In the realm of manufacturing and heavy industries, solid carbide drill bits, or barras de perforación de metal duro, hold a pivotal role due to their exceptional strength, durability, and efficiency in cutting through tough materials. Understanding their application, composition, and benefits can significantly enhance productivity and ensure optimal utilization in various industrial processes.
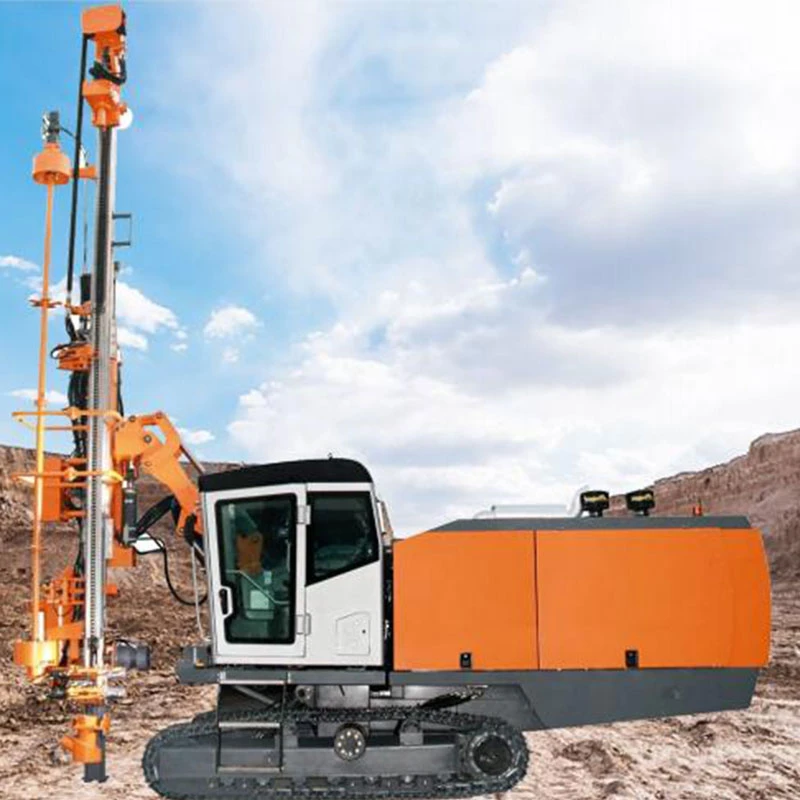
Solid carbide is an advanced material predicated on the fusion of carbon and tungsten, resulting in a substance that boasts remarkable hardness and heat resistance. This robustness makes carbide drills indispensable in settings where high precision and extended tool life are demanded. Unlike traditional steel or HSS (high-speed steel) drills, carbide's unique properties allow it to maintain a sharp cutting edge for an extended period, significantly reducing the frequency of tool replacements.
Utilizing solid carbide drill bits ensures an unparalleled drilling experience, especially when working with hard metals and abrasive materials. Industries like automotive, aerospace, and energy rely heavily on these tools for efficient production. In automotive manufacturing, for instance, the precision and endurance of solid carbide drills facilitate the production of engine blocks with intricate cooling channels and complex fuel injection components.
This precision is critical for ensuring engine performance and longevity.
