In the industrial landscape, slag pumps are essential components employed primarily in metallurgical and cement industries. Their purpose is to transport slag—a byproduct of smelting ore—which, due to its abrasive nature, poses significant challenges in maintenance and reliability. Ensuring their optimal functionality requires diligent maintenance strategies.
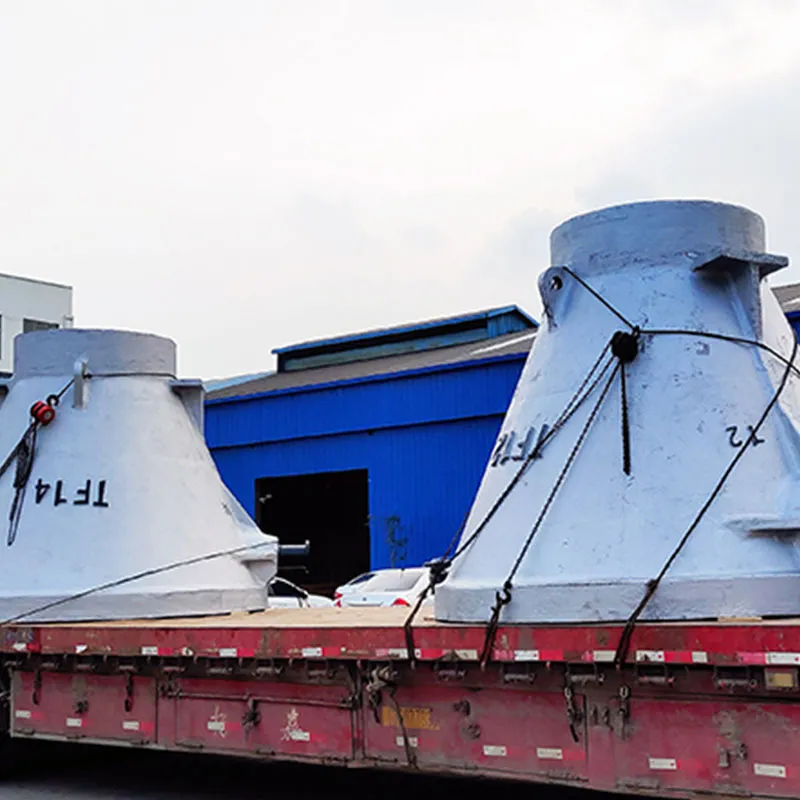
Proper maintenance of slag pumps not only ensures smoother operations but also extends equipment life, thereby offering cost efficiency and production reliability. Here's an insight into maintaining these critical industrial components, driven by experience, expertise, authoritativeness, and trustworthiness.
Industry Experience and Insights
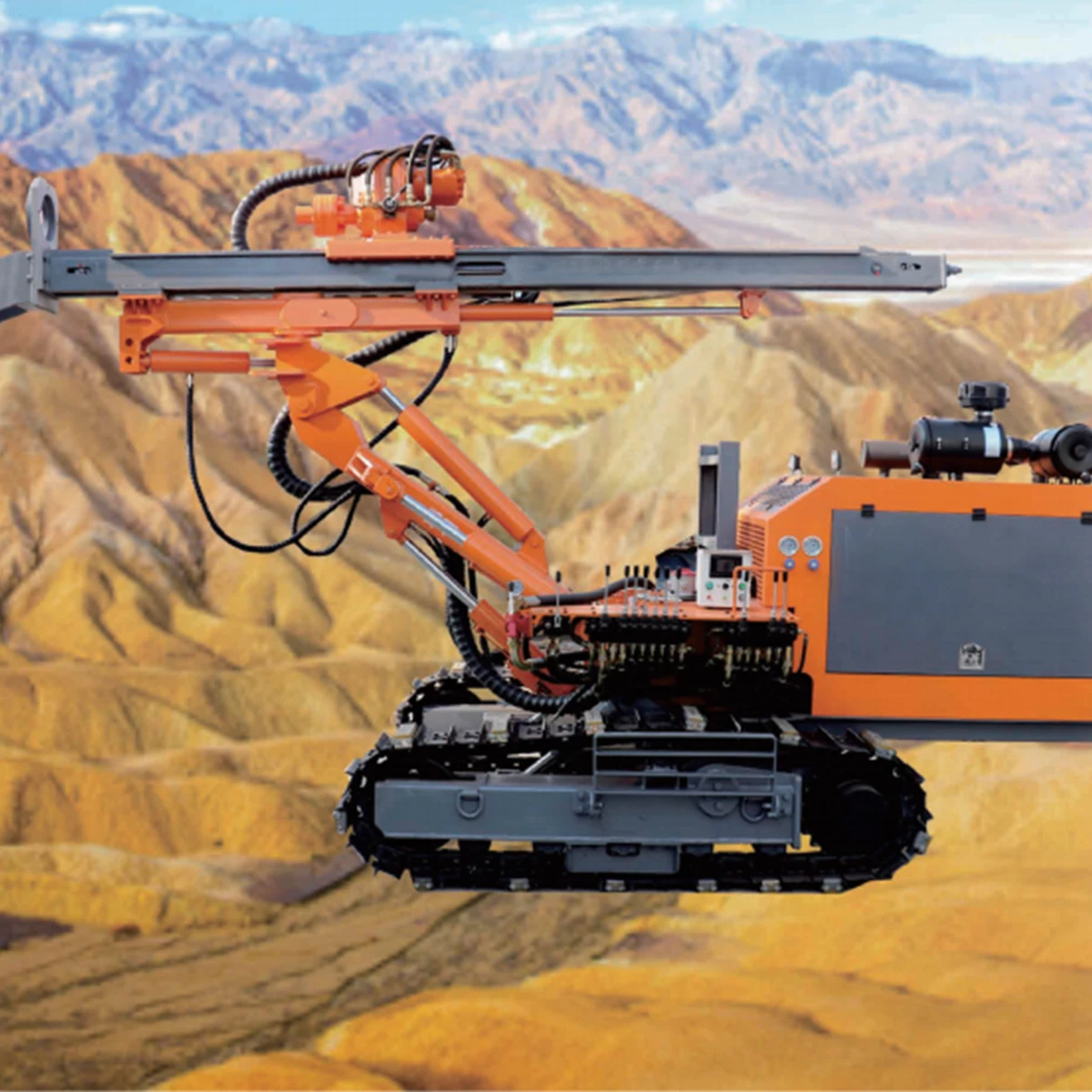
Real-world experience underscores the importance of preventive maintenance over reactive strategies. Regular inspections are vital. Check components such as the impeller, casing, and seals for wear and tear. Given the abrasive nature of slag, these components are prone to degradation. Employing a proactive replacement schedule can prevent sudden failures.
Monitoring vibration levels can also be valuable. High vibration often signals imbalance or misalignment issues, which, if unchecked, can lead to catastrophic failures. Implementing a routine vibration analysis helps in early detection, preventing extensive downtimes and costly repairs.
Expertise in Materials and Techniques
The choice of materials plays a critical role in maximizing durability. Pumps constructed with high-chrome iron or ceramics offer superior resistance to abrasion. Regularly evaluating the material integrity and opting for materials that match the specific slag characteristics in your operation can greatly enhance resistance to wear.
Additionally, employing advanced coating technologies can further reduce abrasion effects. Techniques such as thermal spraying or polymer coatings provide an extra layer of protection. Leveraging these technologies requires specialized knowledge, reinforcing the need for consulting with engineers who have expertise in material sciences.
