Transporting sludge in industrial settings requires the right equipment to ensure efficiency and safety. The choice of pump is pivotal not only for operation but also for long-term performance. Among the many options available, centrifugal pumps, progressive cavity pumps, and peristaltic pumps are the most effective in handling sludge.
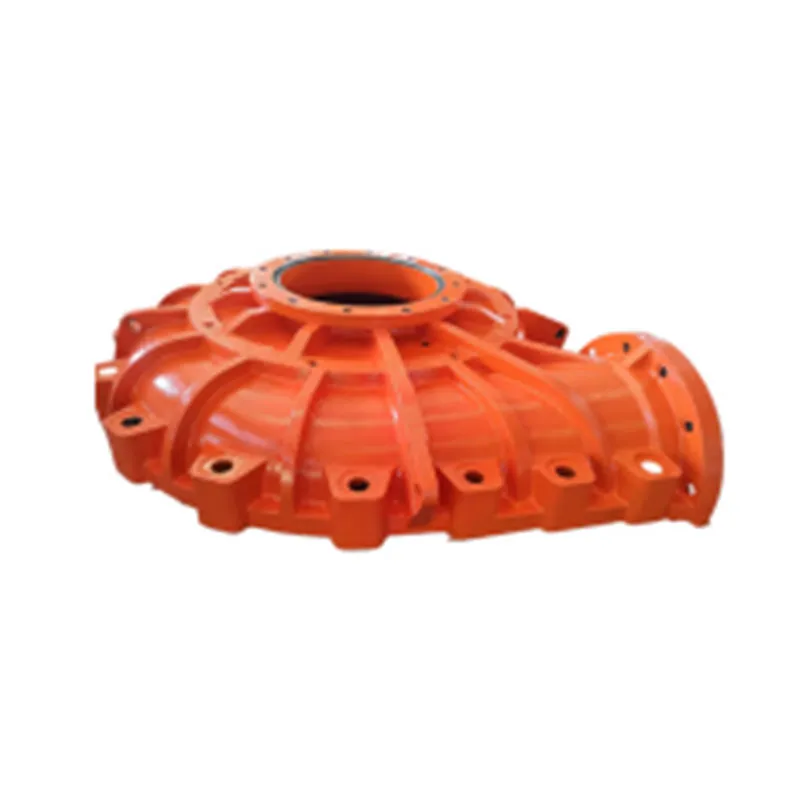
Centrifugal pumps have long been a staple in the industry, known for their reliability and high flow rate capabilities. These pumps operate by converting rotational kinetic energy, typically supplied by an electric motor, to energy in a moving fluid. However, they are generally best suited for fluids with low viscosity. When handling sludge, especially when it's thick, centrifugal pumps might struggle. The presence of suspended solids can cause wear and tear on the components over time, leading to frequent maintenance and operational downtime.
For applications involving thickened or viscous sludge, progressive cavity pumps are highly recommended. Known for their ability to handle fluids with high levels of solid content, these pumps operate using a rotor and stator to create cavities for moving the material forward. This positive displacement design ensures a uniform flow without pulsation, which is crucial in maintaining pipe and equipment integrity. Their capacity to handle high-viscosity fluids with substantial solids makes them favorable in wastewater treatment, mining, and other industries dealing with sludge.
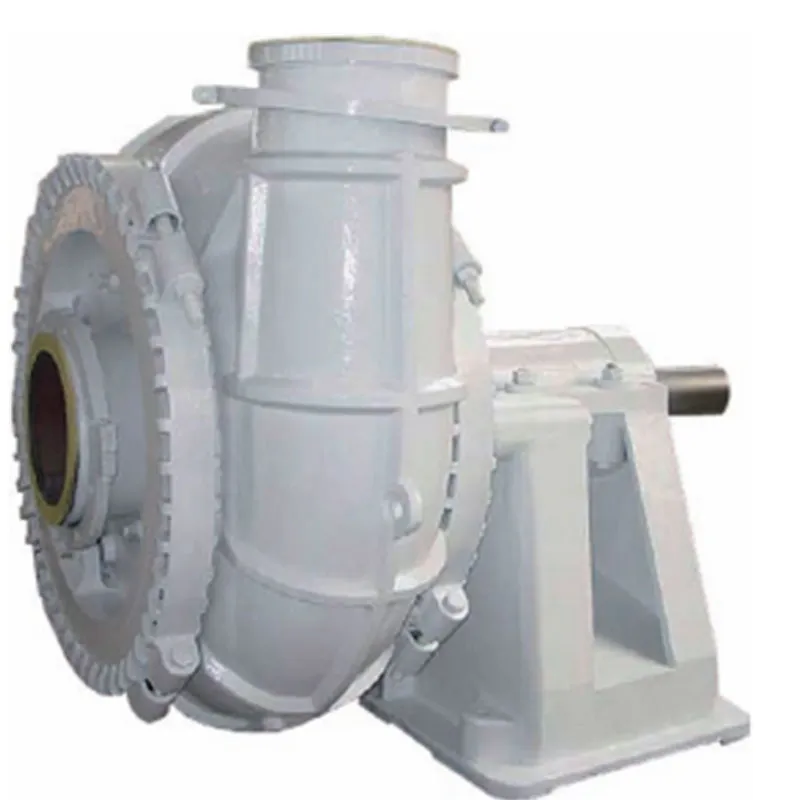
Peristaltic pumps offer another effective solution, especially for applications where a gentle pumping action is required to minimize degradation of the sludge composition. These pumps work by compressing and releasing a flexible tube or hose, moving the content in a wave-like fashion. Since the fluid is contained entirely within the tube, these pumps are ideal for abrasive, corrosive, or viscous fluids. The self-priming nature and ability to run dry without damage further enhance their versatility in sludge pumping scenarios.
When selecting a pump, several factors should be considered to align with the operational needs and constraints. The viscosity and concentration of solids in the sludge greatly influence the type of pump that should be used. Additionally, the distance over which the sludge needs to be transported, as well as the elevation changes throughout the piping system, play significant roles in determining the required pump power and capacity.
What pump is used to transport sludge?
In considering the pump material,
attention should be given to the corrosive nature of the sludge. Materials such as stainless steel or high-grade alloys might offer greater longevity compared to standard steel, particularly in chemically reactive environments. Modern coatings and surface treatments also enhance resistance to abrasion and chemical attack, further extending the service life of the pumps.
For optimizing the performance and longevity of sludge transfer pumps, proper maintenance practices cannot be overlooked. Routine inspections and timely replacements of worn parts help prevent unexpected failures. Utilizing real-time monitoring systems can alert operators to irregularities in pump operation, allowing for proactive maintenance and reducing downtime.
Furthermore, selecting a pump with energy-efficient motors and variable frequency drives can significantly reduce operational costs while providing precise control over the pumping process. This energy-conscious approach not only contributes to sustainability goals but also enhances the overall economic efficiency of the operation.
Lastly, consulting with pump experts and manufacturers early in the selection process provides the chance to leverage their extensive knowledge, ensuring that the chosen solution is tailored to the specific requirements of the operation. Their expertise contributes to a more in-depth understanding of the latest technological advancements and best practices in sludge pumping.
In conclusion, the selection of an appropriate pump for transporting sludge involves a comprehensive understanding of the sludge characteristics, operational environment, and maintenance considerations. By carefully evaluating each parameter and seeking expert guidance, industries can ensure efficient, reliable, and cost-effective sludge management solutions.