In the intricate world of industrial operations, the efficiency of machines often dictates the success of tasks, especially those involving the deployment of slurry pumps. At the heart of these pumps lies a crucial component the slurry pump seal, or sello de la bomba de lodo. This seemingly small part plays an indispensable role in ensuring the machine operates efficiently, securely, and with minimal downtime.
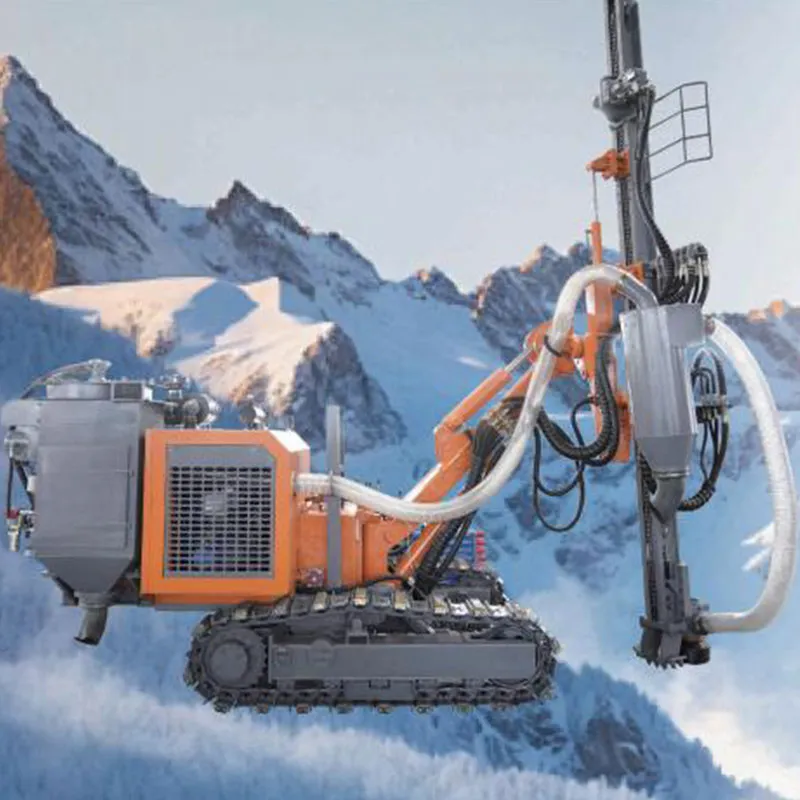
Slurry pump seals are engineered to withstand the aggressive and abrasive nature of the substances they work with. The slurry often contains a mixture of water and solids, and these solids have the potential to cause significant wear and tear on the machinery. A high-quality slurry pump seal is designed to be robust, combating the potential damage from continuous exposure to such harsh environments. This enhances the longevity of the pump, reducing maintenance needs and costs—an essential feature for industries relying heavily on pumping activities.
Professionals in the field highlight the importance of selecting the right seal for specific industrial applications. For instance, in the mining sector, slurry pumps often deal with highly abrasive materials such as rocks and sand. Here, the seal must not only be durable but also capable of preventing leakage and maintaining hydraulic balance. Selecting a seal with materials specifically designed to handle such abrasives, such as tungsten carbide or silicon carbide, can significantly enhance performance and reliability.
