Drill rods are an essential component in the world of drilling, playing a pivotal role in a myriad of industries—from mining to construction. My journey with drill rods began over a decade ago, offering me a wealth of expertise in their application and technological advancements. In an age where precision and efficiency are paramount, understanding the nuanced application of drill rods can significantly enhance operational success.
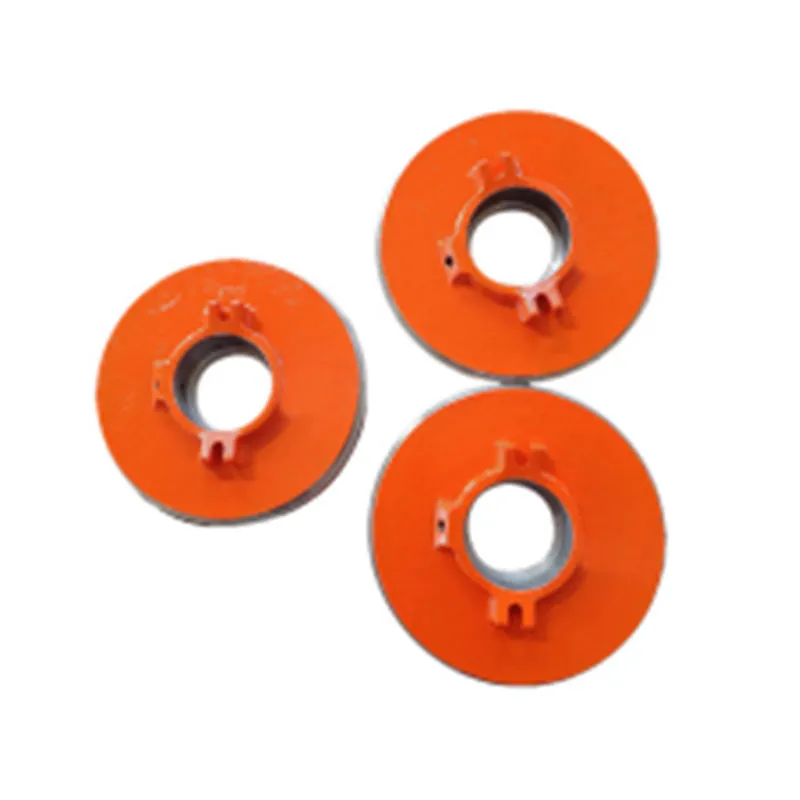
The significance of drill rods lies in their ability to create a conduit between the surface and the depths of the earth. They serve as the backbone of any drilling operation, whether you're penetrating through hard rock formations or softer substrata. When considering drill rods for your project, the key factors to evaluate include material composition, tensile strength, and the connection type.
The expertise surrounding drill rods stems from an understanding of metallurgy. Most high-quality drill rods are manufactured from premium alloys, often a combination of carbon and steel, to ensure durability and longevity. These materials are subjected to rigorous heat treatments to enhance their tensile strength, making them capable of withstanding immense pressure and torque. For instance, in my experience working on high-pressure drilling projects, selecting rods with the right balance of sturdiness and flexibility was crucial. Drill rods need to absorb significant stress while maintaining their structural integrity, a balance achieved through precise engineering.
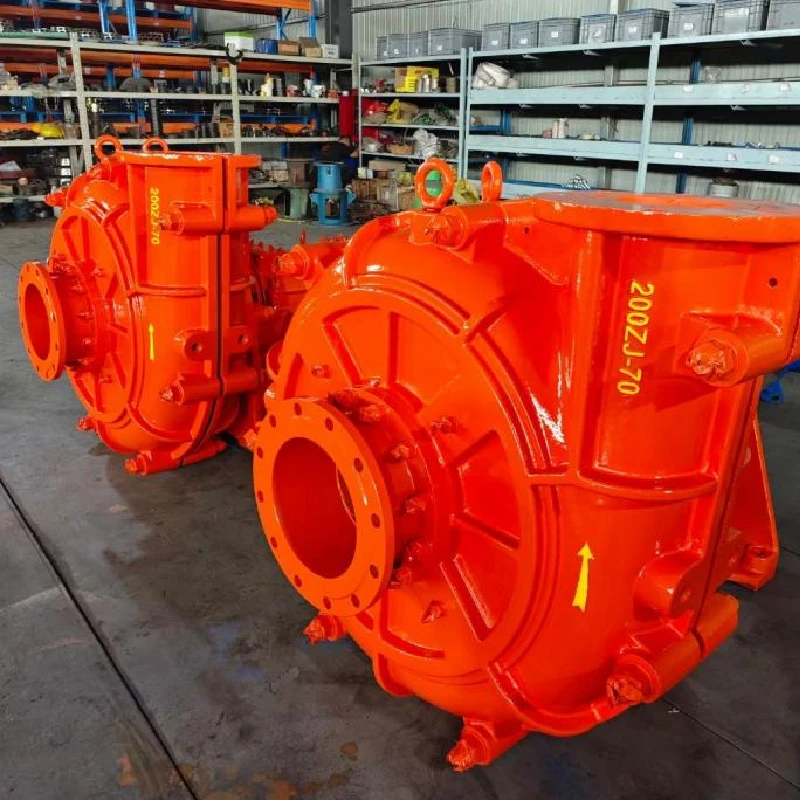
Expertise in drill rods also involves familiarity with their multiple types and uses. For instance, there are standard drill rods, heavy-duty rods, and wireline rods, each tailored for specific drilling needs.
Heavy-duty rods are particularly advantageous for projects requiring deep drilling as they offer superior strength. Meanwhile, wireline rods are vital in mineral exploration, allowing for the retrieval of core samples without having to lift the entire drill string.
Furthermore, trustworthiness and reliability in drill rods are underscored by choosing products from reputable manufacturers who adhere to international standards. In my career, I have witnessed the consequences of opting for inferior drill rods—from project delays to equipment failures. Ensuring the drill rods are certified through rigorous testing protocols validates their performance and reliability.
drill rods
When considering the ecological impacts of drilling, choosing high-quality drill rods that require less frequent replacement can reduce environmental footprints and operational costs. It's a testament to the authority that comes with selecting premium products that meet both industry and environmental standards.
Equally important is the connection type of drill rods, which is a critical element often overlooked. Threaded connections must be precise to ensure a tight fit, reducing the likelihood of operational failures and ensuring safety. Over the years, I've learned to emphasize the importance of matching thread profiles to equipment specifications, an expertise that only develops with practical experience and continual learning.
Finally, an authoritative understanding of drill rods involves continual adaptation to technological advancements. Innovations such as friction-welding technology for joint connections and the introduction of composite materials are now informing next-generation drill rods. Staying abreast of these developments ensures that operations remain competitive and efficient.
In summary, drill rods are more than mere components; they are integral to the success and safety of drilling operations. Drawing from extensive experience and industry expertise allows for informed decision-making when selecting drill rods, driving efficiency and minimizing risks. To maintain the highest standards of trustworthiness and authority, one must prioritize quality, adaptability, and adherence to global standards, thereby setting a foundation for sustainable and successful drilling ventures.