Underground drilling tools play a crucial role in the mining and construction industries, facilitating the extraction of valuable resources and the development of infrastructure in challenging environments. Those involved in selecting and operating these tools must consider factors such as efficiency, durability, and adaptability to varying geological conditions to ensure optimal performance and safety. This article delves into the intricacies of underground drilling tools, providing a comprehensive understanding rooted in expertise, authoritativeness, and trustworthiness.
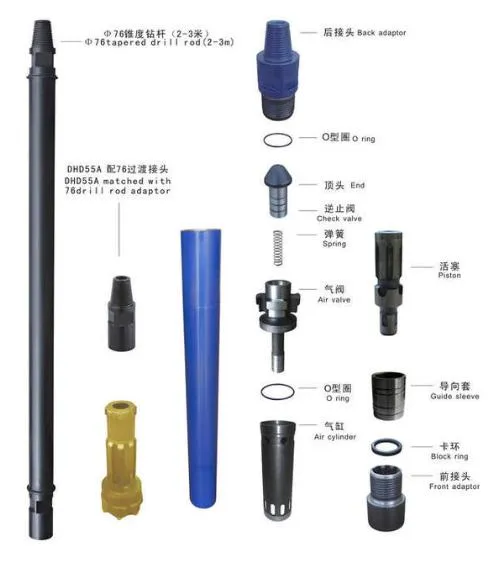
To begin,
the necessity of precision and adaptability in underground drilling cannot be overstated. The various geological formations encountered during drilling operations require tools that can handle diverse substrate types, including hard rock, clay, and sediment. Companies like Sandvik and Atlas Copco have pioneered the development of specialized equipment such as down-the-hole (DTH) hammers, rotary drills, and core drills, each designed to optimize penetration rates while minimizing wear and tear.
Experience with different geological settings is paramount when selecting the appropriate tools. For instance, in limestone formations, percussion drilling with carbide-tipped bits is preferred due to its ability to efficiently fracture the rock, while in softer clay formations, rotary drilling with polycrystalline diamond (PCD) bits offers superior performance by reducing the risk of bit balling and ensuring a cleaner hole. Each of these tool types has its own set of operational parameters, and field expertise is necessary to fine-tune the settings for maximum efficiency.
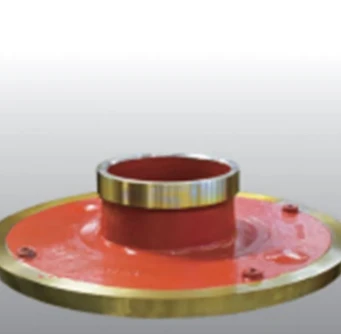
The success of drilling operations also hinges on the durability and maintenance of the selected tools. Long-term projects necessitate robust tools that can withstand extreme conditions without frequent replacement. This makes tool material selection critical, with tungsten carbide and diamond-impregnated segments being popular choices for their resilience and cutting efficiency. Regular maintenance routines, including inspection and timely replacement of worn parts, are essential to maintaining high performance and preventing operational downtime.
Underground drilling tools
Beyond technical specifications, the trustworthiness in the tools' suppliers and manufacturers cannot be overlooked. Manufacturers with a proven track record, such as Boart Longyear and Epiroc, not only signify reliability but also provide assurance through warranties and technical support. Their long-standing industry presence and commitment to innovation foster confidence in the continued advancement and support of drilling technologies.
Moreover, the digital transformation within the industry has introduced advanced monitoring and automation solutions, revolutionizing traditional drilling methodologies. Smart drills with embedded sensors provide real-time data on performance metrics like torque, speed, and temperature, informing operators of potential issues before they escalate. This proactive approach enhances safety and operational efficiency, reinforcing the importance of integrating cutting-edge technology with conventional drilling practices.
In an era where sustainability and eco-friendliness are becoming critical for businesses, the environmental impact of drilling operations cannot be neglected. Alternatives such as electric-powered drilling rigs are emerging, aimed at reducing carbon footprints while improving energy efficiency. Operators are increasingly prioritizing tools that align with environmentally-friendly practices without compromising on performance, encouraging a shift towards greener drilling solutions.
In conclusion, the complexity inherent in underground drilling necessitates a multifaceted approach that considers geological challenges, tool selection, supplier credibility, and environmental consciousness. By aligning operations with industry-best practices and leveraging modern technological advancements, businesses can enhance productivity and contribute sustainably to infrastructural development and resource extraction. The path forward in underground drilling lies in the synergy between expertise, innovation, and sustainability, positioning operators to tackle the challenging demands of modern-day projects effectively.