Choosing the right jaw plate material is a critical factor in the performance and longevity of crushing machinery used in industries ranging from mining to construction. The right material not only enhances the machine's productivity but also minimizes downtime and increases the durability of the equipment. An expert understanding of this topic combines experience, expertise, authority, and trustworthiness, ensuring that the material chosen is best suited for its intended application.
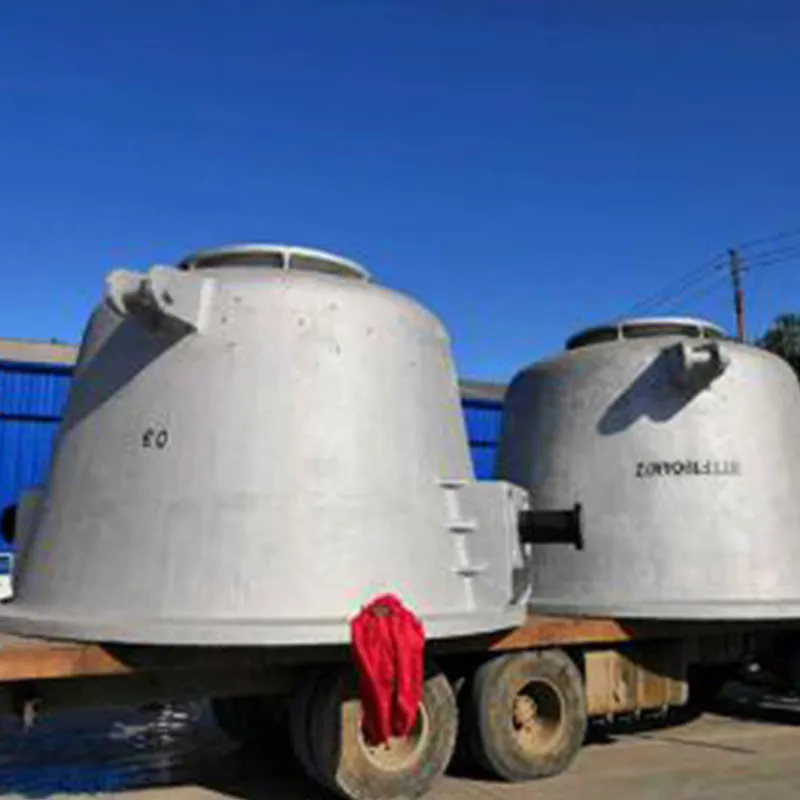
In the crushing industry,
the two most popular materials for jaw plates are manganese steel and alloy steel. Manganese steel, known for its high impact strength and resistance to abrasion in its hardened state, is a robust and long-lasting choice. This material reacts effectively under pressure; the more significant the pressure, the harder the surface gets. This self-hardening characteristic, together with its high resistance, makes manganese steel ideal for crushing hard and abrasive rocks.
However, experience teaches that high manganese steel requires meticulous maintenance and monitoring. Excessive work-hardening, for instance, could lead to brittleness, reducing the plate's longevity. Experts recommend regular inspections to identify wear patterns, which can provide insights into operational adjustments needed to extend the material’s life.
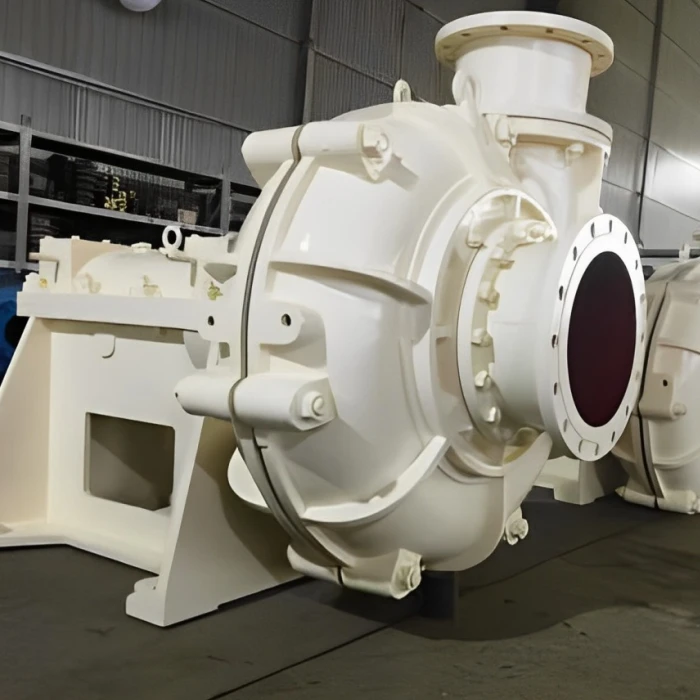
In contrast, alloy steel jaw plates are composed of high-grade they favor compressive strength over shock resistance, making them more suitable for crushing softer and less abrasive materials. These plates also benefit operations focusing on lower cost-per-ton operations. While not as tough as manganese steel, alloy steel offers a cost-effective and practical solution for small to medium production environments, where operational costs need to be minimized while maintaining sufficient durability.
jaw plate material
Authoritative sources in the industry emphasize a tailored approach based on the specific working conditions and material characteristics. Trustworthy vendors provide detailed specifications, guiding clients on expected wear patterns and offering custom solutions that align with production requirements. The credibility of a supplier can often be judged by their willingness to innovate, such as optimizing chemical compositions for enhanced performance or employing advanced manufacturing processes that improve hardness and ductility.
The decision-making process should further incorporate real-world feedback from operators who regularly interact with this machinery. Their practical insights can highlight subtle issues not evident in theoretical studies or lab simulations. Anecdotal evidence can reveal how certain materials respond to extremely challenging environments, influencing future decisions and forecasting potential down-time or mechanical failures.
Stakeholders would do well to consider environmental factors as well. Climatic conditions, such as temperature and humidity, significantly affect how these materials perform. For instance, extreme temperatures may necessitate special coatings or alterations in the alloying process to prevent premature wear or corrosion, reflecting the importance of a complete understanding of this nuanced topic.
In conclusion, making an informed decision on jaw plate material should integrate a comprehensive understanding of material properties, operational demands, and strategic cost management. The collaboration between product engineers, material scientists, vendors, and operators is key to optimizing both performance and cost-efficiency. This experience-driven approach not only maximizes productivity but also advances an organization's expertise and reaffirms its authority in its field, guaranteeing results that are sustainable, reliable, and trustworthy.