Pump shaft bars serve as critical components in various industries that require robust and efficient mechanical systems. These bars, fundamental to the operational success of pumps, are vital for ensuring smooth operation and the long-term durability of the machinery they are part of. This article delves into the world of pump shaft bars, discussing their significance, material composition, manufacturing process, application, and maintenance, while emphasizing the importance of choosing the right product to meet specific industrial needs.
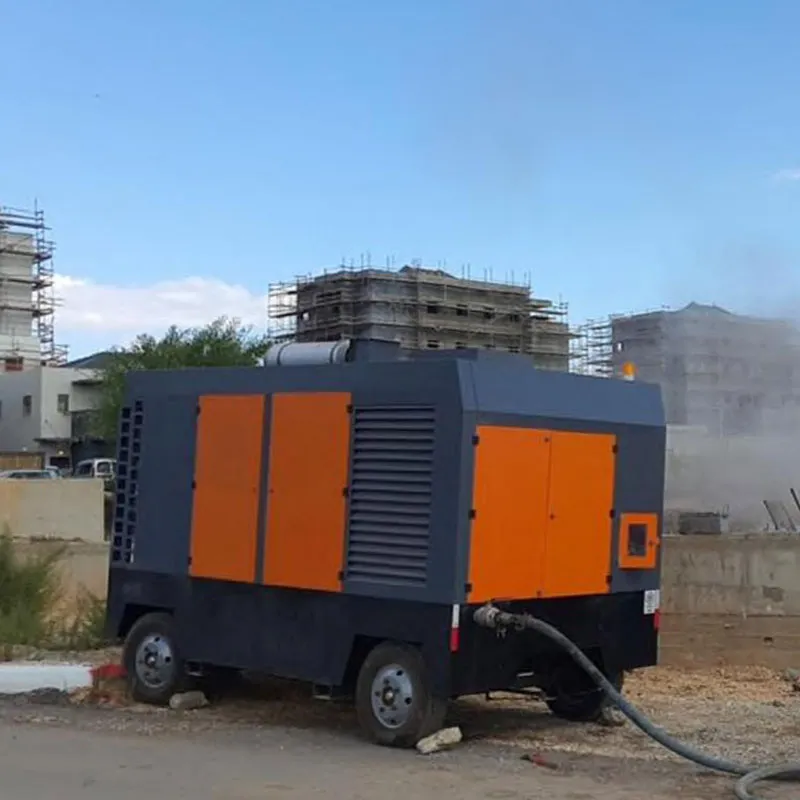
Pump shaft bars are specially designed rods used in centrifugal and other types of pumps, playing a vital role in the transmission of mechanical power from the motor to the impeller or rotor in a pump. Their primary function is to transfer torque while withstanding the operational forces encountered within the pump system. The correct pump shaft bar can significantly enhance pump performance, reduce maintenance costs, and extend the lifespan of the machinery.
The composition of a pump shaft bar is a critical factor that determines its performance and durability. High-grade materials such as stainless steel, carbon steel, and special alloys are commonly used due to their excellent mechanical properties, including strength, flexibility, and corrosion resistance. Stainless steel, for instance, is particularly valued for its ability to resist wear and corrosion, making it ideal for applications in harsh environments or with corrosive fluids.
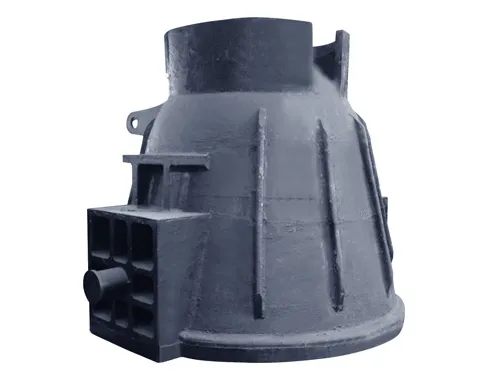
Manufacturing pump shaft bars involves a meticulous process to ensure the final product meets high standards of precision and quality. The process includes several crucial steps cutting, heat treatment, machining, and finishing. Precision machining is essential to achieve the exact dimensions and tolerances necessary for the pump system. Moreover, heat treatment processes such as quenching and tempering are employed to enhance the mechanical properties of the bars, improving hardness and tension strength.
In terms of application, pump shaft bars are used within a wide range of sectors, including water and wastewater management, oil and gas, chemical processing, and food and beverage production. Each of these industries demands specific features and adaptations of pump shaft bars, depending on the fluid being pumped and the environmental conditions. For example, in the oil and gas industry, shaft bars must withstand high pressures and temperatures, as well as exposure to potentially corrosive substances.
pump shaft bar
Ensuring the pump shaft bars continue to function reliably requires regular maintenance and inspection. Routine checks for signs of wear, corrosion, or damage can prevent unexpected failures and costly downtimes. Additionally, proper installation and alignment are critical; misalignment can lead to uneven wear and increased stress on the shaft bar, ultimately resulting in fracture or deformation.
Choosing the right pump shaft bar is essential for optimal pump performance. This decision should be based on a thorough understanding of the operational requirements, environmental conditions, and fluid characteristics of the application. Consulting with expert manufacturers who possess extensive experience and technical knowledge can provide valuable insights, helping businesses select materials and designs best suited to their needs.
Authoritative manufacturers in the pump shaft industry often provide valuable services beyond just supply, including technical support, custom engineering solutions, and comprehensive product warranties. Such services enhance trustworthiness and reliability, ensuring that customers receive not only high-quality products but also the assurance that any potential issues will be addressed promptly and effectively.
Thus, pump shaft bars are indispensable components that require careful consideration and selection. By focusing on the material properties, manufacturing quality, appropriate application, and diligent maintenance, industries can harness the full potential of these critical elements to drive efficiency and performance.