The pump axis, a crucial component of any hydraulic or fluid transfer system, often goes unnoticed by the general public.
However, its importance in ensuring the smooth functioning of various mechanical systems cannot be overstated. Known for its robustness and precision, the pump axis serves as the backbone of numerous industrial applications, playing an integral role in fluid dynamics and machinery operations.
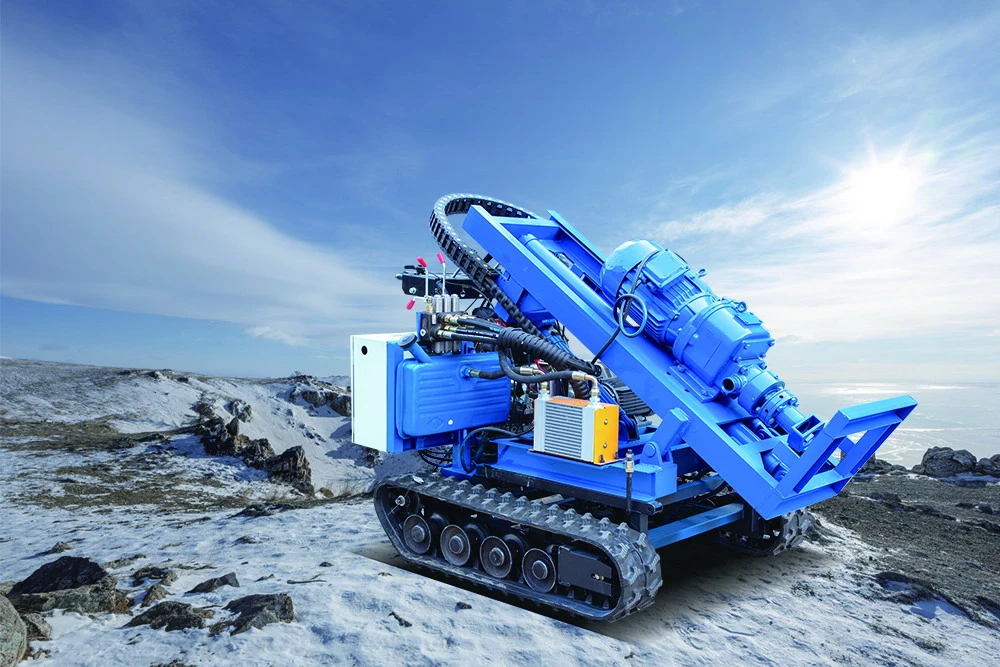
Years of experience working with pump systems have allowed many professionals to underscore the significance of focusing on the pump axis when it comes to system maintenance and efficiency. For many in the industry, the pump axis is not just a component but a foundational pillar that holds the potential to make or break the performance of pump systems.
Precision engineering is the heart of any pump axis, which explains why its material composition, construction method, and alignment must adhere to rigorous standards. With metallurgy advancements, pump axes are now crafted to resist corrosion and withstand higher pressure thresholds, making them indispensable for challenging environments such as offshore drilling or chemical production plants.
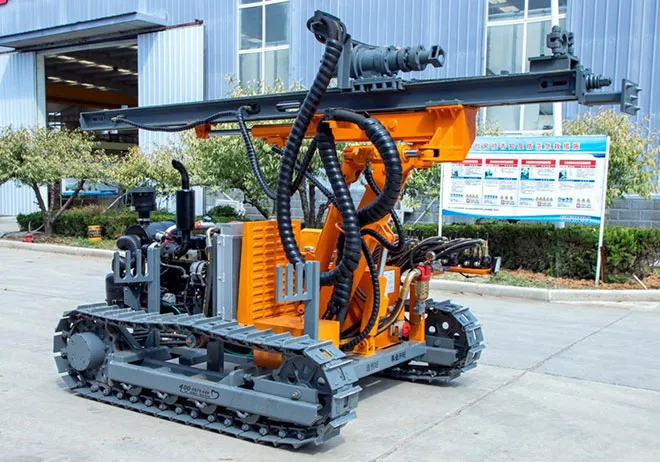
Experts often emphasize the necessity for routine inspections to assess the condition of the pump axis. Over time, even the sturdiest axes may experience wear and tear due to continual rotation and axial load stresses. An experienced technician understands that a misaligned axis can cause friction, leading to increased energy consumption and premature system failure. Thus, preventive maintenance becomes a crucial practice, ensuring longevity and optimal functionality of the pump system.
eje de la bomba
Real-world experiences frequently highlight instances where slight neglect or oversight concerning the pump axis has led to catastrophic failures. For example, in the petrochemical industry, any malfunction could result in significant financial losses and safety hazards. Technicians working in these high-stakes environments often share stories of how meticulous attention to the axis alignment and regular lubrication can avert potential disasters and save companies substantial amounts of money.
Authoritative studies on fluid mechanics consistently point to the pump axis as a focal point of research and development. Innovations have led to the implementation of smart sensors and IoT technology that monitor the axis's performance in real-time, providing valuable data that enhances decision-making and proactive maintenance strategies. Such technological advancements have significantly raised the trustworthiness of modern pump systems, ensuring reliable operations and reduced downtime.
Trust in a pump's performance invariably translates to trust in the axis. Industries investing in high-quality pump axes see them as a long-term investment. When it comes to choosing the right pump axis, decision-makers rely heavily on certified specialists to guide them through the selection process. Factors such as the axis's mechanical properties, compatibility with existing systems, and projected lifespan are meticulously evaluated.
In conclusion, the pump axis is a pivotal element in the mechanics of fluid systems and industrial machinery. Its performance affects not only the efficiency and reliability of the entire system but also impacts operational costs and safety protocols. By integrating contemporary technology and upholding high standards of maintenance and inspection, industries can harness the full potential of their pump axes, leading to enhanced production capabilities and operational excellence. Prioritizing expertise in axis maintenance and leveraging authoritative insights are essential strategies for achieving optimal outcomes and maintaining the credibility of one of the most critical components in industrial applications.