Jaw plate casting is a cornerstone in the production of heavy machinery, offering the perfect amalgamation of strength and durability necessary for demanding industrial applications. Within this domain, achieving excellence in product output necessitates a deep understanding of the casting process intertwined with technical expertise and vast experience.
This intricate process results in jaw plates that don't just meet industry standards but redefine them.
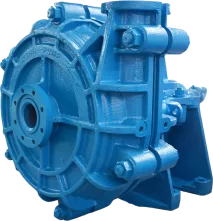
The journey of creating top-tier jaw plate castings begins with selecting the right material. High manganese steel is frequently the preferred choice due to its exceptional work-hardening properties and resistance to impact and abrasion. The composition is crucial, as even minute variations can drastically affect the performance and longevity of the jaw plates. Quality assurance starts here, with meticulous testing and analysis ensuring the material will stand up to the rigors of use.
Next is the mould creation, a critical step where expertise truly matters. The mould must be perfectly dimensioned, accounting for the shrinkage rate of the metal as it cools. This is where the accumulated knowledge of seasoned professionals comes into play, ensuring precision that avoids costly reworks and subpar products. Utilizing advanced computer-aided design (CAD) software, engineers can simulate and rectify potential issues before they manifest, an investment in both time and trustworthiness.
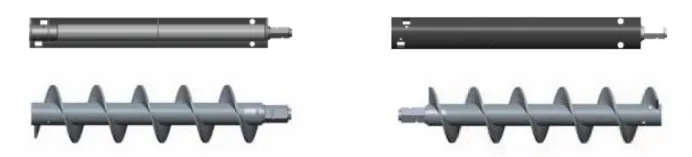
The casting process itself involves pouring molten metal into the prepared moulds. This stage demands acute attention to temperature and timing, with any deviations potentially leading to defects such as porosity or unintended stress points. Here, the role of experience cannot be overstated, as operators must balance a multitude of variables to achieve optimal results. The cooling phase must be carefully managed to avoid rapid temperature drops that might induce metal fatigue or fractures.
Once solidified, the removal of the jaw plate casting from the mold involves skillful handling to prevent damage. This extraction is followed by a series of finishing processes, including heat treatment – an integral part of enhancing the durability and performance of the final product. By elevating the castings to specific temperatures and then cooling them under strict conditions, the internal structure of the metal is modified to increase strength and toughness.
jaw plate casting
Quality control is the final gatekeeper; each casting undergoes rigorous testing under real-world conditions. This includes impact testing, wear analysis, and dimensional accuracy checks. Only those jaw plates that meet the stringent benchmarks proceed to market, underscoring the commitment to reliability and performance.
The expertise required for jaw plate casting doesn't develop overnight. It is a discipline honed over years, where only a deep-seated understanding of materials, processes, and technologies yields the best results. In an industry where precision can significantly impact operational efficiency and safety, entrusting production to those with proven experience guarantees not just product quality but operational excellence.
Moreover, continual advancements in technology and methods are fundamental to maintaining an edge in jaw plate casting. Staying updated with the latest developments through industry seminars, workshops, and academic collaborations ensures the application of cutting-edge solutions to common challenges. This dedication to professional development underscores a commitment to excellence.
Finally, transparency with clients about the processes and limitations involved in casting fosters trust and strengthens business relationships. By providing detailed insights into the crafting of each jaw plate and openly sharing test results and potential improvements, producers can enhance their reputation for authoritativeness and dependability.
In conclusion, crafting jaw plate castings is not merely a manufacturing process; it is a testimony to expertise and prudent application of knowledge. The result is a product that is emblematic of quality and performance, built on a foundation of trusted practices, adept skill, and a commitment to industry standards. This dedication ensures the continued reliability and durability of jaw plates' pivotal role in heavy machinery across the globe.