Efficient slurry transport is critical in industries such as mining, dredging, and wastewater management. Centrifugal pumps are often preferred for this task due to their ability to handle highly viscous and abrasive mixtures. Drawing on years of industry expertise and technical authority, this article delves into effective strategies for optimizing slurry transport using centrifugal pumps.
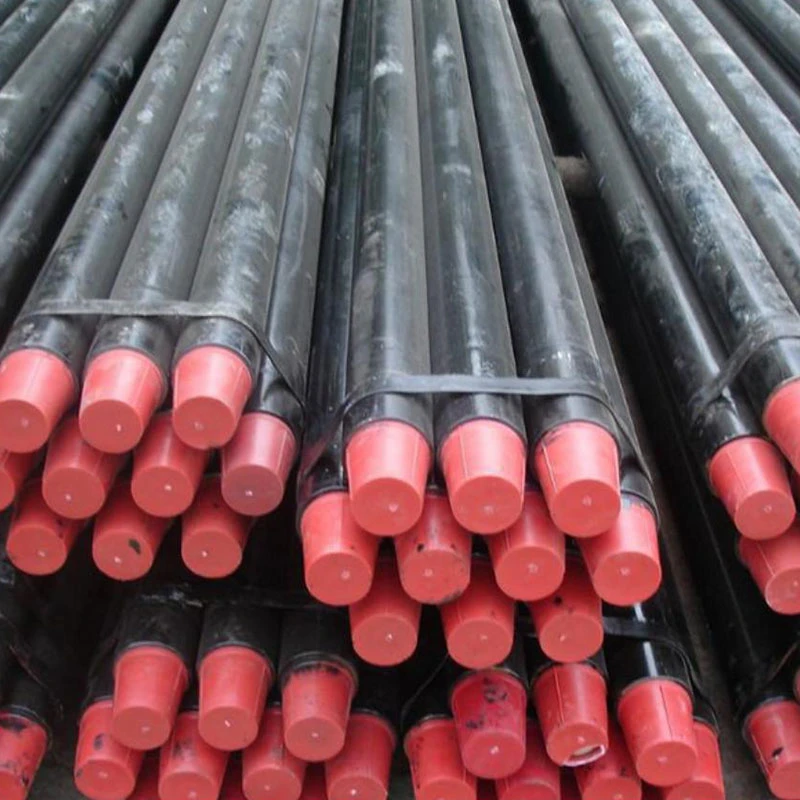
Understanding slurry dynamics is crucial for achieving optimal performance. Slurries, consisting of solid particles suspended in liquid, present unique challenges, such as wear on pump components and flow resistance. It's important to select the right type of centrifugal pump; typically, pumps with large impellers and robust materials are recommended for slurry applications. For effective slurry transport, the material of the pump components should be able to withstand abrasion and corrosion—common issues when dealing with slurries with varying pH levels and abrasive particles.
Performance efficiency is another critical factor. Experienced professionals know that slurry concentration and particle size distribution significantly affect pump efficiency. To minimize energy consumption while maximizing throughput, it's crucial to operate within the pump's best efficiency point (BEP). Regular monitoring and adjustments ensure the pump operates close to its BEP even as slurry characteristics change.
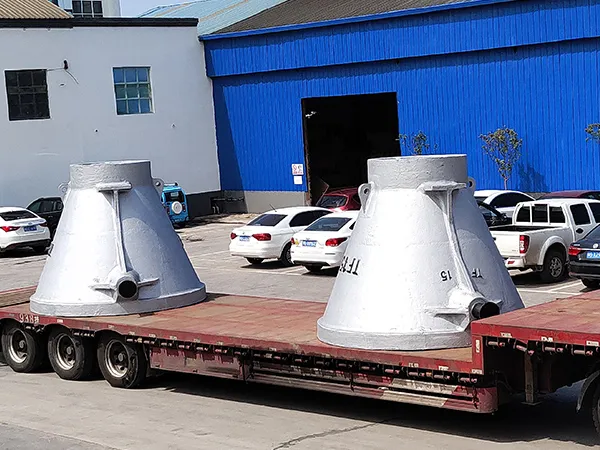
To enhance reliability and prolong the operational life of centrifugal pumps, implementing Best Practice Maintenance is non-negotiable. This includes regular inspection schedules focusing on critical wear parts such as impellers, liners, and shaft seals. Experts recommend predictive maintenance techniques, such as vibration analysis and thermographic scanning, to preemptively identify potential failures.
For industries prioritizing sustainability and cost-effectiveness, optimizing the slurry transport process is more than just about immediate operational costs. Energy-efficient pump operation leads to reduced power consumption, lowering operational expenditure and contributing to a reduced environmental footprint. Moreover, leveraging advanced materials and coatings for pump components can significantly enhance durability and performance, resulting in fewer replacements and reduced waste.
slurry transport using centrifugal pumps pdf
In projects where the transport distance and elevation changes are significant, understanding the implications of system head on pump selection and operation is critical. Detailed system analysis, including evaluating pipeline friction losses and calculating the net positive suction head available (NPSHa), ensures that the centrifugal pump can handle the system’s demands without cavitation or undue strain.
Documented case studies and field experiences further enhance trustworthiness. For example, a mining operation that upgraded to high-performance centrifugal pumps experienced a marked improvement in throughput—reducing maintenance shutdowns by over 40% and achieving a 20% reduction in energy use. These tangible benefits underscore the importance of expert advice and investment in the right equipment.
Consulting with industry-leading authorities ensures access to cutting-edge technology and best practices. Many centrifugal pump manufacturers offer consultation services to tailor solutions specific to the operational needs, providing insights into potential upgrades and innovations that could benefit unique slurry transport scenarios.
Optimizing slurry transport using centrifugal pumps is both an art and a science that requires a blend of engineering acumen, practical experience, and a commitment to technological advancements. With conscientious application of these principles, endeavors in sectors like mining, wastewater treatment, and dredging can see marked improvements in operational efficiency, sustainability, and economic viability.