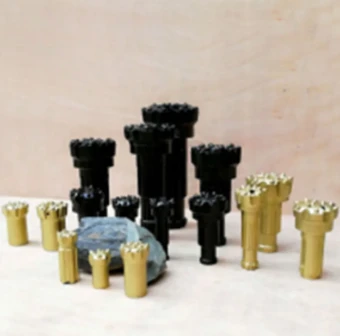
Material selection for slurry pump impellers is a critical consideration. Hard metals such as high-chrome alloys and elastomers like rubber are commonly used based on the slurry’s nature. For instance, high-chrome alloys with around 25-30% chromium offer superior wear resistance in handling coarse particles. On the other hand, rubber impellers or those made with elastomers are better suited for smaller, sharp-edged particulates, reducing wear by absorbing impact. Understanding the material compatibility ensures longevity and efficient pumping, reducing operational costs significantly.
Design Insight
The design of the impeller is another vital factor. Slurry pump impellers come in various designs closed, semi-open,
and open impellers. Closed impellers are known for high efficiency while offering secure containment of the slurry, ideal for denser mixes. Semi-open impellers provide easier access for inspection and maintenance, a choice for medium-density slurries where occasional clogging occurs. Open impellers are best suited for slurries with large or fibrous particulates to minimize blockages. Thus, selecting the right design influences operational efficacy, reducing downtime and maintenance efforts.
Size and Efficiency
slurry pump impeller
Impeller size impacts the flow rate and the head produced by the pump. A larger impeller increases the head and can handle higher flow rates, which is crucial for applications requiring high throughput. However, a balance needs to be maintained to prevent excessive power consumption and wear. Proper sizing involves understanding the system requirements and working closely with suppliers or industry experts to ensure optimal performance. Collaboration with experts enhances not only the precision of selection but also offers insights into operational adjustments required to maintain efficiency.
Operational Expertise
The operational conditions under which the slurry pump impeller works also significantly affect its performance. Factors such as rotational speed and the abrasive nature of the slurry need careful monitoring. Ensuring the pump operates close to its Best Efficiency Point (BEP) can prevent premature wear and failures. Utilizing data analytics and predictive maintenance tools is advised to monitor impeller wear patterns, endure reliable operation, and plan timely interventions. Expert guidance can aid in calibrating these operational parameters, offering a blend of technology and industry knowledge for enhanced pump longevity.
Trust Through Trials
Building expertise and trustworthiness involves a continuous loop of testing, feedback, and adjustments. Field trials and feedback loops with customers help fine-tune the impeller material and design choices across diverse applications. Engaging with user feedback ensures developments are not just reactive but proactive, improving upon current designs and materials to meet emerging challenges. It is through such iterative processes that confident, authoritative recommendations and solutions for slurry pumps are developed, providing a trusted resource for clients across the industry.
In conclusion, the successful implementation of a slurry pump system with an efficient impeller is a multifaceted task requiring in-depth knowledge and expertise. By focusing on material selection, thoughtful design, proper sizing, vigilant operation, and continuous improvement through field feedback, industries can ensure their pumping systems are robust, efficient, and reliable. Engaging with experts who provide tailored solutions based on empirical data and real-world tests can make all the difference in achieving optimal performance and customer satisfaction.