Jaw crusher plates play a crucial role in the mining and construction industries, acting as the primary force behind crushing rocks and other tough materials into more manageable sizes. Their importance in these sectors cannot be overstated, and understanding the nuances of their function and maintenance can significantly enhance operational efficiency and productivity.
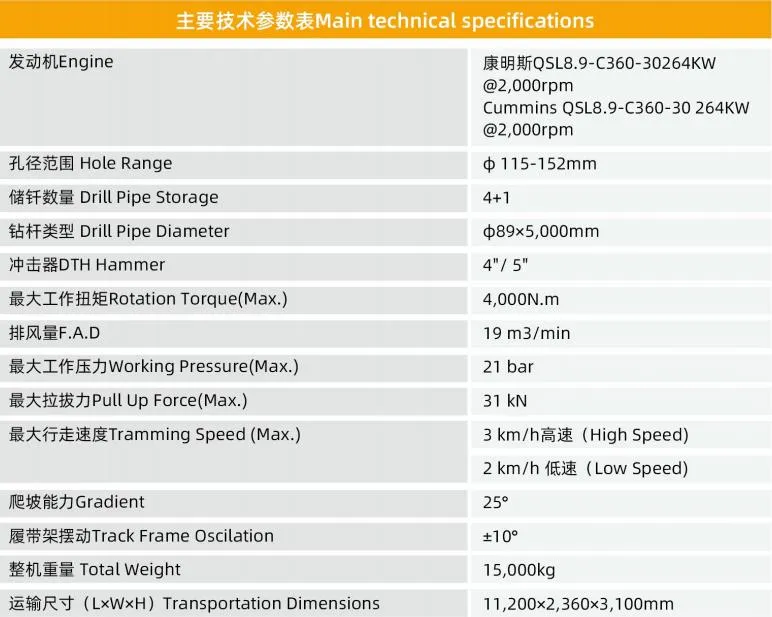
Jaw crusher plates form part of the jaw crusher which consists of two main plates fixed jaw plate and movable jaw plate. These components work in tandem, with the movable jaw applying force and pressure on the rock against the fixed jaw, thereby breaking it into required sizes. The choice of material for these plates is critical to their durability and effectiveness. Typically, they are made from manganese steel, which is renowned for its high impact strength and resistance to abrasion once hardened.
Experience has shown that operational longevity and optimal jaw crusher performance are intricately linked with meticulous attention to maintenance and proper selection of jaw crusher plates. This involves not just regular checks for wear and tear, but also ensuring the correct type and size of plates are used. Various designs of jaw crusher plates are available in the market, including flat, ribbed, and corrugated, each suited for specific tasks and materials. Experienced operators understand that the choice of plate design should be aligned with the requirements of the job at hand, whether it involves crushing hard stones or softer aggregates.
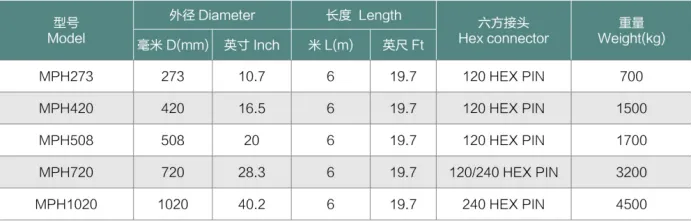
From an expertise perspective, one needs to understand the mechanics of jaw plates within the broader context of the crushing process. Reduced downtime and enhanced efficiency can be achieved by correctly analyzing plate wear patterns. Uneven wear can indicate issues with the crusher's alignment, overfeeding or underfeeding, which can lead to costly downtime if not addressed promptly. Expertise in identifying these wear patterns early, allows for timely shifts in operation techniques or adjustments to machine settings, extending the life of the plates and improving overall crusher function.
jaw crusher plates
The authority of jaw crusher plates in the industrial sector is well documented, with countless testimonials from industry professionals who have witnessed significant improvements in their operations after investing in high-quality plates. Manufacturers often emphasize the importance of sourcing plates from reputable suppliers with a proven track record of delivering products that meet industry standards. Manufacturer-backed warranty and certification offer additional layers of trust, ensuring that the plates can endure the demanding environments they are subjected to.
Trustworthiness emerges as a pivotal aspect when selecting jaw crusher plates. The reliability of these components is essential, given the critical roles they serve in machinery designed for heavy-duty tasks. Industrial users must choose suppliers known for their adherence to quality production processes and dedication to rigorous testing of their products. This ensures that not only are the plates manufactured to meet structural integrity requirements but also that they can perform consistently under varying pressure loads and environmental conditions.
In conclusion, the role of jaw crusher plates within mining and construction industries demands a comprehensive understanding of their function, importance, and maintenance. Pursuing continuous learning and technological advancements in the design and application of these plates can increase operational efficacy significantly. Selecting suitable jaw plates, maintaining them with expertise, and choosing trustworthy suppliers all contribute to maximizing the performance and lifespan of jaw crusher machinery. As industry demands evolve, staying abreast of these developments is paramount for sustained success.