Understanding the components of a slurry pump is crucial for industries that deal with the transportation of abrasive or corrosive materials. Slurry pumps, with their robust design, play a pivotal role in ensuring efficient handling of such materials, making component knowledge an essential facet for optimizing performance and longevity.
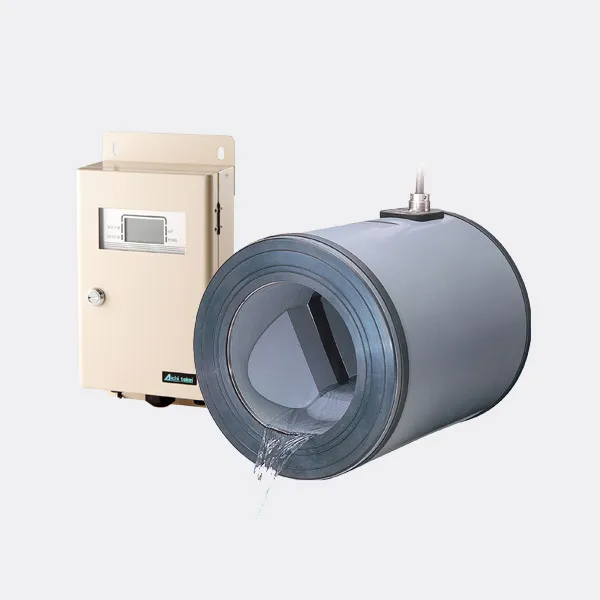
The Heart of a Slurry Pump The Impeller
At the center of any slurry pump you will find the impeller, a dynamically balanced rotor that plays a significant role in generating the centrifugal force necessary to move the slurry. Impellers are typically made of high chrome alloys or rubber materials to withstand the harsh conditions. Their design, often spiral-shaped, is optimized for different types of slurry, whether thick or fine, affecting both the efficiency and the energy consumption of the equipment. Selecting the right impeller is critical and often requires expert input to match the specific needs of an operation, thereby ensuring seamless function and prolonged service life.
Defending Against Wear The Material Selection
Material consideration in slurry pump components stands as a testament to expertise and engineering know-how. Since these pumps deal with a range of corrosive and erosive materials, choosing the right material is akin to mastering a craft. Options like high-manganese steel, stainless steel, and hard iron provide various degrees of toughness and resistance. Investing in the correct material involves understanding the slurry's composition, its pH level, and the presence of any solid particles.
This expertise ensures that the pump components are not only durable but also cost-effective over their lifespan.
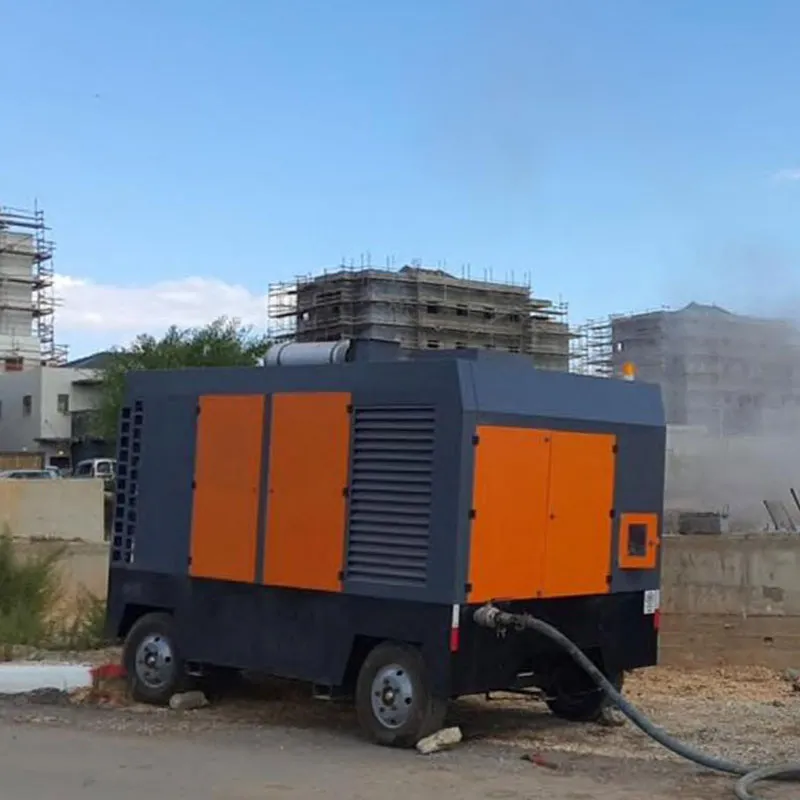
Precision and Tolerance Casing and Bearing Assembly
The casing is the armor that shelters the internal components from external damages and facilitates effective flow regulation. Precision in manufacturing the casing ensures minimal tolerance, promoting optimal flow dynamics that minimize wear and tear. Meanwhile, the bearing assembly acts as the framework that supports the loads imposed by dynamic operations. High-quality bearings minimize vibration and friction, key factors that could otherwise compromise the pump's structural integrity. Regular maintenance and monitoring of these components are imperative to maintain trust in the machinery's reliability.
Sealing Success Shaft and Sealing Options
A critical aspect often overlooked is the shaft and its associated sealing mechanisms. The shaft transmits power from the motor to the impeller, and its seamless operation is crucial for reducing leakage and contamination. Mechanical seals or gland packings are employed depending on the nature of the slurry and the operational context. While mechanical seals offer superior reduction in leakage, they require meticulous installation and maintenance, reinforcing the need for authoritative understanding of the machinery.
slurry pump components
Optimizing Performance Auxiliary Components
Equally significant are auxiliary components like the expeller and liners. The expeller aids in reducing pressure and preventing leakage, enhancing pump efficiency. Liners, on the other hand, act as a secondary defense line, absorbing the bulk of wear against the pump casing. The choice between rubber or metal liners requires a deep understanding of the slurry characteristics and the industrial application, embodying the experience-driven decisions needed to extend the pump's service life.
Advancing with Technology Monitoring and Automation Tools
Innovation in monitoring technologies for slurry pumps is reshaping the landscape by integrating smart sensors and automated controls that enhance authoritative supervision and trustworthiness in operations. Sensors that monitor vibration, temperature, and pressure provide real-time data, enabling proactive decisions that prevent untimely failures. Automation facilitates seamless integration with plant-wide systems, improving efficiency and reducing human error. The deployment of these technologies showcases forward-thinking and a commitment to harnessing expertise for operational excellence.
Lasting Durability Maintenance and Care Protocols
A comprehensive maintenance regime underscores the trust placed in slurry pump components. Routine inspections, diligent monitoring, and timely replacements are paramount for preserving their functionality. Engaging experts to perform assessments and implementing robust care protocols showcase reliability in maintaining equipment performance. This ensures not only the maximum return on investment but also the sustainability of operations.
A focused understanding of slurry pump components goes beyond surface-level knowledge. It demands a dedicated application of experience, expertise, authoritative decisions, and trustworthy practices, driving optimal performance and ensuring that industries can navigate the complex landscapes of material handling with confidence.