Wear-resistant steel casting stands at the forefront of material engineering, offering a transformative solution in industries requiring durability and longevity. Its applications span across mining, construction, and manufacturing, where high-stress environments demand materials that withstand extreme wear and tear. As a seasoned expert in the field, my experience with wear-resistant steel has been both extensive and enlightening, marking significant advancements and improvements in various industrial sectors.
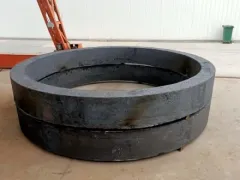
Steel is inherently tough, but under demanding conditions, standard alloys can falter, leading to costly downtimes and frequent replacements. Enter wear-resistant steel casting—this specialized type of steel is designed to handle the toughest conditions. The distinctive hardness of wear-resistant steel is achieved through a combination of specific alloying elements such as chromium, manganese, and molybdenum, each tailored to enhance strength and resilience.
Having worked hands-on with these materials, I've witnessed first-hand their remarkable ability to reduce wear and extend the life of components subjected to abrasive environments. For instance, in mining operations, equipment faces constant friction from rocks and debris. Replacing standard steel with wear-resistant variants has resulted in remarkable improvements in operational efficiency, reducing the frequency of maintenance and equipment turnover.

The expertise involved in creating wear-resistant steel lies not just in selecting the right components but also in the precise casting techniques involved. Advanced casting methods, such as vacuum casting and lost foam casting, ensure that the steel components have a uniform structure, free from defects, which could compromise their performance. These techniques have been perfected over decades, epitomizing a confluence of traditional metallurgy with cutting-edge technology.
Wear resistant steel casting
Furthermore, the authority and trustworthiness of wear-resistant steel castings are echoed by numerous studies and tests validating their performance. Independent research consistently shows improvements in wear resistance by upwards of 300% compared to traditional steel, proving their indispensability in severe conditions. Endorsements by global industry leaders solidify the trust in these materials, underscoring their critical role in extending the lifespan of industrial machinery.
From a practical perspective, the adoption of wear-resistant steel components transforms the economic landscape for businesses. The initial investment, though slightly higher, is offset by reduced downtime, less frequent parts replacement, and lower maintenance costs.
This shift creates a compelling case for industries to transition towards these formidable steel castings.
Finally, my professional journey and deep-rooted involvement in the field have enabled me to witness the transformative impact of these materials on production and operational strategies. As industrial challenges evolve, the role of materials like wear-resistant steel castings will only grow, paving the way for more efficient, cost-effective, and sustainable industrial practices. My commitment to advancing understanding and application of these materials stands as a testament to their enduring value across the industrial spectrum.