Properly adjusting a jaw crusher is crucial for optimizing its efficiency, longevity, and performance. Jaw crushers are integral machines in various industries like mining, construction, and demolition. As a seasoned professional specializing in heavy machinery maintenance, I've gathered insights and effective techniques to ensure precise jaw crusher adjustments that enhance productivity and safety.
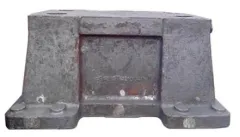
A jaw crusher works by using compressive forces to break down large, hard materials into smaller, more manageable pieces. It features two jaws—one stationary and one movable—that form a V-shaped chamber. The size of the output material is determined by the gap setting at the bottom of this chamber, known as the discharge opening. Proper adjustment of this gap is pivotal in achieving desired material sizes and preventing equipment wear and tear.
To effectively adjust a jaw crusher, start by inspecting the crusher's manufacturer guidelines. Ensuring compliance with these instructions maintains equipment integrity and operational safety. Regular maintenance checks on the crusher should include monitoring wear parts such as jaw plates, toggle plates, and contact points. Excessive wear requires immediate attention, as it can affect the jaw crusher's ability to operate efficiently.
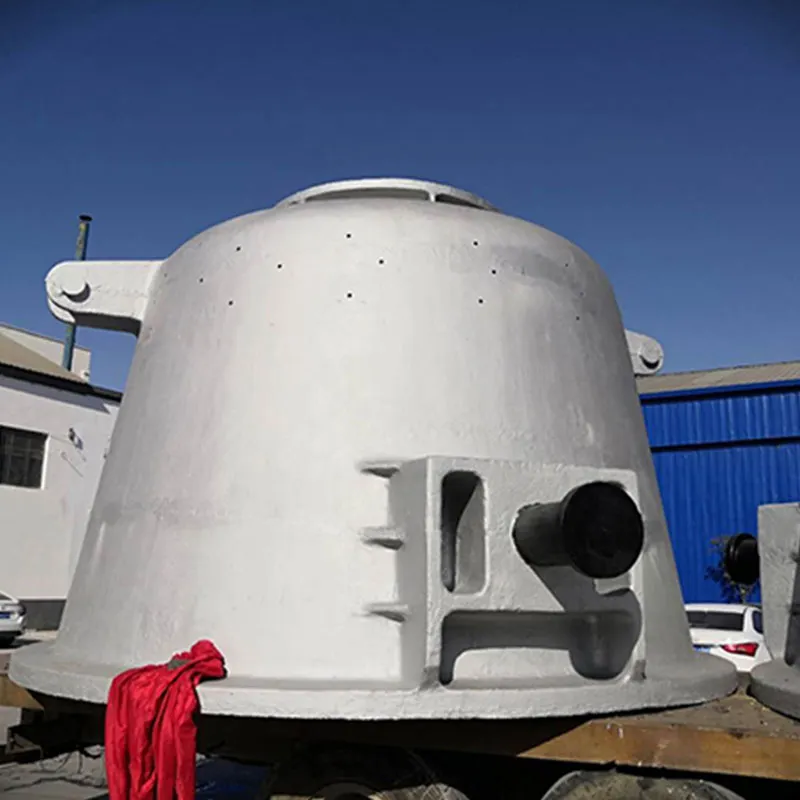
Next, conduct a thorough inspection of the jaw crusher's hydraulic system if applicable. Modern jaw crushers often use hydraulic adjustment mechanisms to alter the discharge opening without the need for manual alignment. Ensuring that hydraulic systems are leak-free and functioning optimally prevents equipment malfunctions during operation. Regularly checking and adjusting the hydraulic pressure according to manufacturer specifications ensures the jaw crusher operates within its necessary parameters.
jaw crusher adjustment
When setting the jaw crusher's discharge opening, determine the required size of the output material. For consistency, use a graduated scale or similar measuring tool. Carefully adjust the gap by manipulating the crusher's tension rods or hydraulic cylinders, observing all necessary safety protocols. It is essential to maintain uniformity in the gap setting along the width of the chamber to avoid uneven wear on the jaws.
Besides mechanical adjustments, pay attention to the crusher's feed size and material composition. Overloading or introducing oversized materials can lead to blockages that hinder performance and increase downtime.
Gradation control ensures stable crusher output and prolongs the lifespan of its components. Employing screens to sort material before it enters the crusher can minimize the risk of clogs and maintain consistent throughput.
Finally, collaborate closely with experienced technicians, and implement advanced monitoring systems if available. Technologies such as wear sensors, automated controls, and machine diagnostics can offer real-time insights into the jaw crusher's performance and wear conditions. These systems reduce the need for extended diagnostics and adjustments, ensuring seamless operations and reducing unnecessary manual checks.
In conclusion, maintaining peak efficiency in jaw crushers revolves around sustained, precise adjustments, proactive maintenance, and integrating technology where feasible. Leveraging the expertise of manufacturers and skilled personnel, along with employing systematic procedures, guarantees the jaw crusher remains a robust, reliable workhorse within any material processing operation. By fostering these practices, operations not only optimize production but also uphold safety and extend machinery lifespan, solidifying their position as leaders in heavy-duty industrial processes.