Slurry pumps are critical components in various industrial applications, mainly designed for transporting abrasive and corrosive slurry mediums. An intricate understanding of the slurry pump diagram is essential for ensuring optimal performance, reduced downtime, and prolonged equipment lifespan. This article delves deep into the anatomy and operational nuances of slurry pumps, underscoring experience, expertise, authoritativeness, and trustworthiness in the field.

A slurry pump differs significantly from conventional pumps due to its robust construction and unique working principle. The diagram of a slurry pump typically emphasizes its vital parts, which include the casing, impeller, shaft, shaft seal, bearings, and drive arrangement. Each component is engineered to handle the rigors of slurry transportation.
The casing is predominantly made of high-quality cast iron, designed to withstand the harshest of wear conditions. Its primary function is to enclose the pump chamber and provide an internal path for the slurry. The design of the casing often reflects the operational demands, such as pressure handling capability and the type of slurry transported.
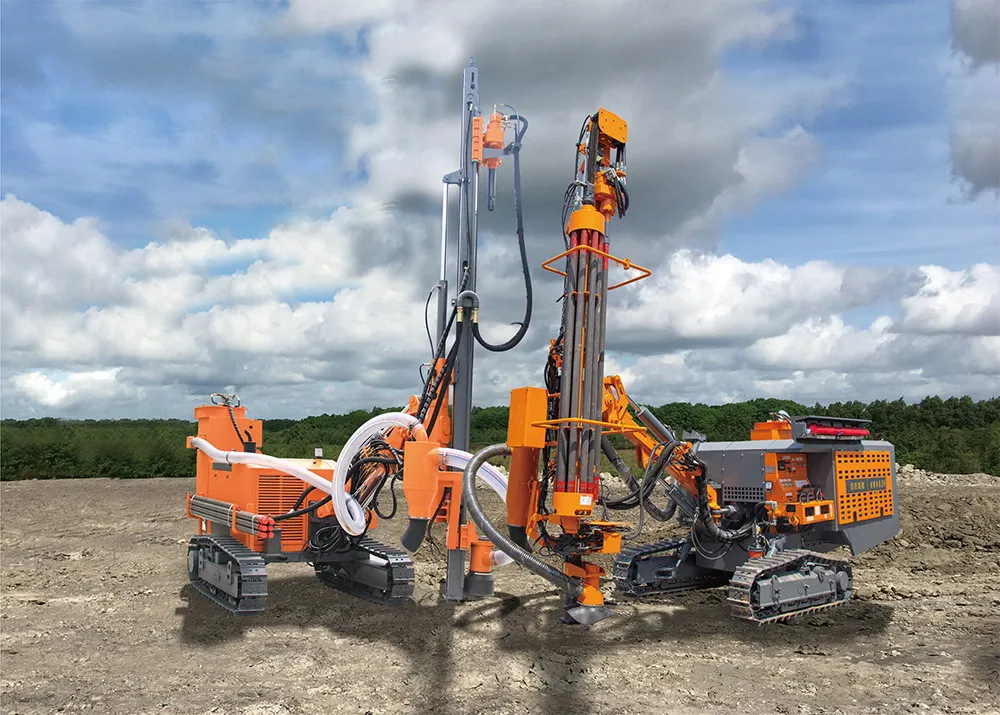
The impeller, often regarded as the heart of the slurry pump, is crafted from wear-resistant material. Its design directly influences the pump’s efficiency. An expertly engineered impeller enhances not just the hydraulic performance but also the pump's ability to process more challenging slurries. Advanced impeller designs may include open, enclosed, or semi-enclosed types, each offering unique advantages based on application.
Shaft and bearings are the mechanical backbone, holding the impeller and connecting to the drive mechanism. High-grade steel shafts are used to ensure minimal deflection and optimal alignment, effectively reducing wear on bearings and prolonging service intervals. Bearings, on the other hand, are critical for maintaining mechanical stability and minimizing friction during operation.
Shaft seals are paramount, preventing slurry from leaking out of the pump housing. Depending on the operational environment and slurry type, mechanical seals, packing seals, or expeller seals might be employed. Choosing the correct seal type is crucial, and expertise in this area can significantly improve pump reliability and reduce maintenance costs.
slurry pump diagram
The drive arrangement, which typically involves electric motors, governs the pump's power delivery. Ensuring the drive system’s compatibility with the pump's requirements can enhance performance and energy efficiency. Variable speed drives are often integrated, allowing operators to optimize pump operations based on real-time demands.
Operational expertise extends beyond just knowing the components; it encompasses understanding the dynamic behavior of slurry within the system. Flow rate, pressure head, and particle abrasion are factors requiring careful analysis and adjustment. Mastery in these variables not only boosts pump efficiency but also minimizes potential hazards like cavitation and erosion.
Authoritativeness in slurry pump technology is often demonstrated by adhering to industry standards, such as those outlined by the Hydraulic Institute or ISO. These standards ensure that the design and operation of slurry pumps meet stringent safety and performance criteria.
Trustworthiness is fostered by continuous monitoring and routine maintenance. An asset management strategy emphasizing predictive maintenance can detect anomalies early, thus preventing costly failures and downtime. In-field experiences often highlight that trust in slurry pump systems stems from an unwavering commitment to quality assurance practices.
In conclusion, understanding the intricate slurry pump diagram is not merely an academic exercise but a practical necessity rooted in industrial reality. By fostering expertise, demonstrating authority, and building trust, professionals can ensure that their slurry pump systems operate efficiently and reliably, ultimately driving productivity and success for their operations.