The evolution of industrial machinery has allowed for significant advancements in mineral processing, particularly in the sphere of cone crushers. One critical component that enhances the efficiency and longevity of these machines is the cone crusher lining, known in the industry as revestimiento de triturador de cono. Selecting the appropriate lining can be the difference between a machine that only survives and one that thrives, proving its worth through sustained high performance and durability.
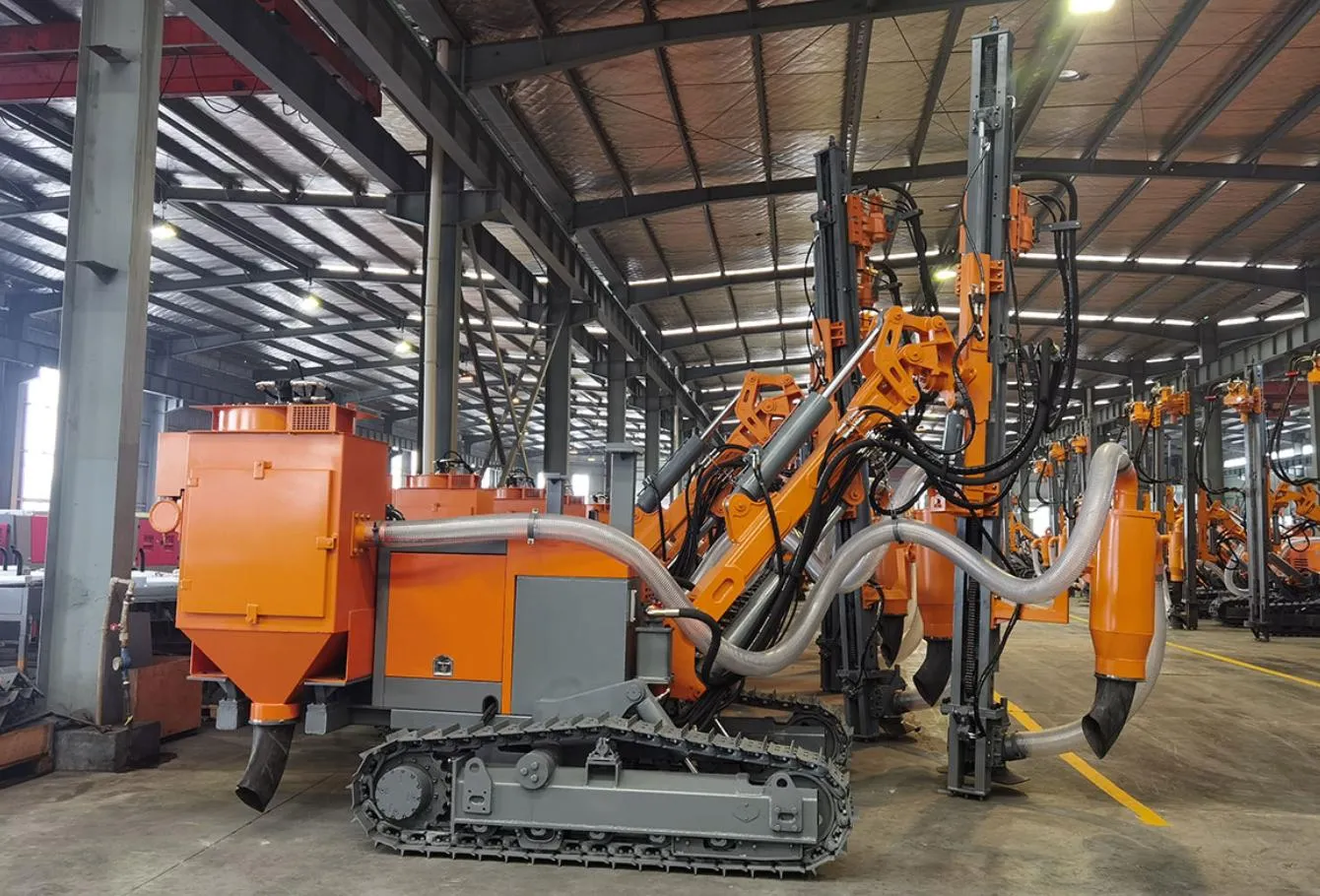
Understanding the expertise behind revestimiento de triturador de cono requires a look into the materials science involved in its manufacture. Linings are subject to extreme wear and tear due to the abrasive nature of materials processed, necessitating the use of heavy-duty alloys or composites. A leading choice within the industry is manganese steel, renowned for its hardness and resistance to wear. However, in recent years, newer materials such as high chrome iron and ceramic composites have gained traction. These materials promise enhanced durability and performance, reducing downtime and maintenance costs. The specific choice of material often hinges on the exact nature of the processed rock, reinforcing the crucial role of expertise in material selection.
