In the realm of industrial applications, the slurry pump stands as a pivotal component, especially in the mining, construction, and wastewater sectors. Its significance is underscored by its ability to handle abrasive, thick, and oftentimes corrosive materials, effortlessly transferring them from one point to another. But understanding the inner workings of a slurry pump can unlock even greater efficiencies and benefits in operation.
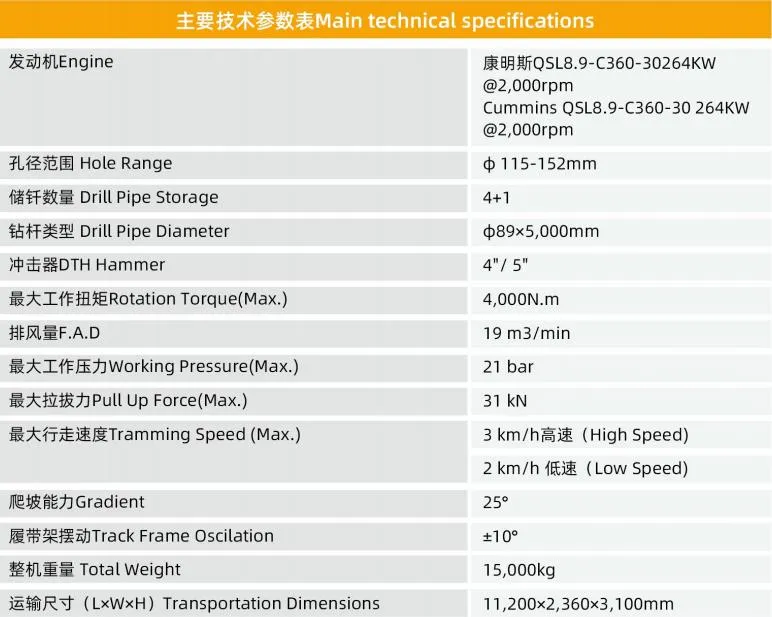
At the heart of a slurry pump lies the mechanism designed to manage slurries—a mixture of solid particles suspended in a liquid. By design, slurry pumps are engineered to manage high wear and tear, anticipating the harsh environments they frequently encounter. The pump's effectiveness is rooted in its robust construction and the careful selection of materials that resist abrasion and corrosion.
A crucial aspect of the slurry pump's operation is its impeller. The impeller, crafted from resilient materials such as high-chrome alloys or rubber, works diligently to create a pressure differential. As the impeller spins, it imparts kinetic energy to the slurry, efficiently propelling it through the pump casing. This movement illustrates the pump’s ability to maintain the flow of dense materials, making it a reliable choice for demanding tasks.
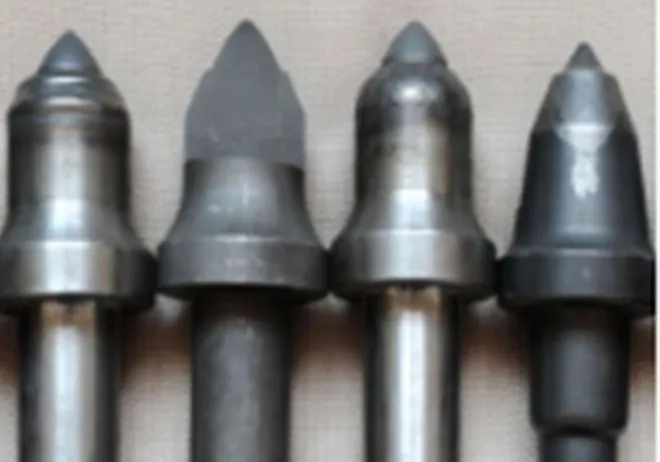
Slurry pumps are distinct from other types due to their thick-walled pump casings. Such design alterations provide enhanced durability and longevity, ensuring they can sustain prolonged exposure to challenging materials without failing. The casings exhibit a volute shape and are often lined with wear-resistant materials which play a significant role in minimizing maintenance needs by reducing wear rates.
how does a slurry pump work
The operation of a slurry pump can also be optimized through the regulation of critical parameters such as flow rate and pump speed, tailored specifically to the type of slurry being processed. Ensuring that these settings are adjusted accurately results in increased pump efficiency and reduced energy consumption.
While selecting a slurry pump, the consideration of particle size, concentration, and nature of the solids is crucial. Pumps that are accurately matched to the characteristics of the slurry will perform with greater efficacy and require less frequent maintenance and repair. This knowledge differentiates experienced operators and experts in the field, highlighting an understanding of the nuanced requirements of specialized pumping tasks.
In everyday operations, slurry pumps need regular inspection to ensure consistent performance. Identifying early signs of wear, such as impeller erosion or casing degradation, allows for preemptive maintenance, averting potential downtime and costly repairs. Best practices in operational management, such as using condition monitoring technologies, reinforce reliability and operational continuity while fostering an atmosphere of trustworthiness through proactive equipment management.
Overall, understanding the functioning of a slurry pump enhances operational effectiveness and resilience. This understanding, interwoven with expert knowledge and experience, underscores the inherent authority and trust professionals hold when dealing with these powerful industrial tools. Such expertise not only guarantees the smooth functioning of industrial operations but also optimizes resources, ensuring that organizations can meet their operational and efficiency goals with precision.