Choosing the right jaw crusher bearing size is critical for ensuring the optimal performance and longevity of your crushing equipment. Jaw crushers, used predominantly in mining, construction, and material recycling, endure significant stress and wear. The bearings used within these units play a pivotal role in maintaining efficient and consistent operation.
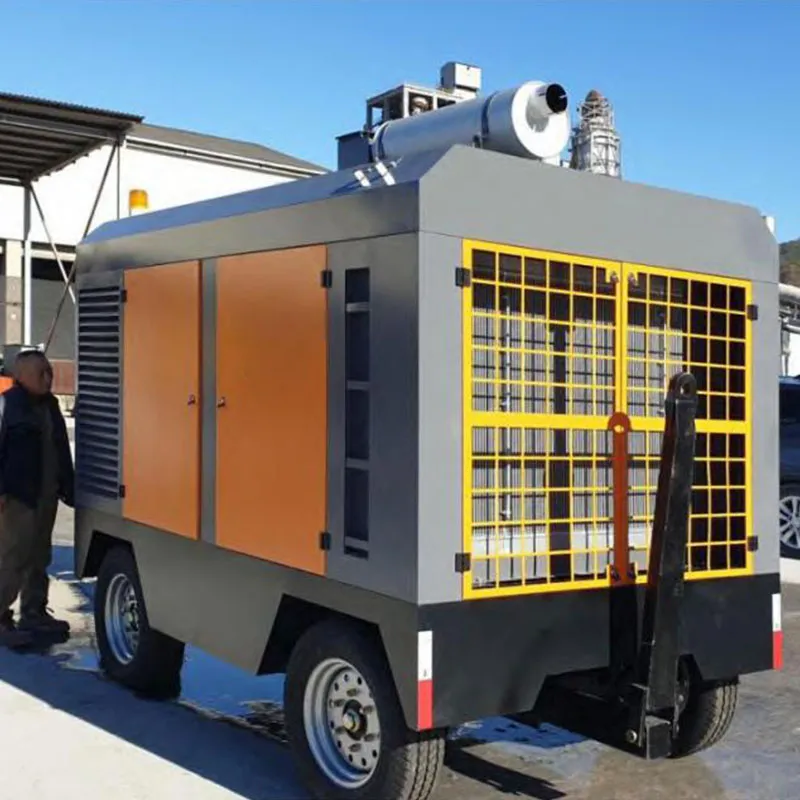
Understanding the specifics about bearing sizes is crucial for both design and maintenance purposes. Jaw crusher bearings need to withstand heavy loads, impact forces, and various environmental stresses. Therefore, selecting the appropriate bearing involves evaluating several key factors.
Start by assessing the working conditions of your jaw crusher. This includes the types of materials being processed, ambient environmental conditions (such as temperature and moisture), and overall operational demands. Different operational contexts require bearings with specific load capacities and resistance properties.
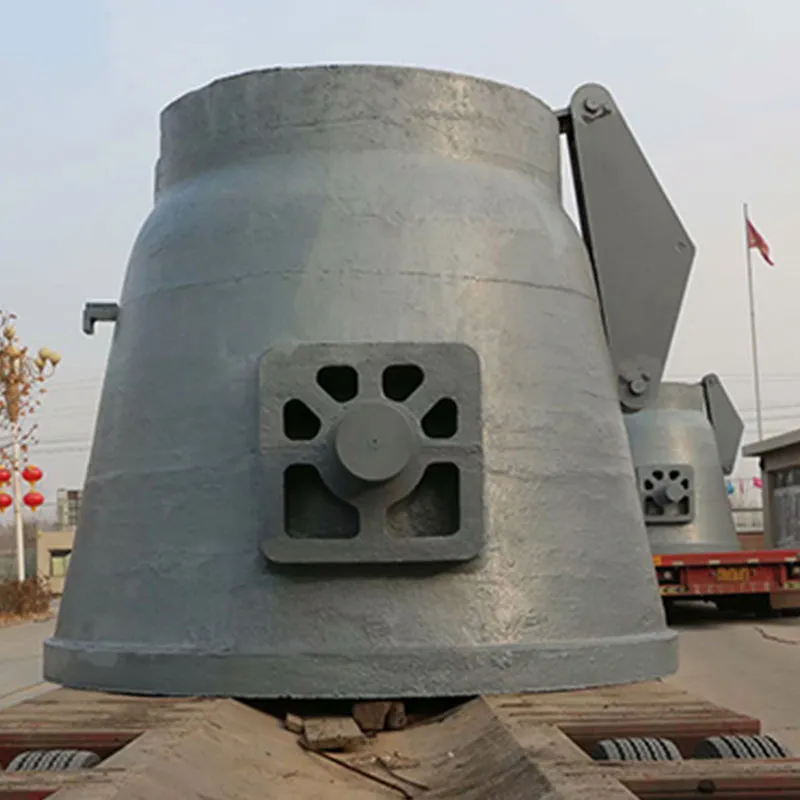
For instance, jaw crushers employed in mining operations frequently encounter abrasive particles; thus, bearings need specialized sealing solutions, such as labyrinth or Taconite seals, to prevent undue wear from contaminants. These features help in extending the lifespan of the bearings by keeping dust and debris at bay.
Additionally,
consider the load calculations essential for determining the right bearing size. Bearings must accommodate both static loads and dynamic loads resulting from operational variances. Typically, the bearing size increases with jaw crusher size and capacity, aiming to handle greater shock loads and metal wear.
Selecting a bearing with a larger size not only improves the crusher's durability but also enhances its efficiency. Larger bearings possess better load distribution capabilities, which translates into reduced internal stress and lower operating temperatures. This reduction in heat generated can significantly prolong the bearing's service life, mitigating frequent maintenance interventions and potential downtimes.
jaw crusher bearing size
Expertise in maintenance practices is equally vital. Routine inspections and lubrication are necessary to ensure peak bearing performance. The lubricant used should match the operational environment—heat-resistant lubricants are ideal for high-temperature operations, whereas water-resistant variants suit humid environments. Regular lubrication decreases frictional forces and aids in heat dissipation, further extending the bearing's operational tenure.
Furthermore, the authority of your brand can be established by partnering with reputable bearing manufacturers. Collaborating with well-known industry leaders not only guarantees high-quality products but also provides access to technical support and innovative solutions tailored to your specific industrial parameters. Investing in high-caliber bearings from reputable brands instills confidence in your operational reliability, thereby enhancing your brand's trustworthiness.
Experienced professionals in the field recommend ongoing training and updates on jaw crusher technology to keep abreast of advancements in bearing design and material technology. Leveraging modern technologies such as condition monitoring systems can also significantly improve maintenance schedules and preempt potential failures.
When evaluating new jaw crusher installations or retrofitting older machines, consult with expert engineers to optimize bearing selection and maintenance procedures. With proper consideration and implementation of these specialized recommendations, operators can dramatically improve the efficiency, reliability, and lifespan of their crushers.
In summary, the choice of jaw crusher bearing size has immense implications on the system's operational efficiency, productivity, and lifespan. Implementing an informed, thoughtful approach—from selecting suitable bearing sizes based on load and environmental conditions, to ensuring rigorous maintenance routines—forms the bedrock of a productive and trustworthy crusher operation.