Vertical centrifugal pumps, a staple in industrial fluid management, have gained significant traction due to their numerous advantages over traditional pump designs. These pumps, primarily used for clean and slightly contaminated liquids, stand out due to their space-saving orientation and highly efficient functionality.
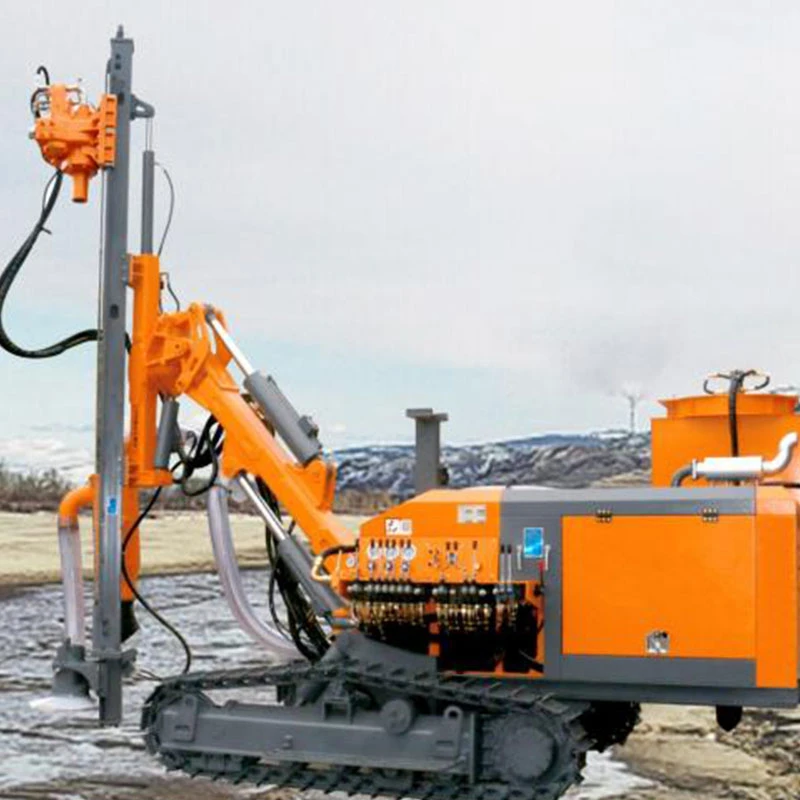
Vertical centrifugal pumps operate on the principle of converting rotational kinetic energy, usually from an electric motor, into hydrodynamic energy of fluid flow. This conversion process allows these pumps to handle large volumes at relatively high pressures, making them suitable for various industrial applications such as chemical processing, water treatment, and power generation.
The design of vertical centrifugal pumps offers several advantages. First, their vertical structure minimizes floor space requirements, which is particularly beneficial in plants where space is at a premium. The vertical configuration also promotes a streamlined flow path for fluids, reducing friction losses and enhancing overall pump efficiency. This is an essential consideration for operations looking to optimize energy use without compromising on performance.
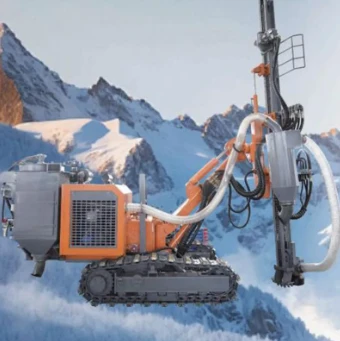
From an engineering perspective, vertical centrifugal pumps are designed to reduce cavitation and enhance stability during operation. Cavitation, the formation and collapse of vapor bubbles within a liquid, can severely damage pump components. The vertical design allows improved suction capabilities, ensuring that liquids are adequately fed into the pump, thus minimizing the risk of cavitation. The alignment of components in a vertical pump also contributes to reduced vibration, higher reliability, and less maintenance over the pump’s lifecycle.
Vertical centrifugal pump type
Industrially, these pumps are favored for their versatility. They can handle a variety of fluids, ranging from water and oils to chemicals and slurries, adaptable to the specific needs of industries such as petrochemical, mining, and wastewater management. This adaptability underscores the expertise embedded in their design, enabling them to meet rigorous industry standards and certifications.
Authoritativeness in the market is achieved by consistently delivering reliable performance across various applications. Leading manufacturers of vertical centrifugal pumps employ advanced materials and innovative technologies to enhance durability and efficiency. For instance, corrosion-resistant alloys and special coatings are used to combat the wear and tear associated with harsh operating environments. These advancements, backed by decades of engineering research and development, establish vertical centrifugal pumps as authoritative solutions in fluid dynamics.
Trustworthiness is ensured through comprehensive testing and quality control measures. Manufacturers conduct extensive performance assessments to certify that each pump meets the required operational criteria. This commitment to quality assures users of consistent pump performance, minimal downtime, and lower total cost of ownership. Furthermore, many manufacturers provide robust after-sales support and maintenance services, ensuring that the pumps operate optimally throughout their intended lifespan.
In summary, vertical centrifugal pumps offer a blend of advanced engineering, space efficiency, and robust performance, making them indispensable in modern industry. Their design addresses common challenges like cavitation and vibration, ensuring stable and efficient operation across diverse applications. Backed by rigorous testing and trusted by industry leaders, these pumps are a testament to both engineering expertise and reliability. As industries evolve, the ongoing development of vertical centrifugal pumps ensures they remain at the forefront of fluid management solutions.