The materials used in the construction of a water pump shaft play a crucial role in the overall efficiency, durability, and performance of the pump. As an essential component of fluid handling systems, water pump shafts are fundamental in industries ranging from automotive to agriculture. Here, a deep dive into the materials commonly utilized for water pump shafts offers insights into their strengths, weaknesses, and applications.
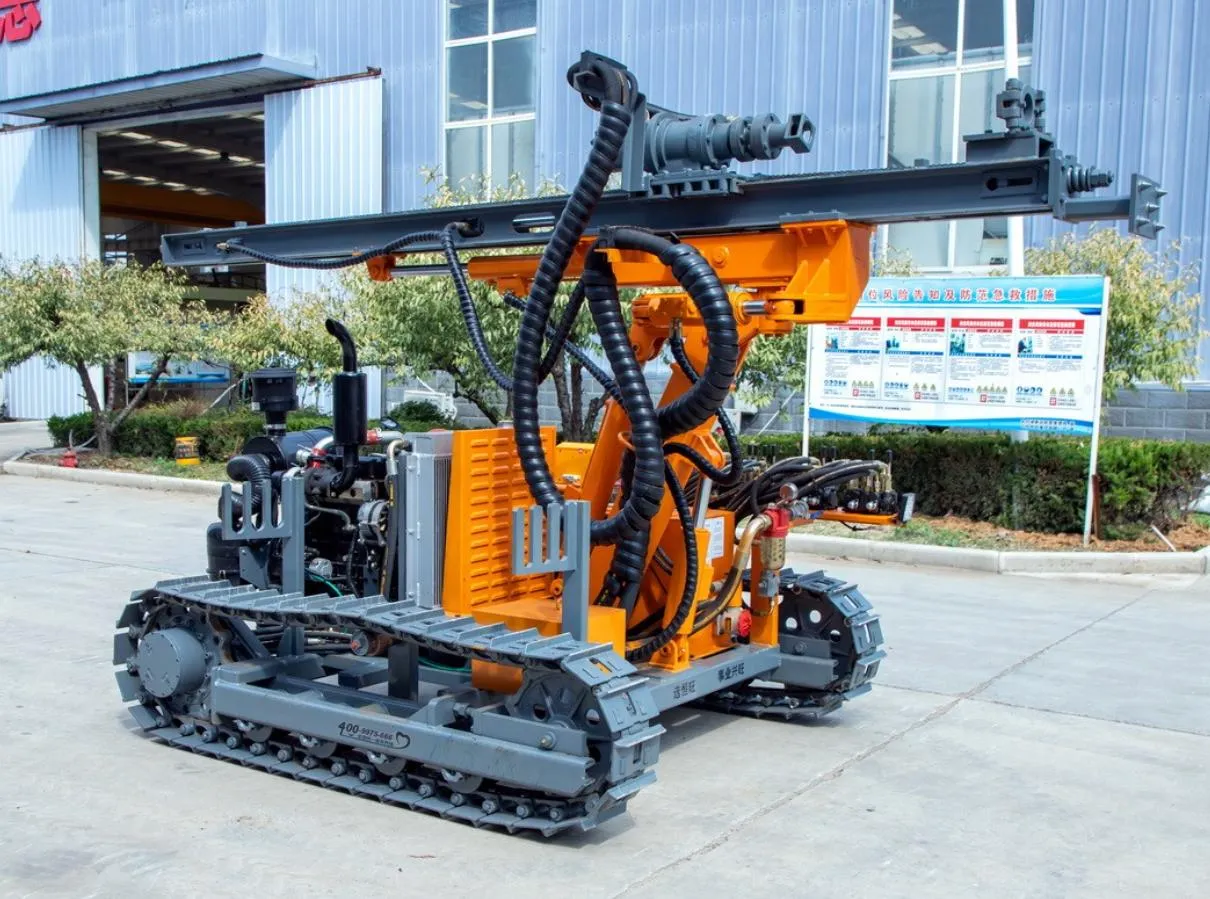
Water pump shafts are subjected to a variety of stresses, including mechanical, thermal, and chemical. Therefore, the selection of an appropriate material is imperative. Among the most widely used materials is stainless steel, renowned for its excellent resistance to corrosion and high tensile strength. Stainless steel shafts are especially prevalent in applications involving exposure to water with various chemical additives or salty environments, such as marine applications.
