In the ever-evolving world of industrial manufacturing and construction, the jaw crusher stands out as a fundamental piece of equipment. Central to its operation are the jaw crusher cheek plates, integral components that significantly affect the efficiency and longevity of the machine. Understanding and optimizing these pivotal plates isn't just a technical endeavor but an exercise in balancing experience, expertise, authoritativeness, and trustworthiness.
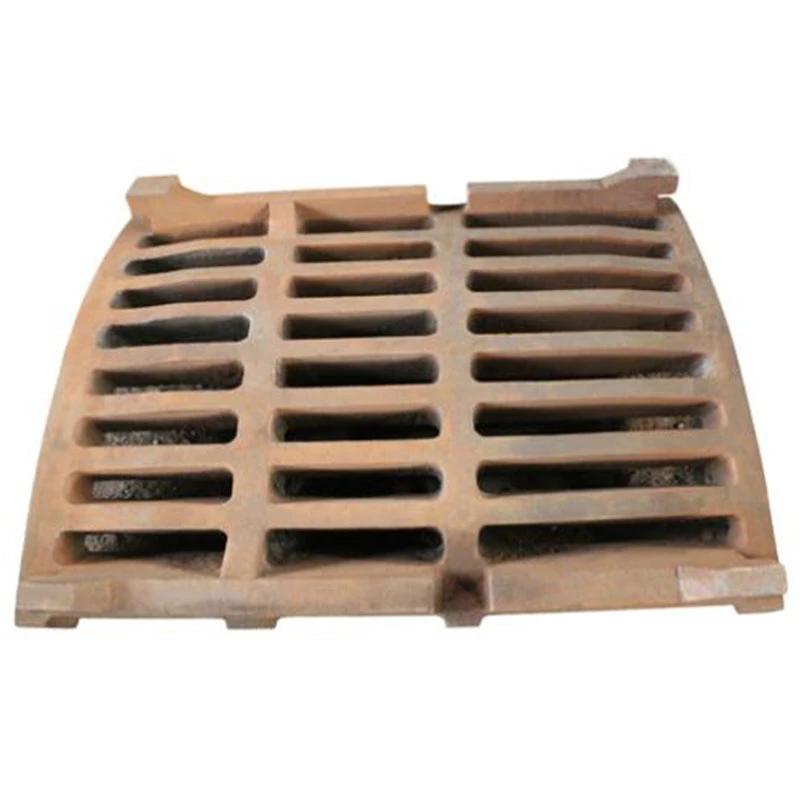
At its core, a jaw crusher functions to reduce large rocks into smaller pieces using a mechanism that mimics the jaw's movement in living beings. The cheek plates, predominantly made from manganese steel due to its durability and hardness, play a crucial role by protecting the crusher frame from wear and tear. A nuanced understanding of these plates can distinguish a seasoned operator from a novice.
First, let's delve into the material science behind jaw crusher cheek plates. Manganese steel is chosen for its unique self-hardening property, which provides longevity under stress. However, modern advancements have led to the development of various steel alloys that cater to specific needs, such as enhanced wear resistance or toughness at different operational temperatures. Operators with hands-on experience will attest to the performance differences these materials can bring in real-world applications.
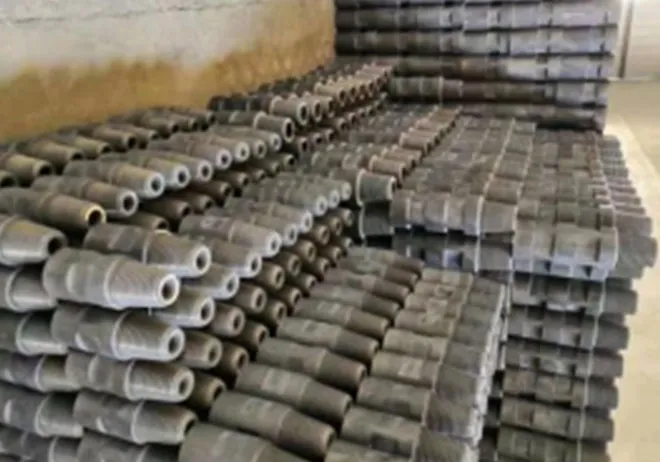
From a manufacturing perspective, the exact design and thickness of cheek plates depend on the crusher model and its intended use. Expertise in this domain involves selecting the optimal cheek plates for specific mining or construction tasks. For instance, a quarry handling abrasive materials will benefit from thicker,
more robust cheek plates. In contrast, operations dealing with less abrasive materials might prioritize lighter, more energy-efficient plates. The precision in these decisions underscores the importance of thorough technical knowledge and experience.
jaw crusher cheek plates
Trustworthiness in jaw crusher cheek plate optimization is not just about technical proficiency but also concerns practical, field-tested recommendations. Manufacturers who commit to rigorous quality testing of their jaw crusher components contribute significantly to the trustworthiness of their products. Furthermore, aligning oneself with industry standards and continually seeking certification from recognized bodies adds layers of credibility. In industries where downtime is costly, reliability in component selection becomes paramount.
Authoritativeness in this domain often comes from a blend of experience and an unwavering commitment to research and development. Leading manufacturers invest in cutting-edge technology to simulate wear and optimize cheek plate design. These efforts are instrumental in extending the life of equipment and reducing maintenance costs, thereby cementing the manufacturer's authority in the field. It's this continual innovation that sets apart respected leaders in the industry from their competitors.
For those involved in the procurement and maintenance of jaw crushers, harnessing experience from seasoned operators and engineers is invaluable. Real-world scenarios often provide unanticipated challenges that theoretical knowledge alone may not resolve. Operators who have experienced localized wear patterns and adapted by customizing cheek plates provide insights that can elevate operational efficiency.
In conclusion, jaw crusher cheek plates, while seemingly simple components, encapsulate a wealth of knowledge that requires a blend of experience, expertise, authoritativeness, and trustworthiness to fully maximize their potential. By keeping abreast of the latest advancements in materials and design, and by valuing the experiential insights from seasoned professionals, businesses can optimize their operations, leading to significant improvements in both performance and cost-effectiveness. As industries move forward, those who understand the intricacies of components like cheek plates will undoubtedly lead the charge in elevating operational excellence.