Authoritative Insights into Maintenance Protocols
maintenance of the sludge pump
Establishing a comprehensive maintenance protocol is crucial. A robust protocol includes detailed records of maintenance activities, inspections, and repairs. This database can help in analyzing patterns leading to wear and failure, allowing for predictive maintenance.
An authoritative approach includes training personnel in best practices for maintenance. Training programs focusing on locking and tagging procedures, safe handling of equipment, and emergency protocols can significantly enhance safety and operational effectiveness.
Sealing technology is another key focus area. The integrity of seals directly influences pump efficiency and lifespan. Regular inspection and timely replacement or upgrading of seals can prevent leakage and contamination, maintaining optimal pump performance.
Trustworthiness Through Sustainable Practices
Incorporating sustainable practices into pump maintenance is becoming increasingly vital. Experts advocate for reusing and recycling worn-out components wherever possible. This not only reduces waste but also aligns with corporate sustainability goals, enhancing the company’s reputation for responsible business practices.
Utilizing condition-based monitoring systems can significantly boost trust in maintenance strategies. These systems use sensors to provide real-time data on pump health, which aids in making informed maintenance decisions. Implementing such an IoT-based approach improves transparency and predictability in operations.
Conclusion
In maintaining slag pumps, integrating experience, expertise, and authoritative knowledge significantly boosts reliability and efficiency, while enhancing trust in industrial operations. Through preventive maintenance strategies, skilled application of materials and techniques, authoritative protocols, and sustainable practices, industries can ensure robust pump performance. This approach not only aligns with operational goals but also with a broader commitment to sustainable and efficient industrial practices.