Slurry pumps are essential in industries that handle fluids with suspended solids, such as mining, dredging, pharmaceutical production, and wastewater treatment. Selecting and operating slurry pumps requires precise calculations to ensure optimal performance and longevity. These calculations involve understanding various parameters that impact the efficiency and durability of the pump system.
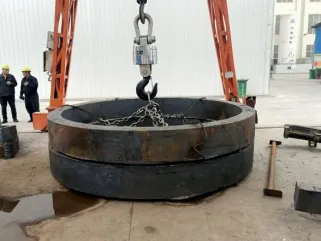
The cornerstone of slurry pump calculations begins with understanding the slurry's specific gravity and concentration by weight or volume. These factors directly affect the pump's hydraulic performance and wear rate. Calculating the slurry's specific gravity involves measuring the density of both the liquid and the solid components. This ratio is pivotal since a higher specific gravity means heavier slurries, which require more power to pump and potential adjustments to the pump system's design.
Another critical calculation is determining the slurry's flow rate, often measured in cubic meters per hour (m³/h) or gallons per minute (GPM). The flow rate will dictate the pump size and power needed to maintain efficient operation. Accurate estimation of the desired flow rate ensures that the system will meet production demands without overburdening the pump, which can lead to premature wear and increased operational costs.
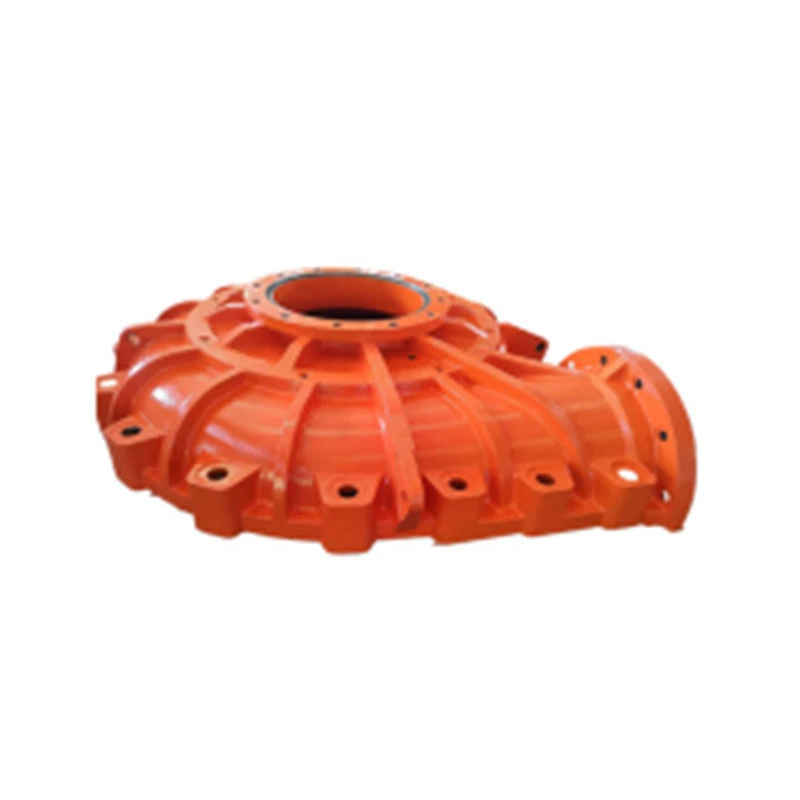
Head loss due to friction is another parameter that requires careful calculation. Slurry flow through pipes introduces friction, which results in energy loss. Engineers must calculate the total dynamic head (TDH), taking into account both the static lift and the dynamic loss due to friction. This calculation is crucial for selecting a suitable pump that can overcome this resistance, maintaining the desired flow rate without causing excessive energy consumption or wear.
Pump efficiency is not just about meeting operational specifications but also about extending the equipment's life. It's essential to select impellers and volutes that are compatible with the slurry's abrasive nature. Calculations related to the erosion and corrosion potential ensure that the materials used in pump construction can withstand the harsh conditions, thereby enhancing the pump's reliability and reducing unnecessary maintenance costs.
slurry pump calculations
Power consumption is a significant cost factor in any pumping operation. Calculating the brake horsepower (BHP) needed for the slurry pump involves understanding the total head and flow rate in correlation with the pump's efficiency. BHP calculations help in selecting motors that provide adequate power without oversizing, which can lead to inefficiencies and increased energy costs.
Moreover, slurry temperature can affect pump performance. High temperatures may lead to increased wear or change the slurry's properties, influencing calculations for specific gravity and viscosity. Ensuring that calculations account for operational temperature ranges can prevent adverse effects on both process efficiency and equipment lifespans.
Accurate slurry pump calculations are foundational to optimizing pump systems for industrial use. They not only enhance performance but also contribute significantly to the longevity of the pumping equipment and the efficiency of the operation. Leveraging expertise in these calculations ensures that systems are not only designed to handle current operational demands but are also adaptable to future needs.
Detailed knowledge and experience in slurry pump calculations are indispensable. Utilizing advanced modeling software and analytical tools can enhance these calculations, providing more precise predictions and allowing for preemptive adjustments to pump systems. As technology advances, these tools are becoming integral to ensuring that slurry pumping remains both efficient and economical.
In conclusion, the effective application of slurry pump calculations requires a blend of expertise, experience, and reliable data. By focusing on these critical calculations, industries can significantly improve operational efficiency, extend equipment lifespans, and reduce costs—all while maintaining a commitment to responsible engineering practices.