Using a gravel pump efficiently requires a blend of experience, expertise, authority, and trustworthiness to harness its full potential. This powerful piece of equipment is essential for industries such as mining, construction, and dredging, where moving large volumes of sediment or slurry is necessary. Understanding how to effectively use a gravel pump can not only enhance productivity but also extend the longevity of the machine, ensuring that projects are completed safely and efficiently.
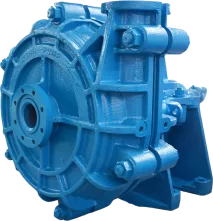
To begin with,
recognizing the appropriate application for a gravel pump is crucial. These pumps are engineered to handle the robust demands of moving gravel, sand, and other heavy sediments that would otherwise cause wear and tear on standard pumps. Their rugged design means they can operate in challenging environments, but selecting the right pump for your specific needs is paramount. Consider the size of the particles, the volume of material to be moved, and the distance it needs to travel. Matching these parameters with the correct pump specifications will ensure optimal performance.
Operators should possess a solid understanding of the technical aspects of a gravel pump. This expertise extends to knowing the components of the pump, such as the impeller, casing, and wear plates, and recognizing how these parts contribute to the pump's functionality. Regular maintenance checks are an integral part of gravel pump operation. A consistent schedule of inspections for wear and tear on impellers and casings can prevent unexpected breakdowns. Consider leveraging technology, such as vibration analysis and thermographic imaging, to pinpoint potential issues before they become serious problems.
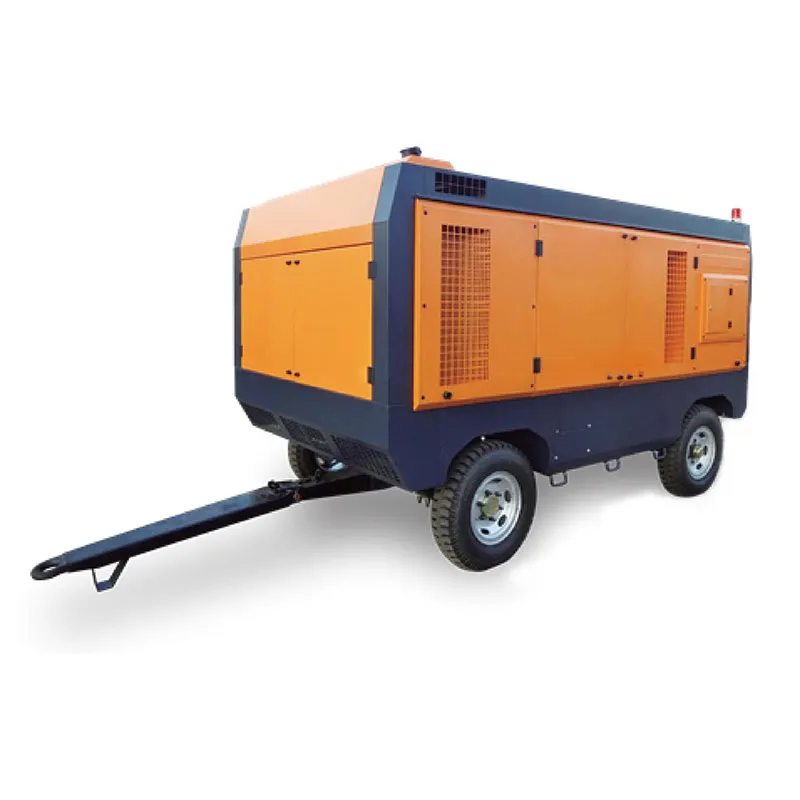
Experience plays a vital role when dealing with gravel pumps. Seasoned operators understand the nuances of the machinery and are adept at adjusting the pump to meet varying job demands. For instance, controlling the flow rate is a critical skill that can prevent overworking the pump, which often leads to overheating or failure. Skilled operators can also sense subtle changes in the pump's performance, such as vibrations or noises that indicate an impending malfunction. This intuition, developed through years of use, can be invaluable in maintaining the pump's efficiency and reliability.
how to use a gravel pump
When it comes to authority and trustworthiness, ensuring that all safety guidelines and operational protocols are followed is non-negotiable. Gravel pumps, due to their handling of abrasive materials, can pose significant risks if not used correctly. Operators must be trained rigorously and continually updated on safety practices and technological advancements in pump design and operation. Utilizing systems like geotagged operation records can add a layer of accountability and traceability, ensuring that the equipment is handled with the utmost care and responsibility.
Entrusting your gravel pump operations to a reputable supplier is equally important. A credible supplier will offer guidance on the best pump system for your needs, provide warranties that reinforce reliability, and have a track record of customer satisfaction. They should also offer comprehensive training and support to ensure that the equipment is used correctly from the get-go.
Emphasizing sustainability, operators should consider the environmental impacts of gravel pumping. Aligning operations with environmentally friendly practices, such as minimizing water usage in slurry transport and ensuring that runoff does not contaminate nearby water sources, is essential. This not only upholds regulatory compliance but also builds trust with stakeholders and the public, demonstrating that operations are conducted responsibly.
In summary, using a gravel pump effectively involves a confluence of experience, technical know-how, adherence to authoritative standards, and a commitment to safety and environmental responsibility. By integrating these elements, operators can maximize the utility of their equipment, ensuring both economic efficiency and operational sustainability.