Understanding carbide drill rods requires delving into their application, benefits, and selection criteria, aspects critical to both woodworking and metalworking industries. The intrinsic properties and engineering precision offered by carbide technologies stand second to none in high-demand environments.
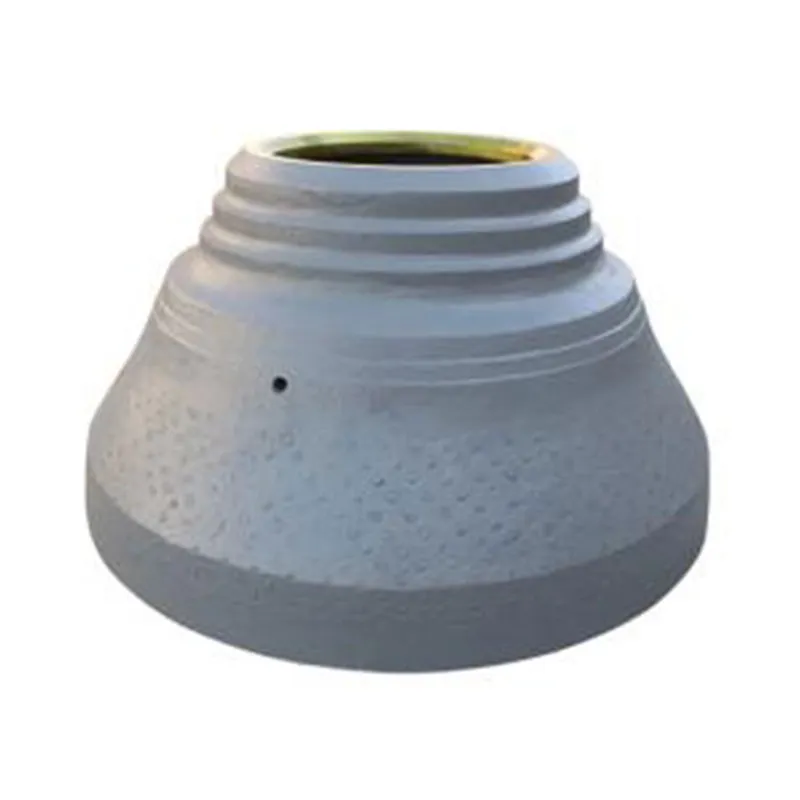
When considering the utilization of carbide drill rods, the first point of contemplation should be the material's composition. Tungsten carbide, known for its exceptional hardness, durability, and resistance to abrasion, forms the bedrock of these tools. Crafted through a powder-metallurgy process, this composite remains a favorite amongst professionals who prioritize quality and precision.
The primary benefit of choosing carbide drill rods lies in their longevity and performance sustainability. In comparison to traditional steel rods, carbide rods exhibit vastly superior wear resistance, resulting in significant reductions in downtime for tool replacements. This translates directly into increased efficiency and productivity in industrial settings. The durability of tungsten carbide is especially advantageous in drilling operations where precision and consistency are paramount.
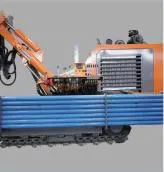
Comparative assessments reveal that carbide drill rods are particularly advantageous in high-speed applications due to their ability to retain sharpness longer than other materials. Their impressive heat resistance minimizes tool deformation even at elevated temperatures, ensuring precise drilling without compromising structural integrity. This capability makes them indispensable tools in sectors such as aerospace, automotive engineering, and heavy equipment manufacturing, where precise specifications are non-negotiable.
Incorporating carbides into the daily workflow demands a thorough understanding of their limitations as well. Despite their strengths, carbide drill rods are intrinsically more brittle compared to other materials. This brittleness makes them prone to chipping if handled incorrectly. Consequently, experts advocate for careful storage and handling practices to maximize their lifespan and effectiveness.
Choosing the right carbide drill rod involves an informed analysis of application needs. Parameters such as the workpiece material, drilling speed, and operational scale play crucial roles in determining the best-suited rod type. Several proprietary formulations and coatings are available in the market, each engineered for specific requirements, such as enhanced cutting efficiency or increased corrosion resistance.
carbide drill rod
Technical proficiency is further enhanced by familiarity with the latest innovations in carbide technology. Advances such as nanostructured carbides and micro-grain compositions provide customized benefits tailored to niche demands. These technologies push the boundaries of what traditional materials can achieve, offering companies the chance to refine performance metrics further than ever before.
In building a network of trust with clientele, transparency about manufacturing processes and material sourcing can enhance trustworthiness. Companies investing in ethically sourced raw materials and environmentally responsible production techniques not only contribute positively to sustainability efforts but also engender loyalty among environmentally conscious customers.
Industrially speaking, the deployment of carbide drill rods goes beyond mere utilization; it calls for synergetic expertise between tool manufacturers and end-users. Maintaining an open dialogue on best practices, usage techniques, and industry trends enriches all parties involved, promoting a culture of continuous improvement and shared knowledge.
The rapid evolution of carbide technologies, driven by research and development, continually shapes the landscape. Stakeholders committed to staying ahead must engage with scholarly resources, attend conferences, and participate in collaborative projects that encourage the exchange of innovative ideas.
In conclusion, carbide drill rods represent a pinnacle of engineering prowess, meeting the rigorous demands of modern-day industrial drilling applications with unmatched reliability and performance. Success in leveraging their potential hinges on the harmonious integration of material knowledge, application expertise, and operational foresight, all underpinned by a commitment to quality and innovation. This multifaceted approach not only enshrines these tools as indispensable assets but also strengthens an organization’s competitive edge in a burgeoning global market.