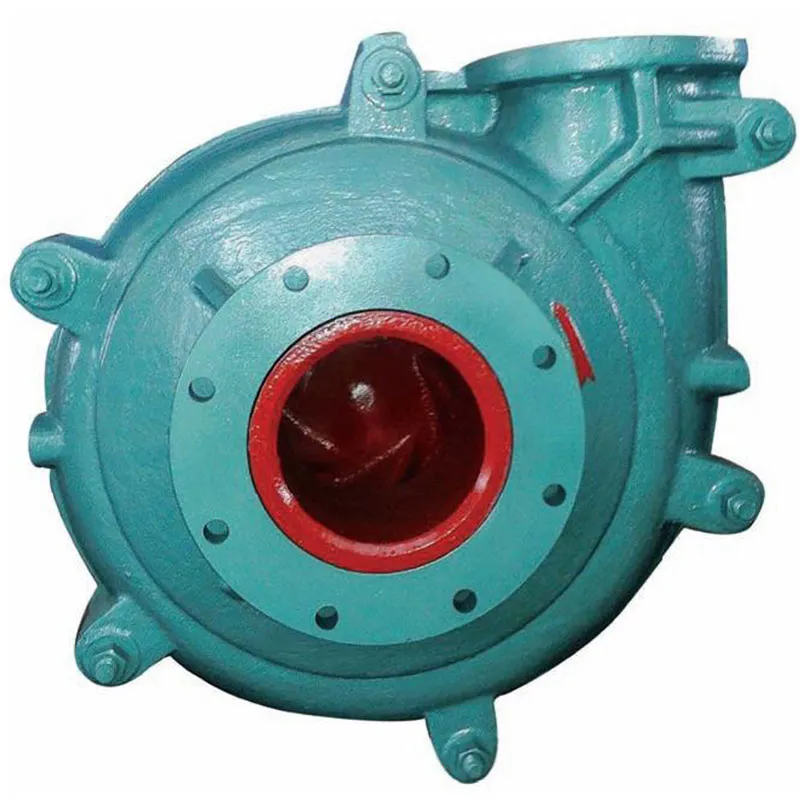
Similarly, in the aerospace sector, these drills are crucial for creating precise components such as frames and panels, which must withstand extreme stress and temperatures. The remarkable wear resistance and thermal stability of carbide drills allow them to perform under these challenging conditions without compromising the structural integrity of the components.
The engineering behind solid carbide drill bits involves meticulous design and manufacturing processes. Advanced computer-aided design (CAD) software ensures that each drill is optimized for performance, taking into consideration the specific requirements of the material it will cut. The fusion of technology and material science creates drills capable of operating at high speeds, which enhances their efficiency. Furthermore, the ability of these drills to operate at elevated temperatures without losing strength is a critical factor in their widespread industrial adoption.
Choosing the right drill involves understanding the substrates it will interact with and the specific requirements of the project. For instance, machinists must consider the type of coating applied to carbide drills, such as TiN (titanium nitride) or TiAlN (titanium aluminum nitride), which further enhances their performance by providing additional lubrication and reducing heat build-up during operations.
hard metal drilling rods
The durability of solid carbide drills extends beyond their physical attributes to impacting overall operational cost-effectiveness. Though initially more expensive than their steel counterparts, their extended lifespan and reduced downtime ultimately offset the initial investment, providing substantial savings in the long run. Fewer tool changes and less frequent servicing translate into more consistent production cycles and increased output.
Safety is another paramount aspect where carbide drills excel. Their reliable performance reduces the risk of tool failure, thereby minimizing potential accidents in the workplace. Consistent quality and predictable wear patterns ensure that operators can maintain a steady hand and focus on precision, reducing the likelihood of costly errors.
Trust in solid carbide drill bits has been established through continuous research and development. Manufacturers of these tools often work closely with industry partners to innovate and improve, ensuring that the drills meet the ever-evolving demands of modern industry. This collaboration underscores the credibility and authoritative standing of solid carbide drills in the industrial community.
Maintenance plays a vital role in extending the life of carbide drills. Regular inspections for signs of wear, coupled with proper storage and handling, can significantly enhance tool longevity. Training operators to recognize signs of deterioration and encouraging a culture of proactive maintenance ensures that the tools remain in peak condition, maximally contributing to operational efficiency.
In conclusion, the advantages of employing solid carbide drill bits are undeniable, offering superior performance, durability, and cost-effectiveness in demanding industrial applications. Their strategic use not only enhances production quality but also establishes a foundation of trust in the tools engineering professionals rely upon daily. Emphasizing expertise, reliability, and innovation, solid carbide drills will continue to be indispensable assets in the machineries of modern industry.