Drilling machines, often the unsung workhorses of various industries, play a pivotal role in sectors ranging from construction to manufacturing, mining, and oil extraction. Their ability to penetrate the earth or material surfaces to create precise and clean holes cannot be overstated. This article delves into the intricacies of drilling machines, combining real-world experience with authoritative insights to provide a comprehensive guide for anyone looking to deepen their understanding or optimize their use of these essential tools.
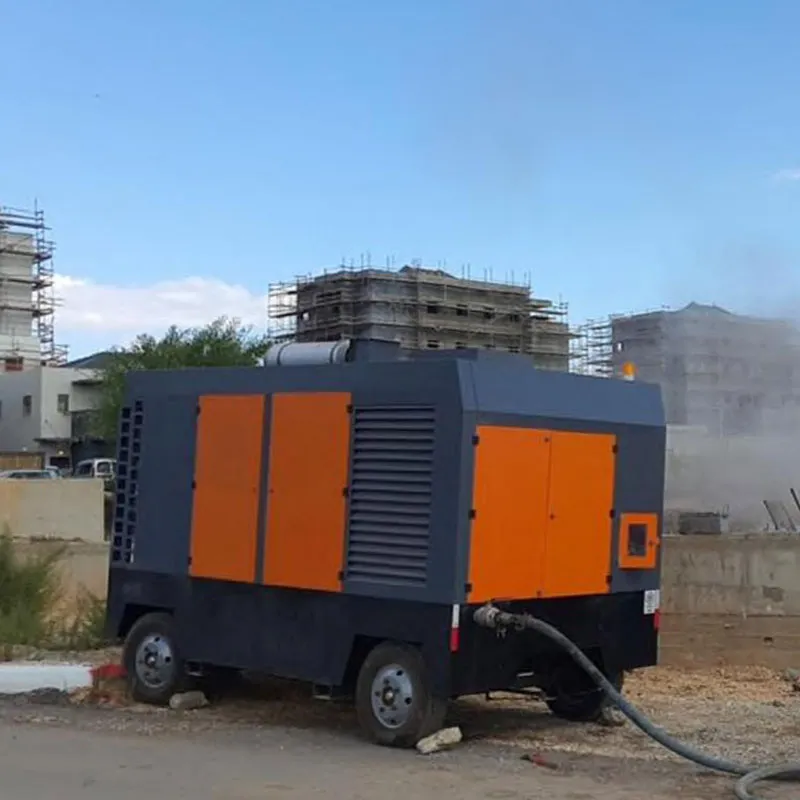
Drilling machines come in various types, each suited to specific tasks and materials. Among the most common are rotary drilling rigs, which are prized for their versatility in both continuity and precision. This type of machine is widely used in mining to extract minerals and in the oil industry to tap into deep-seated reserves buried beneath the Earth's surface. From an expert perspective, the choice of drill bit is crucial; selecting the right bit in terms of material and design can significantly enhance the efficiency and lifespan of a rotary drilling session.
Another popular type is the hammer drill, often utilized in construction for masonry and concrete tasks. Its high-impact force enables efficient drilling through tougher materials. For optimal performance, experts recommend maintaining proper angle and speed settings to prevent bit wear and ensure accurate results. Experience shows that a well-maintained hammer drill can dramatically reduce downtime and project costs.
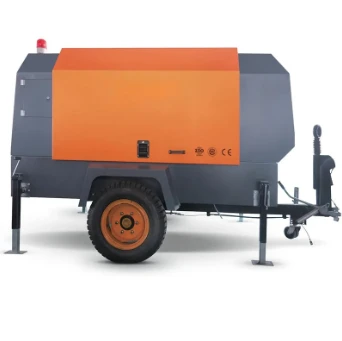
Precision is key in the manufacturing sector, where CNC (Computer Numerical Control) drilling machines are frequently employed. These sophisticated machines are revered for their precision and repeatability, essential in producing complex parts and assemblies. Expertise in CNC programming and machine calibration can lead to an impressive increase in productivity and product quality. It's vital to ensure that operators are adept at both programming these devices and maintaining them to prevent costly errors.
Horizontal directional drilling (HDD) has gained fame, particularly in the utility sector, for installations beneath obstacles like roads and rivers without disrupting surface activities. This trenchless technology requires thorough planning and precise execution, wherein a pilot bore is controlled by azimuth and inclination sensors. Trust in the equipment and operators' expertise ensures successful installations with minimal ecological impact, which has become increasingly important in urban planning and development.
Drilling machines
The authoritative edge in the field of drilling machines stems from a solid foundation in safety practices. Operators and technicians must adhere to stringent guidelines to forestall accidents and equipment failures. Regular training sessions and audits enhance competence, while reliable documentation ensures traceability and accountability. Trustworthy operations often highlight the best industry practices, promoting a culture of safety and professionalism.
The future of drilling machines also cannot be overlooked. Innovations like automation, AI, and sustainable technologies are reshaping the landscape. Automated drilling systems can perform complex tasks with minimal human intervention, reducing fatigue and increasing precision. Meanwhile, AI systems contribute to predictive maintenance, minimizing downtime by forecasting equipment failures before they occur.
Sustainable drilling solutions such as electric and hybrid systems are making inroads, driven by a collective push to reduce fossil fuel dependency. With expertise and experience, these innovative machines not only offer environmental benefits but also enhance operational efficiency by lowering long-term energy costs.
Despite the technological advancements, the essence of a successful drilling operation remains grounded in the synergy of equipment and human expertise. An authoritative understanding of the machines, combined with hands-on experience, ensures optimal use and outcomes. Trustworthiness in handling these complex operations cements a company’s reputation, solidifying its stance as a leader in the competitive landscape.
In conclusion, drilling machines are indispensable across numerous industries, each machine tailored for specific demands. A keen understanding of their functionalities, combined with ongoing advancements and best practices in safety and maintenance, provides businesses with a definitive edge. For stakeholders, harnessing the full potential of drilling machines not only optimizes performance but also aligns with the future trajectory of sustainable and efficient industrial operations.