In the industrial machinery sector, precisely in the context of jaw crushers, wear parts play a crucial role in ensuring efficiency and extending the lifespan of equipment. The term piezas de desgaste de triturador de mandril refers to these essential components. Understanding their importance, materials used, and the maintenance involved is vital for businesses that heavily rely on crushing machinery.
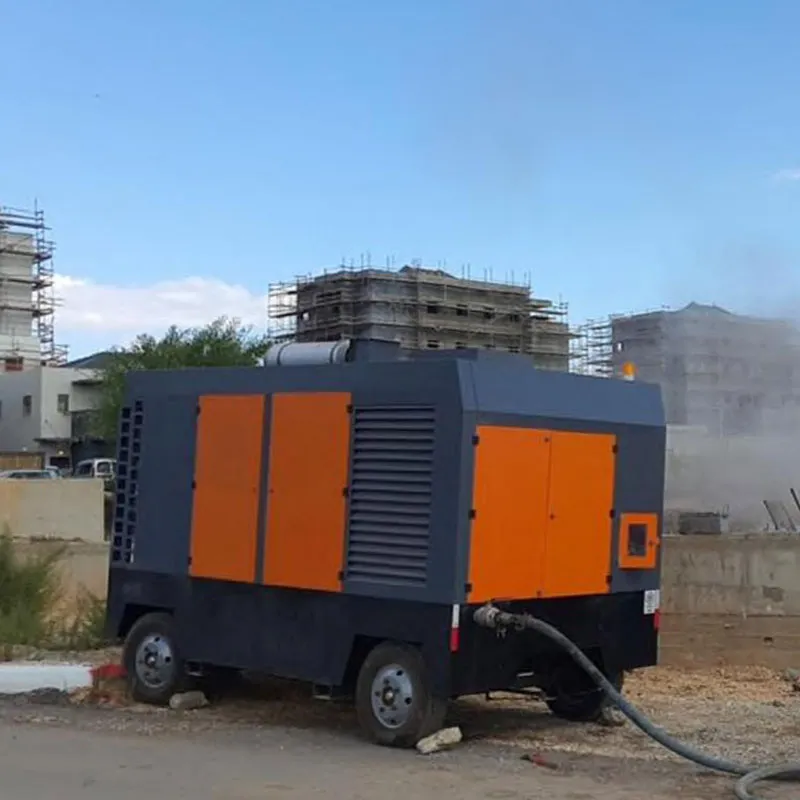
Jaw crushers are essential in the mining and construction industries, offering raw material processing through mechanical pressure. These machines are known for their durability and effectiveness, but to maintain their performance, attention must be directed towards the wear parts. The wear parts in jaw crushers typically include the jaw plates, cheek plates, and toggle plates.
The jaw plates are perhaps the most critical wear parts. Positioned at the top of the machine, they crush the material against a fixed plate. The crushing process subjects these plates to constant friction and heavy loads, leading to inevitable wear and tear. To mitigate this wear, manufacturers utilize materials like manganese steel, known for its high impact strength and resistance to abrasion. Some advanced versions may include ceramic or carbide inserts for enhanced durability. Balancing hardness and toughness in the materials used for jaw plates is essential to avoid premature failures and unscheduled downtimes.
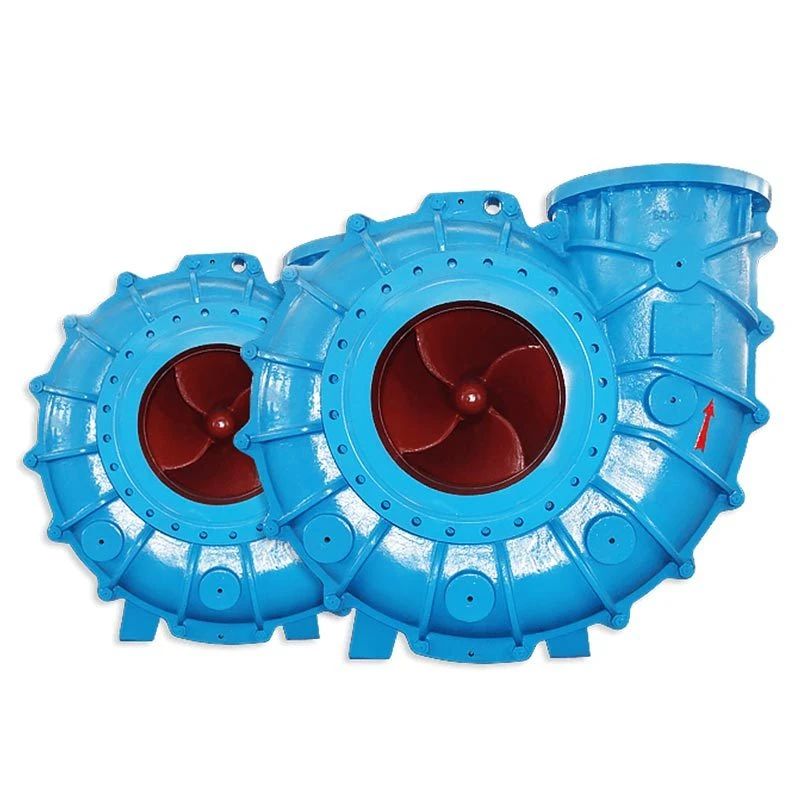
Cheek plates, placed on the sides of the machine, similarly protect the main frame from wear. These secondary plates are designed to absorb impact and abrasion, thereby prolonging the crusher's life. Although not subjected to the same pressure as jaw plates, their strategic positioning ensures the structural integrity of the jaw crusher.
Toggle plates act as the safety mechanism within jaw crushers. They play a crucial role in the machine's operation, absorbing excessive shocks and acting as a fulcrum point during crushing. While they don’t wear out as quickly as the jaw plates, they remain susceptible to deformation under extreme pressure situations.
piezas de desgaste de triturador de mandril
Selecting the right material and design for these wear parts is not merely a matter of cost but a strategic decision that affects operational efficiency and productivity. Companies need to consider several factors, such as the material's abrasiveness and hardness, desired product size, and the crusher's capacity.
Routine maintenance of wear parts is crucial in maximizing the efficiency and longevity of jaw crushers. Regular inspection for signs of wear and timely replacement of parts can prevent major breakdowns. Ensuring that the wear parts fit correctly and are secured tightly reduces the chances of catastrophic failure. Operators must be trained to detect unusual vibrations or noises that could indicate wear parts are becoming ineffective.
Working with a reputable supplier for wear parts is another significant aspect. Suppliers should provide not only high-quality parts but also expert advice on maintenance and performance optimization. Companies that establish strong partnerships with suppliers gain access to advanced wear technologies and materials that can substantially benefit their operations.
Innovation in wear part materials and design is also a dynamic field. Researchers and manufacturers continually develop new alloys and composite materials to enhance the durability and efficiency of jaw crushers. Cutting-edge techniques like computer-aided simulations and 3D printing offer opportunities to design wear parts that meet the specific needs of distinct operational environments.
In conclusion, wear parts are an indispensable component of jaw crushers, directly influencing the machine's productivity and operational efficiency. By focusing on high-quality materials, proper maintenance routines, and innovative partnerships with suppliers, operators can ensure their machinery performs optimally while minimizing downtime and reducing operational costs. The expertise in handling these aspects not only enhances business operations but also builds a trustworthy reputation in the industry, evidencing a firm's commitment to operational excellence and customer satisfaction.