Navigating the world of DTH (Down the Hole) drill bits can be a complex journey, demanding a blend of technical expertise, hands-on experience, and a keen understanding of the specific application needs. As an essential component in the realm of mining, geothermal drilling, and construction, DTH drill bits stand out for their durability, precision, and efficiency. This article delves into the nuances of DTH drill bits, highlighting their unique features, expert insights on selection, and the latest trends enhancing their application.
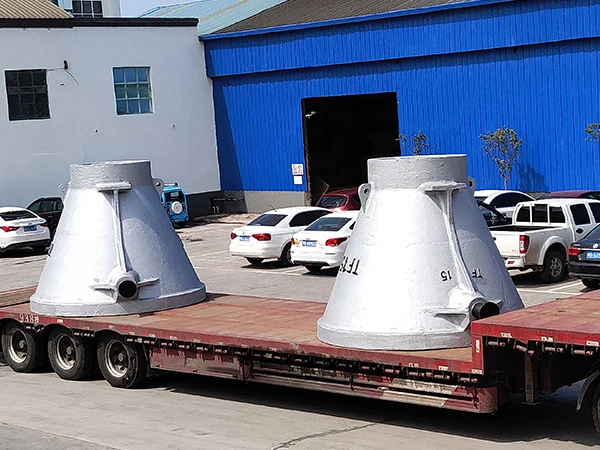
DTH drill bits are renowned for their robustness and are integral for a variety of drilling activities, where precision and penetration speed are crucial. Designed to withstand extreme conditions, these bits facilitate the transfer of maximum concussive force to the rock face, minimizing energy loss and enhancing operational efficiency. The design intricacies, such as the button configuration, size, and shape, play a pivotal role in their performance and longevity.
Industry expertise underscores the importance of selecting the right drill bit based on the geology of the drilling site. The rock formation's hardness and abrasiveness dictate the bit's material and design. For instance, harder formations may necessitate tungsten carbide buttons, known for their hardness and resistance to wear. Simultaneously, softer formations might benefit from steel-based bits that offer better flexibility and reduced cost.
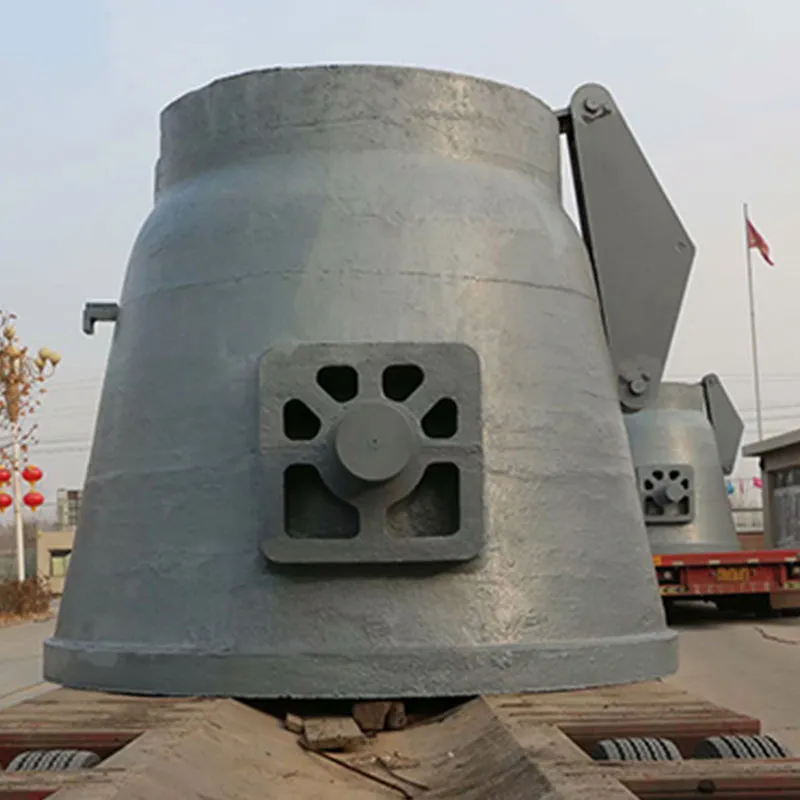
American Drilling Company, with decades of industry presence, emphasizes real-world testing and adaptability in challenging terrains. The company advocates for test runs in site-specific conditions, asserting that theoretical knowledge, while foundational, must be augmented by practical experience for optimal bit selection. Their rigorous testing protocols ensure that bits not only withstand the test of time but also remain efficient throughout their lifespan.
dth drill bits
Trustworthiness and reliability are key when it comes to purchasing DTH drill bits. Manufacturers with ISO certifications and stringent quality control standards are often preferred, as these credentials assure a commitment to quality and continual improvement. Additionally, patented technologies and innovations signal a company's dedication to enhancing drill bit effectiveness, such as advanced heat treatment processes and customized button designs that prevent premature wear.
Trends in the DTH drill bit industry are leaning towards sustainability and smarter technology integration. Environmental considerations are driving the industry to develop eco-friendly drilling solutions that reduce fuel consumption and emissions. This is especially pertinent in countries with stringent environmental regulations. Moreover, the incorporation of IoT and AI technologies is enabling real-time monitoring and data analytics, allowing operators to make informed decisions and preemptively address potential issues.
A growing body of research conducted by leading geological institutions supports the use of adaptive drill bits that adjust to varying rock densities automatically, promising major efficiency gains. These innovations not only extend the lifespan of drill bits but also significantly cut down operational costs.
In summary, the evolution of DTH drill bits is marked by a deep integration of expert knowledge and cutting-edge technology. The future holds promise for even more advanced, efficient, and environmentally conscious drilling solutions. Industry leaders and seasoned professionals agree that a blend of material science, field experience, and tech innovations will shape the next generation of drill bits. For companies and individuals venturing into drilling operations, understanding these dynamics is essential for maximizing efficiency and ensuring sustainable growth in a competitive landscape.