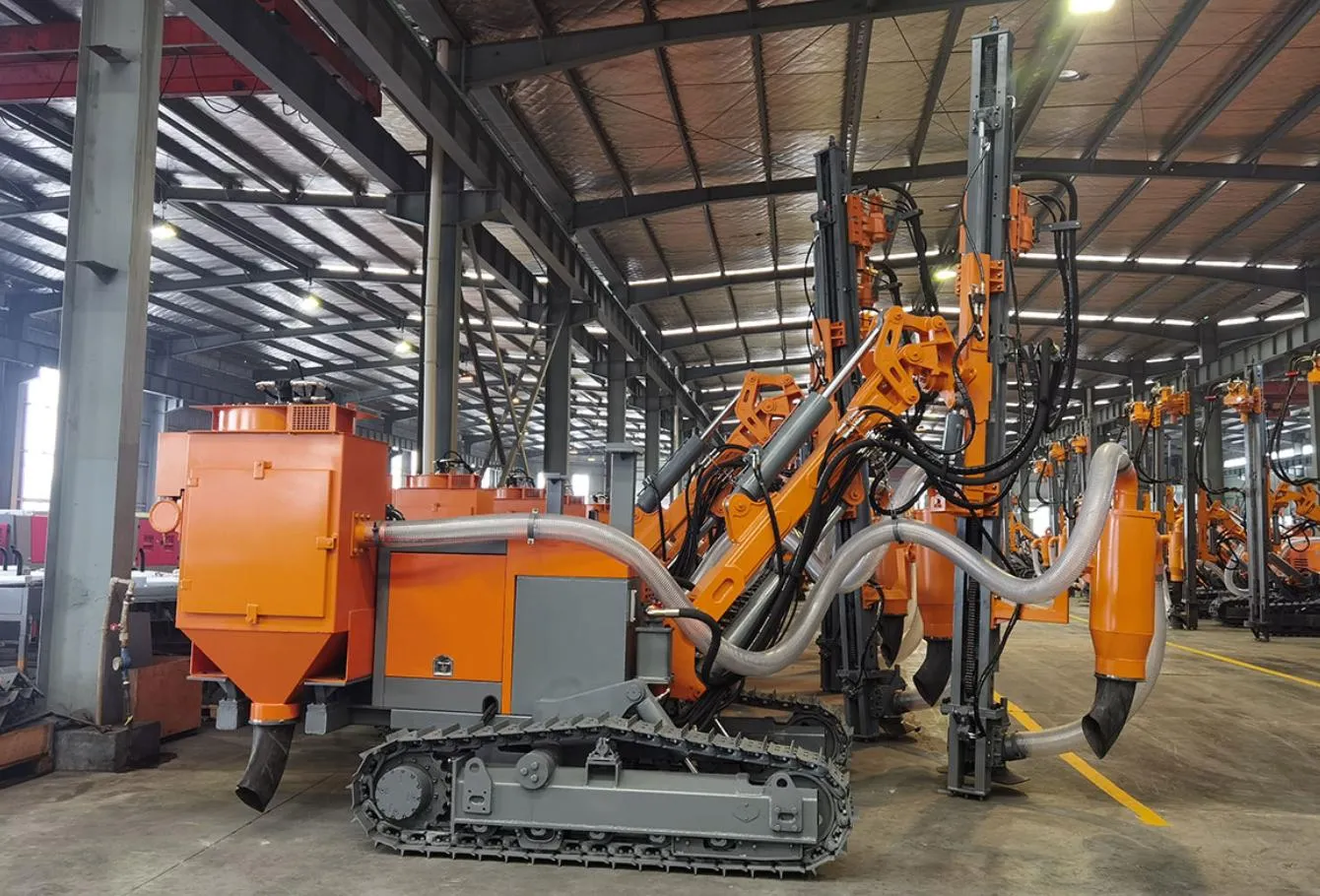
Experts assert that beyond material selection, the design of the seal is equally critical. Seals come in a variety of forms including gland packing seals, mechanical seals, and cartridge seals. Each type has its specific benefits and is chosen based on the operational conditions. Mechanical seals, for example, offer a better sealing performance and longer service life compared to traditional packing seals, thus, they are preferred in high-pressure and high-speed pump environments.
The installation and maintenance of slurry pump seals demand expertise and precision. Improper installation can lead to premature wear or failure, resulting in unplanned downtime that can be costly.
Regular inspections and maintenance are advised to ensure that seals remain in optimal condition. Periodic maintenance not only includes inspection but also cleaning and adjusting the seal alignment, ensuring they function at their highest efficiency. Trust in the reliability of your slurry pump is intrinsically tied to the proper management of the seals.
sello de la bomba de lodo
Authoritative figures in equipment manufacturing emphasize customization and innovation in slurry pump seals. New materials and innovative designs, like those incorporating self-lubricating properties, have been developed to enhance performance even further. These developments represent a commitment to adapting to the burgeoning demands of ever-evolving industrial applications.
Customer experiences provide valuable insights into the real-world performance of slurry pump seals. Many industry veterans report a marked improvement in productivity and cost-efficiency after upgrading to newer models of seals. These tangible benefits underscore the importance of staying updated with the latest technological advancements in pump seal technology.
For any operation dealing with heavy-duty slurry pumps, understanding the significance of appropriate seal selection, installation, and maintenance is pivotal. Investing in high-quality seals pays off multifold, through increased efficiency, reduced maintenance intervals, and prolonged machinery life. Trustworthiness in daily operations is fortified through such strategic investments.
Ultimately, the slurry pump seal stands as a testament to the advancement of industrial components; an embodiment of engineering expertise, experience, and reliability. As industries propel towards greater efficiencies and environmental stewardship, this small yet mighty component will continue to be a cornerstone of operational excellence.