In the industry of mineral processing and recycling, the efficiency and longevity of the equipment hinge significantly on the small yet crucial components, such as the crusher liner. Specifically, the tungsten carbide crusher liner has increasingly become a pivotal element for businesses aiming to enhance operational efficiency and cost-effectiveness. This innovation not only promises unparalleled durability but also elevates the entire material processing methodology.
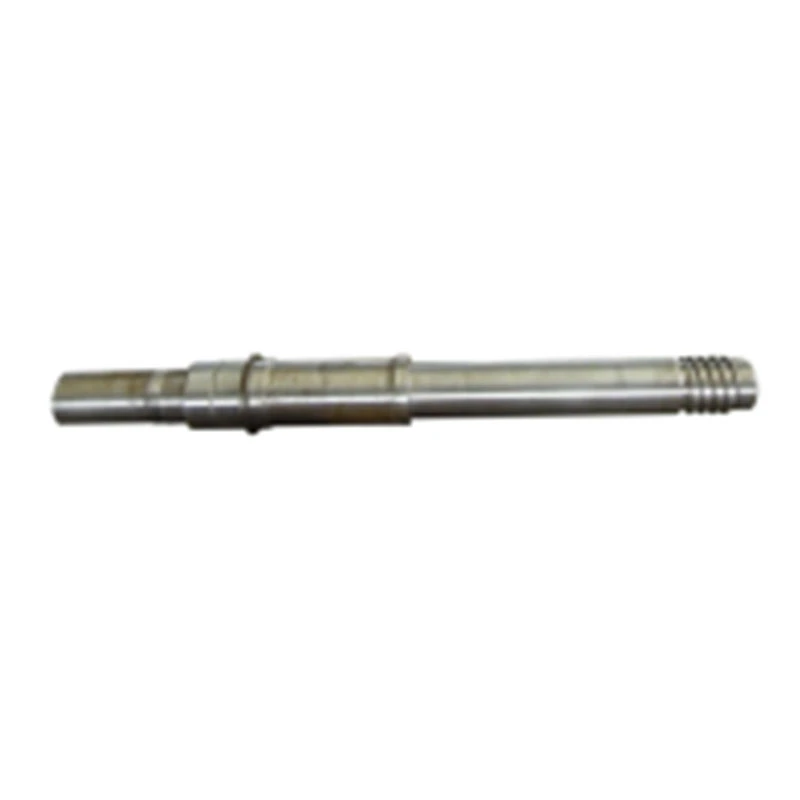
Historically, the dilemma faced by many industries, from mining to material recycling, has been the rapid wear and tear of crusher components. This challenge, often leading to frequent downtime for replacement and maintenance, considerably hampers productivity. Enter the tungsten carbide crusher liner—a revolutionary product that expertly addresses this widespread problem.
Tungsten, renowned for its hardness and refractory properties, offers exceptional resistance to wear.
When employed as a lining material for crushers, tungsten carbide compounds significantly extend the equipment's lifespan. This remarkable durability translates to prolonged service intervals and reduced maintenance costs. The economic benefit is substantial, as less frequent shut-downs mean enhanced throughput and a greater return on investment.
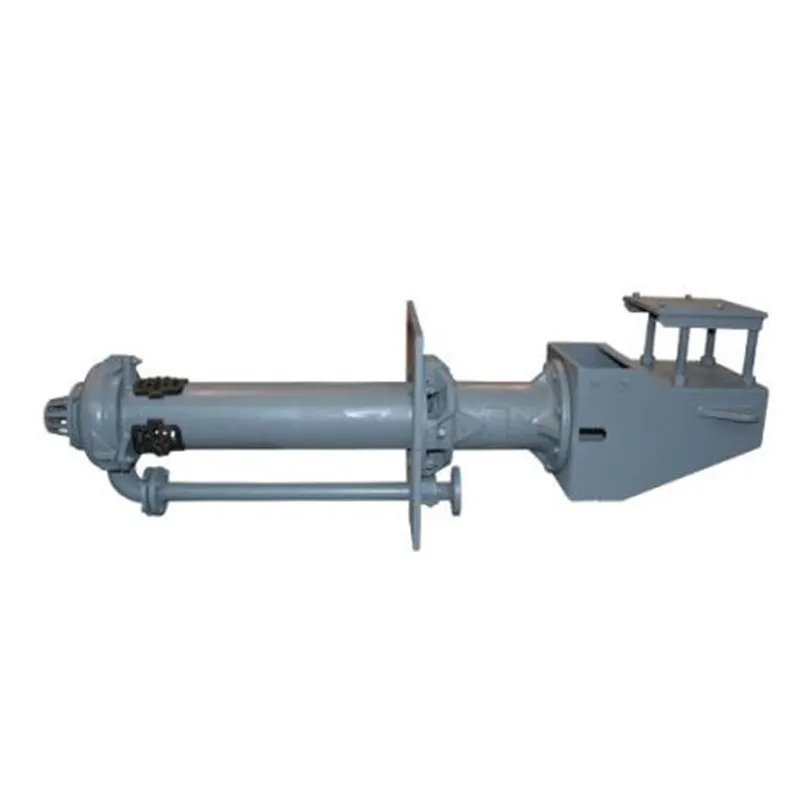
From an expertise standpoint, industries utilizing these advanced liners report a marked improvement in crushing efficiency. The tungsten liner's ability to maintain shape and integrity under extreme conditions allows consistent material processing, leading to uniform particle size and improved product quality. This level of consistency is particularly crucial in sectors like mining, where at every stage, uniformity in material size can greatly influence subsequent processing stages and overall efficiency.
revestimiento de triturador de tungsteno
When considering trustworthiness, feedback from industry leaders who have integrated tungsten carbide crusher liners into their operations is overwhelmingly positive. Many emphasize the product's reliability, noting that its resilience translates not only into cost savings but also into energy savings. As the liners exhibit less wear, crushers require less energy to operate effectively, aligning companies with environmentally sustainable practices—an increasingly critical factor in today's industrial landscape.
Moreover, the authoritative endorsement of tungsten carbide as a premium solution in equipment manufacturing cannot be overstated. Renowned material scientists and engineers vouch for its superior properties, reaffirming its suitability for heavy-duty applications. Such endorsements lend validation to its application, instilling confidence in prospective adopters.
From a trustworthiness perspective, choosing a supplier with a proven track record in tungsten processing further guarantees the quality and performance of the crusher liners. Reputable suppliers implement rigorous quality control measures, ensuring each liner meets industry standards and exceeds performance expectations.
In conclusion, the tungsten carbide crusher liner represents a pivotal advancement in crusher component technology, deftly balancing durability, efficiency, and cost-effectiveness. For businesses serious about optimizing their material processing systems, transitioning to tungsten carbide liners provides not just operational excellence, but a sustainable edge in an increasingly competitive market. The transformation brought about by this seemingly small component underscores an important business principle innovation often lies in the details, and mastering these can drive monumental success.