The moving jaw plate is a pivotal component in the crushing mechanics of jaw crushers, devices that are fundamental in the mining, recycling, and aggregate industries. These machines contribute to the fragmentation of extensive rock and ore into smaller, more manageable fragments or, indeed, achieve pulverization for subsequent processing. The efficiency and durability of a jaw crusher predominantly rest on the quality and design of its components, notably the moving jaw plate.
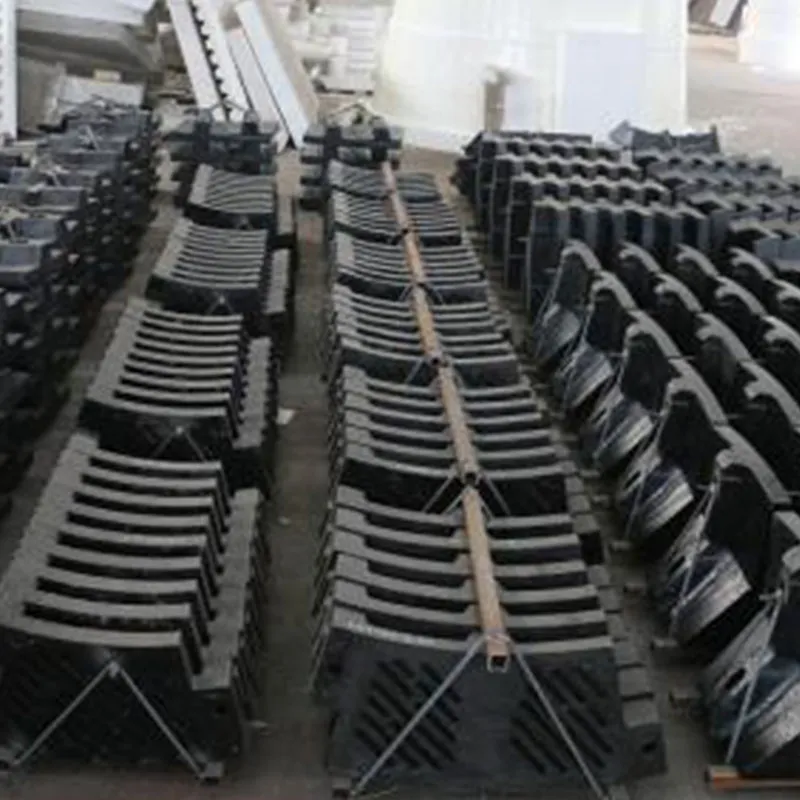
In the realm of mineral processing, the moving jaw plate operates as a dynamic surface, oscillating back and forth to compress materials against a fixed jaw plate. Crafting this component demands an intricate balance of material science and mechanical engineering. Typically fabricated from manganese steel due to its robust nature, the moving jaw plate benefits from the metal's outstanding wear resistance and work-hardening properties. This ensures longevity and consistent functionality even under severe operational conditions where significant stress and strain are daily occurrences.
The importance of the moving jaw plate extends beyond mere material breakdown.
Its design determines the crusher's throughput and particle size distribution. A plate with optimized geometry and thickness reduces material slippage, enhances grip, and allows for more efficient force application. Consequently, manufacturers meticulously analyze the crusher's intended applications and the properties of the rocks to devise an effective jaw plate configuration.
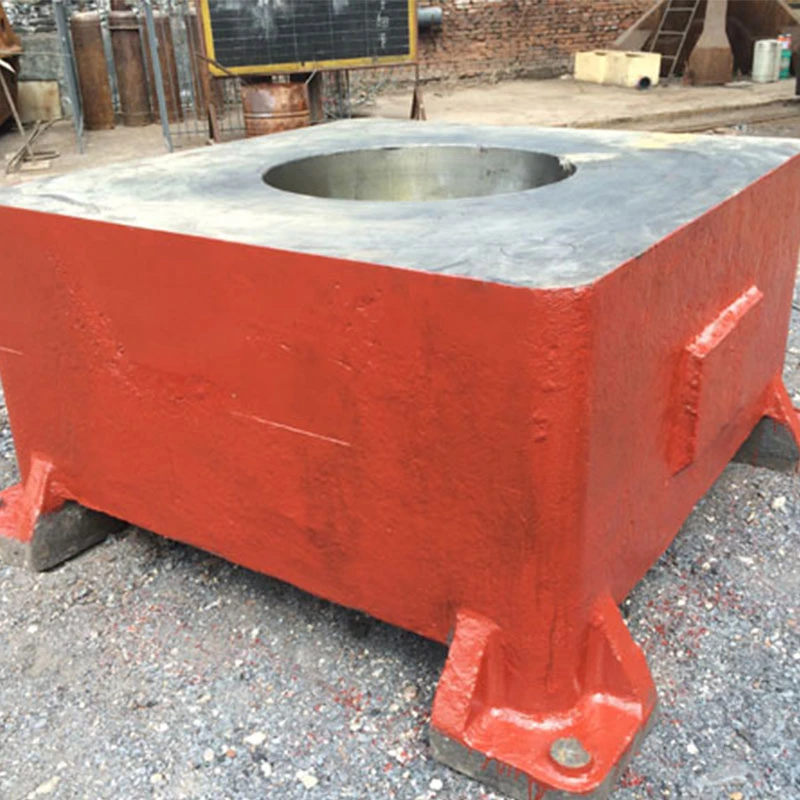
Experience in the field has shown that even with the best initial design, the wear and performance of the moving jaw plate can be substantially affected by several operational factors. These include feed material hardness, moisture content, and feed size. Regular monitoring and analysis are required to understand wear patterns, allowing for timely adjustments or replacement. This proactive approach ensures the jaw crusher sustains its productive capacity and minimizes unscheduled downtime, which could disrupt operations.
moving jaw plate
Professionals in the industry often advocate for a comprehensive preventative maintenance program that comprises visual inspections, hardness testing, and employing advanced technologies such as laser scanning to track wear. Such expertise-driven practices are not merely for longevity; they contribute to maintaining a consistent reduction ratio and achieving a reliable output quality.
Another consideration in managing moving jaw plates is the integration of modern engineering solutions such as 3D modeling and simulation. These technological advances allow for precise testing and refinements in virtual environments before production, optimizing for factors like load distribution and stress control. Such authoritative use of technology ensures that the jaw plates produced are of the highest quality and tailored for their specific application.
A testament to the trustworthiness of a well-designed moving jaw plate is its performance under extreme conditions. Reliability in these components builds trust with operators and managers, knowing that their equipment can withstand harsh environments without unexpected failures, thus safeguarding operational efficiency and safety.
In conclusion, understanding and optimizing the moving jaw plate's function, material composition, and design are crucial in achieving optimum operational performance. Industry expertise and real-world experience emphasize the importance of regular maintenance, monitoring, and leveraging cutting-edge technology to ensure these components remain durable, effective, and trustworthy. When these elements are in place, companies can rely on their jaw crushers for prolonged periods, finding confidence in their machinery's ability to deliver consistent and expected results.