When exploring the world of jaw crusher spare parts, understanding the intricate details and specific characteristics of these components is crucial for maintaining peak performance. Jaw crushers, vital tools in industries such as mining and construction, rely on an array of components working in harmony to crush materials effectively. Here,
we delve into the essential aspects of these critical machine parts.
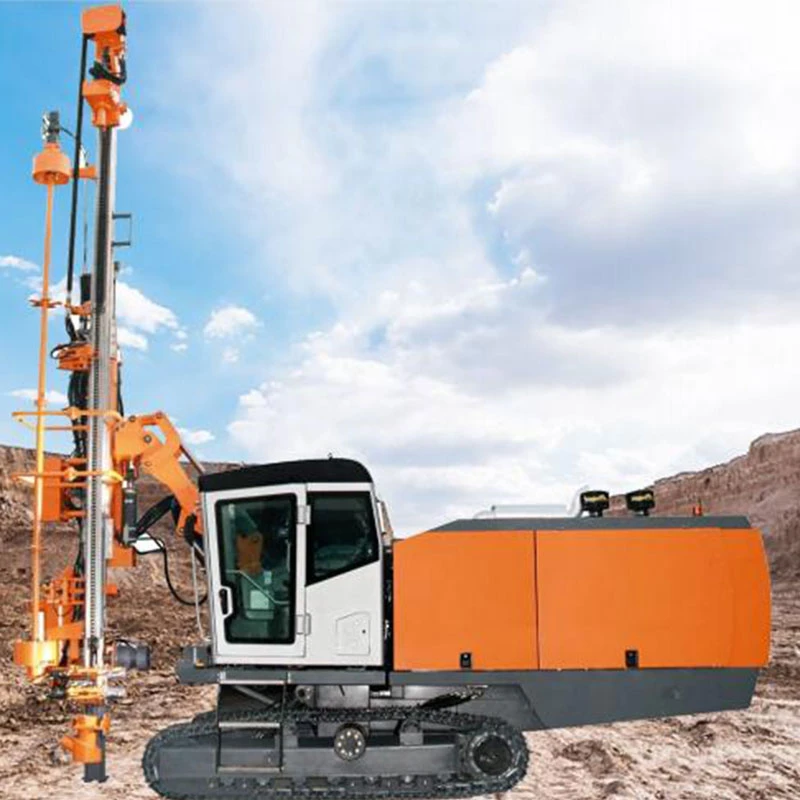
Jaw crushers serve as pivotal equipment for reducing large materials into more manageable pieces. These machines require robust construction, and their optimal function hinges on the proper maintenance and replacement of spare parts. The core components of a jaw crusher include the jaws, pitman, and frame, each playing an indispensable role in the device's operation.
The primary component, the jaws, made typically from manganese steel, are responsible for compressing the feed material introduced into the crusher. Each jaw, one fixed while the other is movable, functions in unison under the influence of the pitman, a moving component powered by the machine's motor. The pitman is connected to the flywheel and eccentric shaft, which converts rotational motion into a reciprocating movement, essential for the closing action between the jaws essential for crushing.
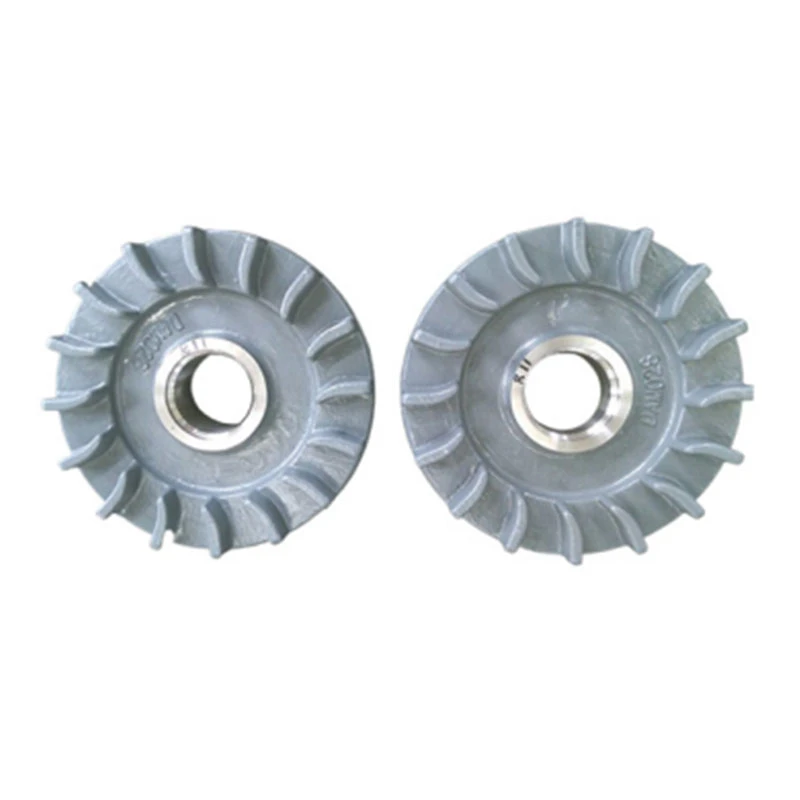
In maintaining these crushers, attention must be paid to several key spare parts, ensuring the machine remains reliable and efficient. The jaw plates, often the first component to wear, require regular inspection and replacement. Choosing high-quality jaw plates made from durable materials can significantly enhance the lifespan of the crusher. Opting for OEM (Original Equipment Manufacturer) parts versus aftermarket options is often advised, as OEM parts are specifically designed for compatibility and longevity within the crusher.
Examining the toggle plate, another critical component, unveils its role as a safety mechanism for the crusher. This simple part not only supports the movable jaw but also acts as a protective device. In the event of uncrushable material entering the crushing chamber, the toggle plate can break, preventing damage to more expensive components. Regular inspection is necessary to ensure its integrity, and timely replacement is crucial in safeguarding the crusher’s more complex systems.
piezas de triturador de mandril
Lubrication systems within the crusher demand equal attention to maintain smooth functioning of the jaw crusher’s moving parts. Proper lubrication minimizes friction and wear, thus extending the life of bearings and other moving parts. Implementing an appropriate lubrication schedule can drastically reduce downtime and extend operational timeframes.
Another overlooked component is the eccentric shaft. The rigorous demands placed on this component necessitate regular inspection and maintenance. A damaged shaft can lead to operational inefficiency, increased energy consumption, and potential damage to the entire system. Ensuring the shaft is free from cracks and damage will maintain the crusher’s efficacy and reduce financial loss due to downtime.
Regular training of maintenance personnel is another key aspect of ensuring the longevity of jaw crusher components. Skilled operatives will recognize the early warning signs of wear and tear, thus implementing problem-solving measures before major issues arise, ensuring continuous operational readiness.
Utilizing technology can further enhance the maintenance process. Predictive maintenance tools, employing sensors and diagnostic equipment, provide real-time feedback on the condition of jaw crusher parts. These innovations enable precise identification of potential failures, allowing for preemptive correction before catastrophic malfunctions occur.
In conclusion, understanding the roles and maintenance requirements of jaw crusher components is pivotal for the effective operation of these machines. Emphasizing the selection of durable parts, implementing a rigorous inspection and replacement schedule, and employing technologically advanced monitoring tools enhances both performance and longevity. Informed personnel, equipped with comprehensive knowledge and specialized training, significantly contribute to the successful operation and preservation of these industrial workhorses, ensuring they continue to serve their purpose efficiently across various sectors.