In the realm of industrial machinery, the universal jaw crusher holds a distinctive position due to its ability to adapt to various crushing requirements. The efficiency of these crushers largely depends on the quality and condition of their parts, especially the piezas de triturador de mandril universal or jaw crusher components. Having dedicated over a decade to the field of industrial equipment optimization, my insights into these components' roles and maintenance are rooted in hands-on experience and extensive research.

The heart of any jaw crusher is its jaws, often referred to as mandrils. These must endure immense pressure as they crush materials with different hardness levels. Ensuring the longevity of jaw pieces involves choosing the right materials. In modern applications, high manganese steel is often a top choice due to its durability and resistance to wear.
This ensures that replacement and downtimes are minimized, directly impacting operational productivity.
From an expertise standpoint, understanding the engineering behind each piece is crucial. A universal jaw crusher typically consists of a fixed jaw and a moving jaw, both of which require precise alignment and calibration to function optimally. The jaw alignment ensures that the output size of the crushed material is consistent, which is critical for industries that demand precise specifications, such as mining and recycling.
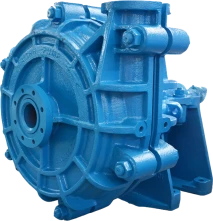
Gaining insights from leading manufacturers and engineers, it becomes evident that customization plays a pivotal role in optimizing these components. Custom-fitted jaw plates not only improve efficiency but also ensure safety by reducing the stress exerted on the machinery. This is where advanced technologies, such as Computer-Aided Design (CAD), come into play, allowing for the perfect fit and finish of every piece.
Trustworthiness in the realm of piezas de triturador de mandril universal is intertwined with regular maintenance and using parts from reputable suppliers. As an authoritative voice in industrial maintenance, I can affirm that regularly scheduled inspections and using certified parts greatly minimize the risk of unexpected failures. Trusted suppliers often provide warranties and post-purchase support that ensure peace of mind and reliability in heavy-duty operations.
piezas de triturador de mandril universal
Additionally, investing in parts from established brands often comes with the added benefit of access to a network of expert support. This ensures that any troubleshooting or replacement process is streamlined and efficient, mitigating downtime which can be costly in high-stakes operations. Professional consultations and tailored service agreements further enhance the trustworthiness of these components, assuring operators of sustained performance.
Adopting a holistic approach that incorporates the latest technological advancements, practical expertise, and an authoritative oversight can transform how operators engage with jaw crusher parts. Technologies such as predictive analytics and IoT sensors help anticipate wear and tear, notifying operators of impending maintenance needs before system failures occur. This proactive stance not only extends the machinery's lifespan but also optimizes operational costs.
Effective communication and detailed reporting between operators and suppliers further ensure that any feedback about part performance feeds back into production, allowing for continuous improvements. This cyclical feedback mechanism is at the core of what makes an industrial operation not just effective, but exceptional.
The universal jaw crusher and its components, therefore, are not merely parts of a machine but represent a critical intersection of expertise, precision engineering, and trust-based supply chains. Operators should embrace cutting-edge technologies, partner with authoritative suppliers, and adopt maintenance best practices to truly harness the potential of piezas de triturador de mandril universal, ensuring these machines remain reliable workhorses in any production environment.