From an authoritative standpoint, manufacturers who produce revestimiento de triturador de cono with advanced metallurgical technologies often set the standard in the market. Companies like Metso and Sandvik, known for their pioneering research and development initiatives, provide not only a product but a promise of quality and innovation. Establishing a partnership with such manufacturers ensures access to cutting-edge technology, contributing to a crusher’s efficacy. Their years of accumulated knowledge lend credibility and assurance to operators who rely on crushers for demanding tasks in mining and construction.
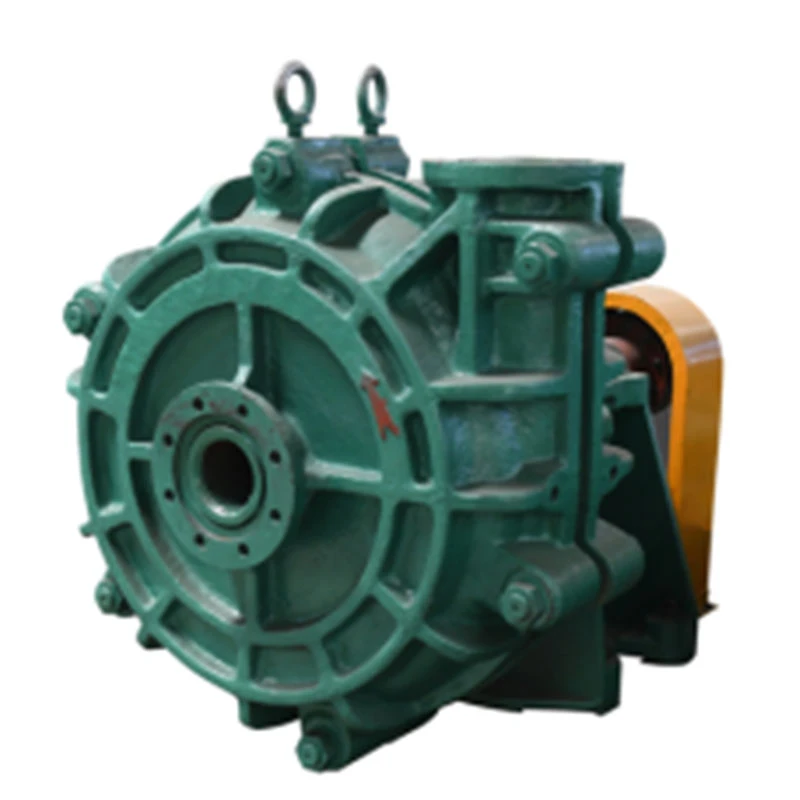
Trustworthiness plays a pivotal role in the selection process of cone crusher linings. End-users heavily depend on real-world testimonials and case studies, which reflect actual performance metrics and extended lifespans. When a lining consistently surpasses its estimated operational life, it becomes a testament to its quality. Operators observe improvements in uptime and overall productivity, underscoring a successful investment. Furthermore,
data-driven insights into failure rates and wear patterns bolster confidence, guiding maintenance schedules and procurement decisions.
revestimiento de triturador de cono
In practice, the deployment of the right cone crusher lining results in tangible improvements in processing plants. Mining companies have reported back on specific performance metrics after switching their linings — output material quality, reduced operational costs, and improved safety standards are notable outcomes. These anecdotal evidences, while not purely scientific, accumulate to build a narrative of reliability around a quality product.
Ultimately, professionalism in the selection and maintenance of revestimiento de triturador de cono is paramount. It calls for skilled technical teams to gauge wear regularly and replace linings at optimal intervals to ensure constant machine efficiency. Likewise, predictive maintenance technologies have proven indispensable, as sensors and real-time monitoring systems aid in forecasting wear and determining the timing for lining replacement.
As the discussion surrounding cone crusher linings continues to evolve, it is imperative that industry professionals keep abreast of advancements in material science and production techniques. By doing so, they not only extend the operational life of their machinery but also enhance productivity and safety, driving greater returns on investment. Thus, a deep understanding and strategic selection of revestimiento de triturador de cono are essential for any operation seeking to leverage its assets to the fullest.