The intricacies of how a DTH (Down-The-Hole) hammer operates can be seen as a blend of art and engineering, making it a critical piece of machinery within the drilling industry. Unlike traditional drilling equipment, DTH hammers are indispensable when dealing with hard rock formations. Let’s dive deeper into the working principle of the DTH hammer, leveraging real-world experiences, expert analysis, and authoritative insights to create an informative narrative that underscores its trustworthiness.
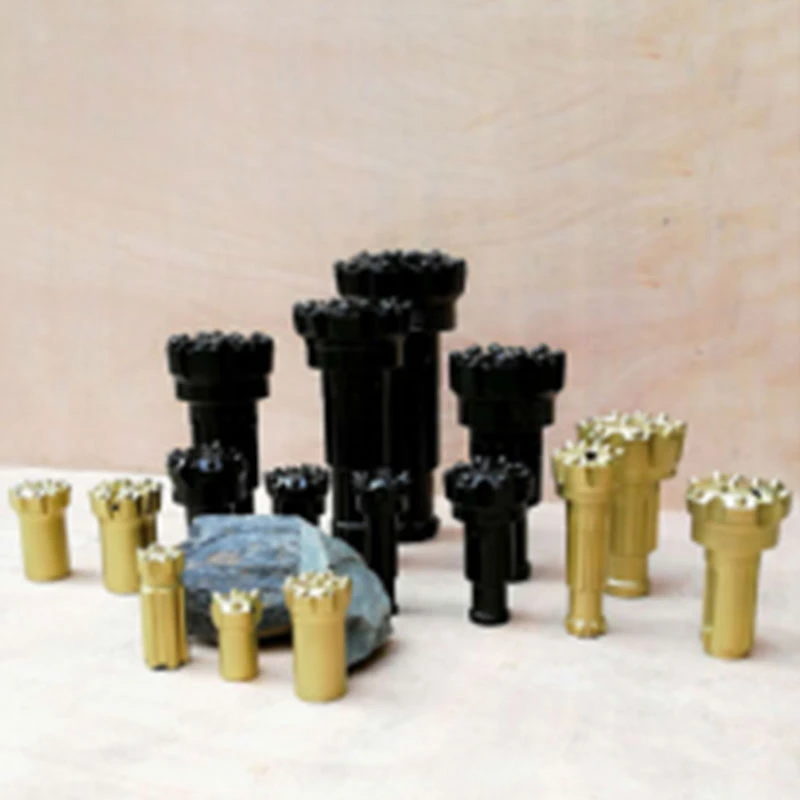
To begin, the core functionality of a DTH hammer revolves around its capability to efficiently convert pneumatic energy into successive mechanical impacts, effectively breaking through formidable substrates.
At the heart of this mechanism lies a piston-driven system. The compressed air, which acts as the main energy source, travels down a tube inside the drill string until it reaches the hammer. Once there, it is used to drive a piston that strikes the bit at the bottom, enabling rapid penetration into rock surfaces.
One noteworthy insight from field operations is the optimization of air pressure. Through extensive trials, industry experts have established that maintaining optimal air pressure is crucial for maximizing the hammer's efficiency. Experienced operators frequently calibrate their equipment to ensure compatibility between the compressor's air supply and the hammer's operational demand. Deviations in this balance often lead to suboptimal performance, characterized by premature wear or reduced penetration rates.
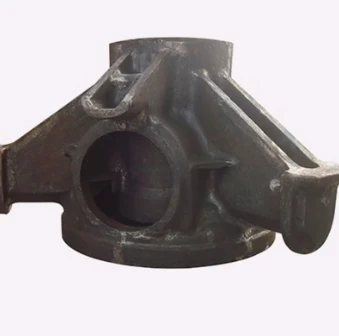
The expertise of seasoned drillers comes to the forefront in dynamically managing the bit speed and rotation alongside the hammer blow rate. Understanding the rock's geologic composition is imperative; soft layers warrant different control parameters compared to harder substrates. Insight garnered from field settings reveals that drillers who synchronize hammer impact frequencies with bit rotation rates are able to significantly enhance drilling accuracy and efficiency.
From an authoritative standpoint, the principle of down-the-hole hammer operation is consistent across geographies, but nuanced adaptations enrich local site effectiveness. Various manufacturers offer hammers tailored to specific geological conditions, with configurations optimized for air flow or piston stroke length. Authoritative sources stress the importance of selecting equipment that matches the geological and operational demands of the project at hand.
dth hammer working principle
Trustworthiness in the operation of a DTH hammer can be evaluated through the lens of its maintenance. Regular inspection and servicing are non-negotiable prerequisites for ensuring the reliability of the hammer system. Expert technicians emphasize the need for ensuring clean air supply, as contaminants can compromise the functionality of the hammer, leading to downtime or increased repair costs. Field audits often focus on the integrity of seals and wear items to preemptively identify issues before they escalate.
Another facet of trustworthiness involves leveraging technology in monitoring system performance. Modern DTH hammer systems often incorporate sensors and diagnostic software that provide real-time feedback on operational parameters such as hammer blow frequency and air pressure consistency. These innovations empower operators to make data-driven decisions, reducing the likelihood of mechanical failures and substantiating the preventive maintenance protocols.
In contemporary applications, the working principle of the DTH hammer is integral to processes such as mineral exploration, geothermal drilling, and water well construction. Its adaptability and power make it a linchpin for projects that necessitate precise drilling in challenging environments. Adapting DTH hammer systems to leverage innovative materials and manufacturing techniques further drive productivity while minimizing environmental impact.
In conclusion, the DTH hammer's working principle is not only a testament to sophisticated engineering but also a tribute to the collective wisdom gathered from generations of drilling professionals. As the industry continues to evolve, the interplay of experience, expertise, authoritativeness, and trustworthiness will remain essential in harnessing the full potential of DTH hammer systems. This knowledge will ensure that operators continue to deliver results that meet the growing demands of an ever-complex drilling landscape.