Mud pumps, a crucial component in various industries such as oil drilling and construction, have intrigued engineers and technicians for years. Understanding how a mud pump operates is essential for ensuring efficiency and preventing costly downtimes in critical projects.
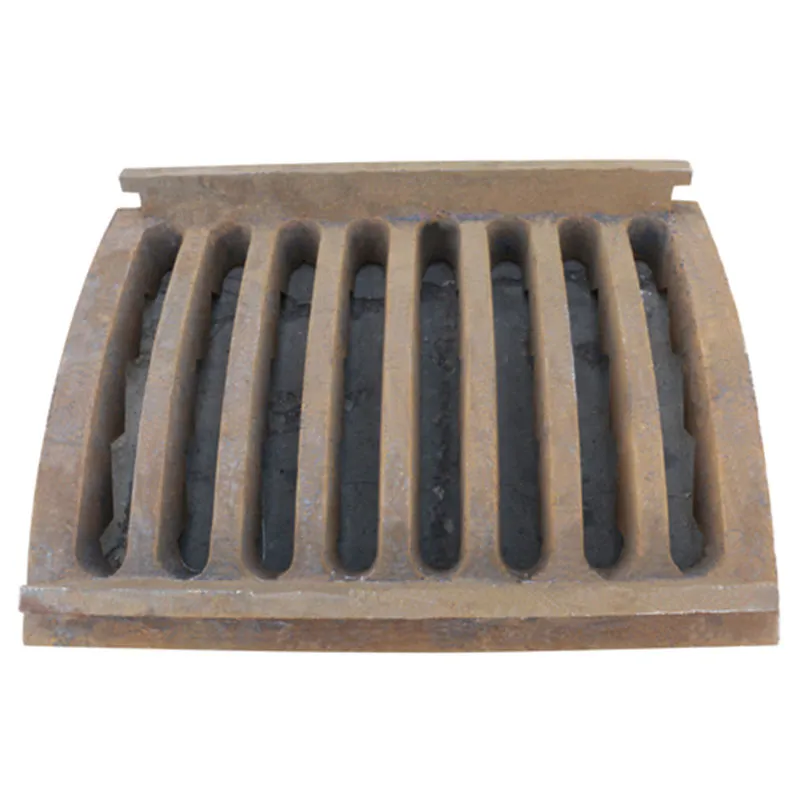
A mud pump's primary function is to circulate the drilling fluid, commonly called mud, down the drill string and back up the annulus. This circulation cools the drill bit, transports drill cuttings to the surface, and stabilizes the wellbore. The pump's operation is centered on its pistons or plungers that move fluid through a suction and discharge cycle.
The intricate design of a mud pump combines experience-tested engineering practices and cutting-edge technology. Typically, two main types of mud pumps are utilized duplex and triplex. Duplex pumps have two pistons, while triplex pumps employ three, offering smoother flow and reduced pulsation due to their sequential operation. This reduction in pulsation ensures consistent mud flow, crucial for maintaining well stability and optimizing drilling performance.
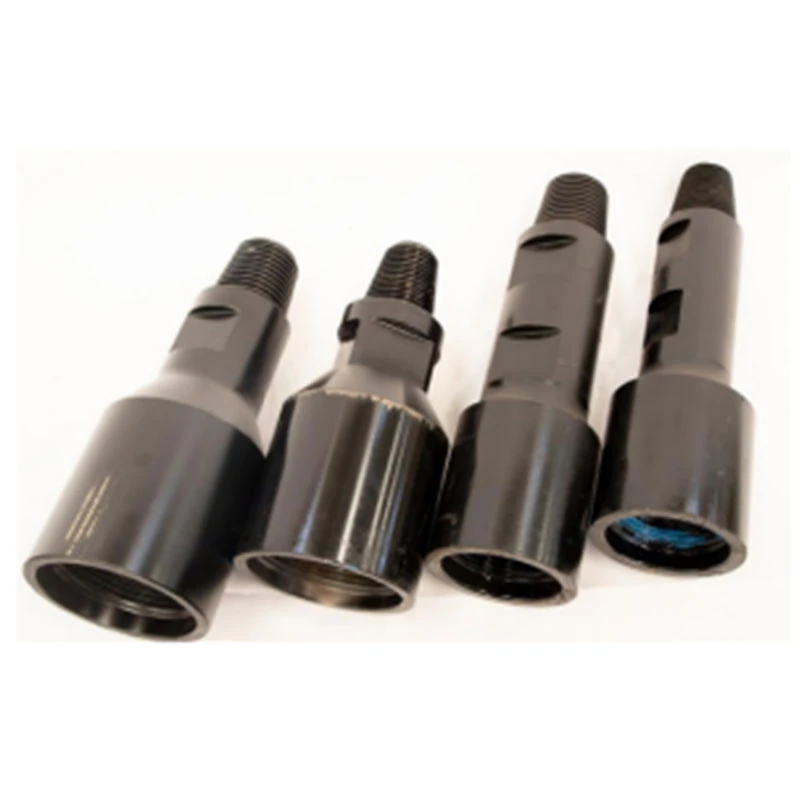
Material selection is paramount in mud pump construction. Components such as liners and pistons are crafted from high-grade, wear-resistant materials to withstand the abrasive nature of drilling fluids. This durability is backed by decades of research and practical findings by industry experts aiming to extend the lifespan of the pump, thereby boosting its reliability.
Another critical aspect of mud pump operation is the power source. These pumps generally rely on diesel engines or electric motors, chosen based on the operational environment and energy requirements. This adaptability signifies the pump’s versatility, whether deployed on a compact rig in remote locations or large offshore platforms.
How the sludge pump works
Expertise in mud pump maintenance plays a pivotal role in operational efficacy. Routine inspections to detect signs of wear, such as pitting on the plungers or erosion in the valves, are essential. These practices are rooted in industry standards, derived from exhaustive field tests and analysis that ensure repair and maintenance are both timely and cost-effective.
Furthermore, technological advancements have ushered in the era of smart mud pumps, integrated with sensors that provide real-time data on pump performance. This information is invaluable, enabling technicians to make informed decisions, thus preventing potential failures and extending the pump's life.
Trustworthiness in mud pump systems comes from rigorous testing and certifications by authoritative organizations. Manufacturers adhere to API standards, ensuring that every pump meets stringent safety and performance benchmarks. Such compliance not only enhances trust but also guarantees that the pumps are safe to use in high-pressure, high-stakes environments.
In conclusion, the functionality of mud pumps is an intricate play of design, materials, and technology governed by principles refined through years of experience. Understanding these elements not only aids in selecting the right equipment but also in implementing maintenance practices that can save time and resources, ultimately increasing the efficiency of drilling operations.