Another material frequently used is carbon steel. Though it offers lower corrosion resistance compared to stainless steel, carbon steel is highly durable and cost-effective. It provides excellent strength and is often used in freshwater applications or those where the water's chemical composition is not too aggressive. The affordability of carbon steel makes it a popular choice for large-scale operations where budget considerations are significant.
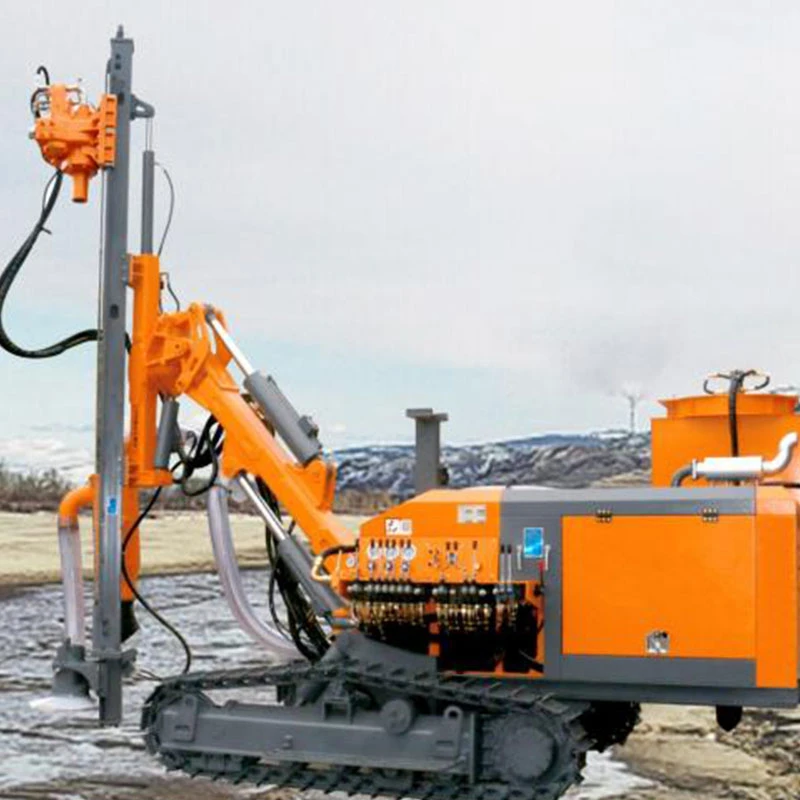
Brass and bronze are also employed in water pump shafts, prized for their anti-corrosive properties and ability to withstand mineral build-up, which is common in water systems. These alloys provide reliable performance in domestic water systems and some industrial applications. Their unique properties make them suitable for specific niche applications, such as those requiring lower magnetic interactions.
Ceramic materials are gaining traction in water pump shaft applications due to their exceptional resistance to wear and heat. While ceramics are not metals, their inclusion in the pump's architecture is increasingly seen in high-precision industrial environments where durability against abrasive action and extreme temperatures is vital. However, ceramics can be brittle, a factor that needs consideration during the design and application phases.
materiales del eje de la bomba de agua
For applications demanding high performance and lightweight properties, titanium comes into play. Its low density coupled with high strength makes it ideal for pumps used in specialized industries such as aerospace. Titanium's resistance to both corrosion and extreme temperatures often outweighs its higher cost, making it a long-term investment in environments where these factors are prevalent.
Each material choice affects the water pump shaft's lifecycle, maintenance needs, and suitability for specific applications. Expert design considerations involve not just the material but also understanding the environmental conditions and operational requirements of the pump. For instance, while stainless steel offers excellent corrosion resistance, it might not be necessary for all applications, leading to unnecessarily increased costs. Conversely, opting for a material like brass or bronze could reduce initial costs but might not meet lifespan expectations under certain conditions.
When selecting a material for a water pump shaft, consulting with industry experts ensures a balance between cost-effectiveness and performance. Leveraging advanced computational models and real-world testing can provide authoritative insights into how different materials perform under specific conditions. Customizing the shaft material based on precise operational data enhances trustworthiness and reliability over the pump's operational life.
In conclusion, the choice of water pump shaft material requires a blend of experience, expertise, authority, and trustworthiness. With continuous advancements in material science technology, the landscape of possible materials is expanding. By considering the unique performance attributes of each material and aligning them with the operational demands of the water pump, more effective and efficient fluid handling solutions can be achieved.