When it comes to drilling technology in the oil and gas industry, down hole hammer bits represent a specialized and highly-effective tool. Known for their efficiency and performance in challenging drilling conditions, these bits are revolutionizing how companies approach subterranean projects. With years of evolution in drilling technology, understanding the nuances of down hole hammer bits can significantly impact operational success.
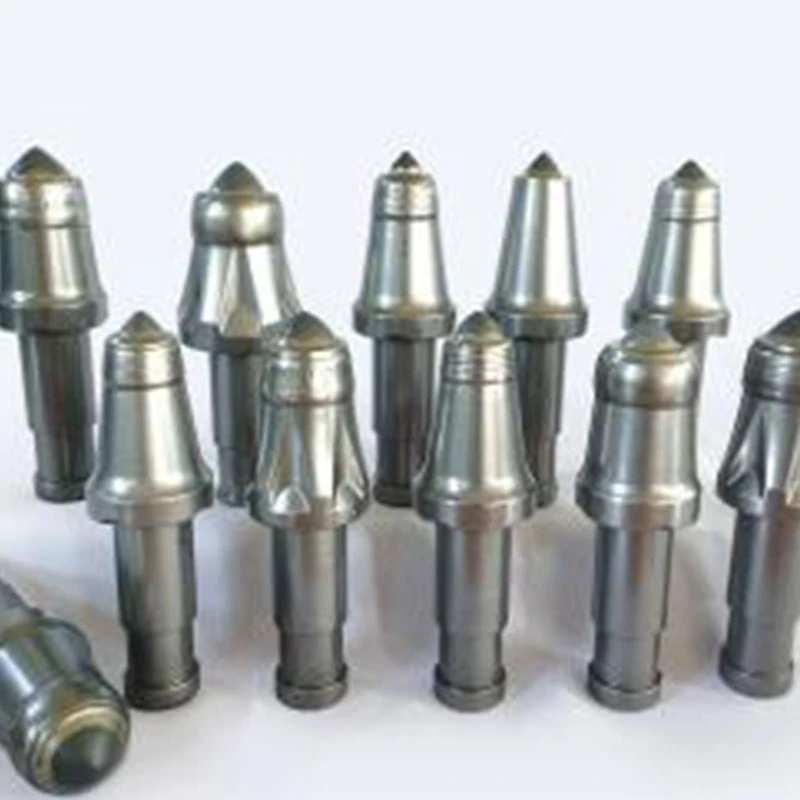
Down hole hammer bits, known for their robustness and ability to crush rocks with rapid percussion, are integral to precise and cost-effective drilling operations. These bits utilize a percussive mechanism that pounds the rock as the drill rotates, allowing for faster penetration and more efficient excavation of hard materials. The mechanism reduces the need for extreme downward force, which not only enhances the lifespan of the drilling equipment but also leads to more accurate extraction processes.
From an expertise perspective, the design of down hole hammer bits emphasizes adaptability to various rock formations. The bits come in multiple designs, each tailored for specific geological conditions, ensuring that operators can select the optimal tool for their projects. This versatility underlines the importance of choosing the correct bit; a mismatched bit can lead to inefficient drilling, increased wear and tear, and ultimately higher operational costs. It's crucial for operators to work with experienced engineers who can assess the geological conditions and recommend the most suitable bit design.
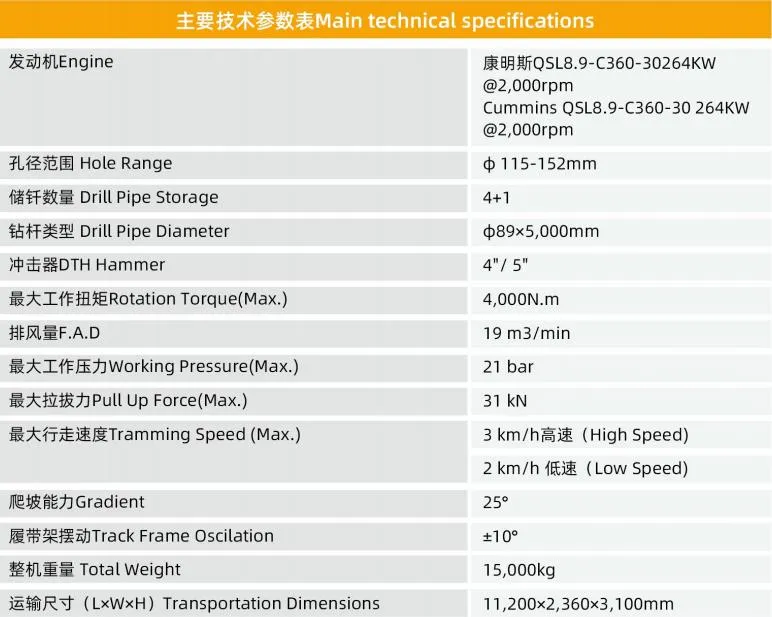
In-depth knowledge about down hole hammer bits extends into their construction materials. High-grade steel combined with tungsten carbide inserts is often used to craft these bits, providing both durability and resilience under intense conditions. Manufacturers frequently focus on material innovations to improve wear resistance and operational longevity. Discussions with industry experts continually highlight the importance of these advancements, speaking to the broader trend of enhancing drilling efficiency while minimizing downtime.
down hole hammer bits
Authoritativeness in the field of down hole hammer bits comes from understanding the technological advancements and real-world applications.
Operators rely on authoritative sources for information on the latest developments in hammer bit technology. These sources facilitate informed decision-making for purchasing, maintenance, and replacement, guiding operators to achieve optimal performance. Companies providing these resources are generally recognized for their innovation and leadership in the field, and maintaining a relationship with such entities can significantly benefit operational outcomes.
Trustworthiness is paramount, especially given the substantial investments associated with drilling projects. Reputable manufacturers of down hole hammer bits offer extensive warranty and support programs, ensuring that users can operate with confidence in the reliability of their tools. Performing due diligence by vetting suppliers through industry reviews, certifications, and proven track records can mitigate risks associated with equipment malfunction or sub-standard performance.
Industry experience consistently shows that selecting the right down hole hammer bit involves a combination of expert insight and cutting-edge technology. Collaborating with seasoned drilling professionals can provide invaluable advice on optimizing drilling strategies, helping to reduce costs and improve project timelines. Furthermore, participating in industry forums and conferences can offer additional exposure to emerging trends and technologies in down hole drilling, fostering an environment of continuous improvement and learning.
In summary, down hole hammer bits are more than mere tools; they are critical components that directly affect the efficiency and success of drilling operations. By prioritizing experience, expertise, authoritativeness, and trustworthiness, organizations can ensure that they are using the most appropriate and high-performing drilling solutions available. Embracing the innovation inherent in the design and application of these bits opens pathways to operational excellence and sustained profitability in the demanding landscape of underground drilling.