Rolling mill chocks, a vital component in the machinery of steel manufacturing, are pivotal in ensuring the efficiency and durability of rolling mills. Their significance cannot be overstated, as they bear the brunt of immense pressures and harsh operating conditions, thus requiring meticulous engineering and expert knowledge.
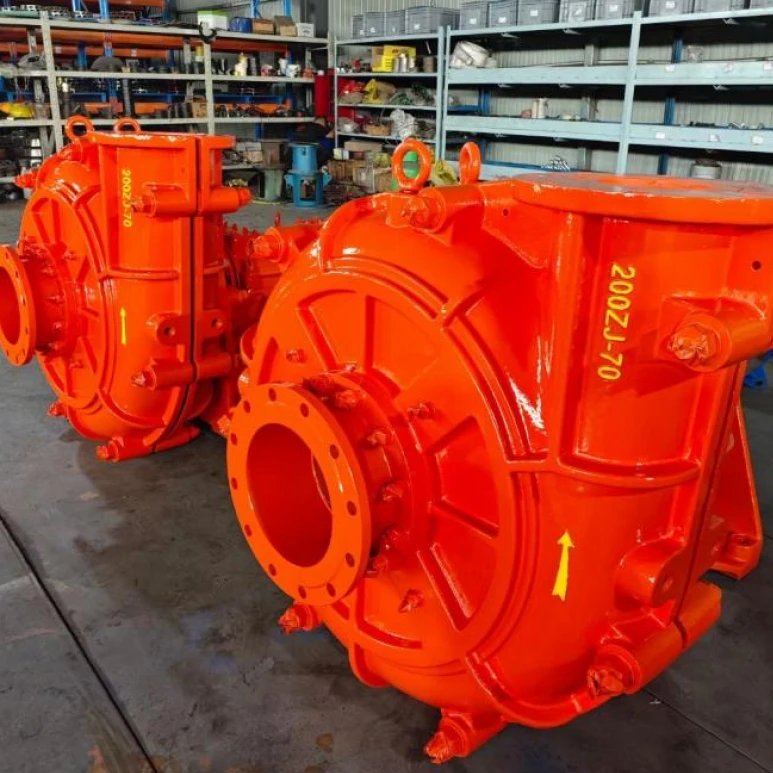
When delving into the realm of rolling mill chocks, one must appreciate the intricate balance between design, materials, and functionality. A robust understanding of these elements is essential for any manufacturer aiming to optimize their steel production processes. From experienced engineers to seasoned operators, the consensus is clear the quality of these components directly influences the output and longevity of the mills they serve.
Experience in handling rolling mill chocks reveals that the selection of materials plays a critical role. Typically made from high-grade cast steel or nodular cast iron, these chocks are engineered to withstand extreme conditions, including high temperatures and constant impact. Those with deep expertise in metallurgy are constantly exploring innovative materials that offer enhanced resistance to wear and tear, thereby extending the lifespan of these components and, by extension, the mills they operate within.
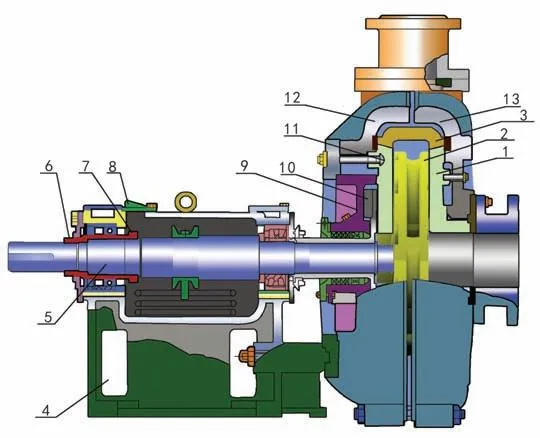
The manufacturing process of rolling mill chocks demands precision and adherence to stringent quality standards. Advanced CNC machining techniques are employed to achieve the exacting tolerances required for seamless operation. Professionals in this field stress the importance of rigorous testing and quality assurance protocols, which ensure that each chock can meet the demands of high-speed rolling conditions without succumbing to structural failures.
rolling mill chocks
From an expertise standpoint, the design of rolling mill chocks is continually evolving. Design engineers leverage cutting-edge CAD software to simulate operational stresses and optimize the geometry of each chock for maximum performance. These simulations help in predicting potential failure modes, allowing for preemptive design modifications that enhance reliability and efficiency. Such forward-thinking approaches underscore the expert-level understanding required to innovate within this specialized field.
Authoritative voices in steel production acknowledge that the performance of rolling mill chocks can significantly impact the operational efficiency of entire rolling mill systems. This recognition has led to strategic investments in research and development, driving technological advancements that benefit the whole industry. Industry seminars and papers frequently highlight case studies where improvements in chock technology have led to marked increases in throughput and reductions in maintenance costs, establishing a direct correlation between chock performance and operational success.
Trustworthiness in this context is underscored by the partnerships between rolling mill operators and reputable chock manufacturers. Trust is built through a transparent supply chain, showcasing a commitment to ethical sourcing of materials and adherence to environmental standards. Leading manufacturers provide comprehensive documentation and certification for their chocks, offering assurance that these products meet or exceed international industry standards.
In conclusion, the critical role of rolling mill chocks in steel manufacturing cannot be underestimated. Their impact on the efficiency, reliability, and overall success of rolling mills highlights the need for a deep, expert understanding of their design and production. For those in the industry, staying abreast of the latest developments in chock technology is not just beneficial; it's essential for maintaining a competitive edge in an increasingly demanding market. The synthesis of experience, expertise, authoritative knowledge, and trustworthiness defines the nuanced landscape of rolling mill chocks, positioning them as a cornerstone of modern rolling mill operations.