Designing a centrifugal slag pump is a highly specialized task that requires a blend of mechanical engineering expertise and practical industry experience. These pumps are crucial in industrial applications, particularly in environments that handle abrasive or high-density materials. Their efficiency and reliability significantly impact the operational success of such settings.
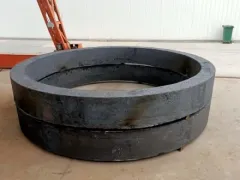
The initial step in designing an effective centrifugal slag pump is a comprehensive understanding of the material characteristics it will handle. Slag, being a byproduct of metal smelting and mineral extraction processes, has distinctive properties it's dense, has a varied particle size distribution, and can be highly abrasive. These characteristics demand that the pump materials are selected to withstand extreme wear and tear. High-chrome iron, for instance, is often chosen for its abrasion resistance and durability.
Precision in design is paramount. The impeller, the heart of the centrifugal pump, must be configured to deliver optimal hydraulic performance while minimizing wear. This involves careful selection of the impeller size and shape, along with the casing design, to ensure efficient movement of slag slurry with minimal energy loss. Computational Fluid Dynamics (CFD) simulations can be instrumental at this stage. These simulations allow designers to model the flow characteristics within the pump, identify potential problem areas, and refine the design before physical prototypes are developed.
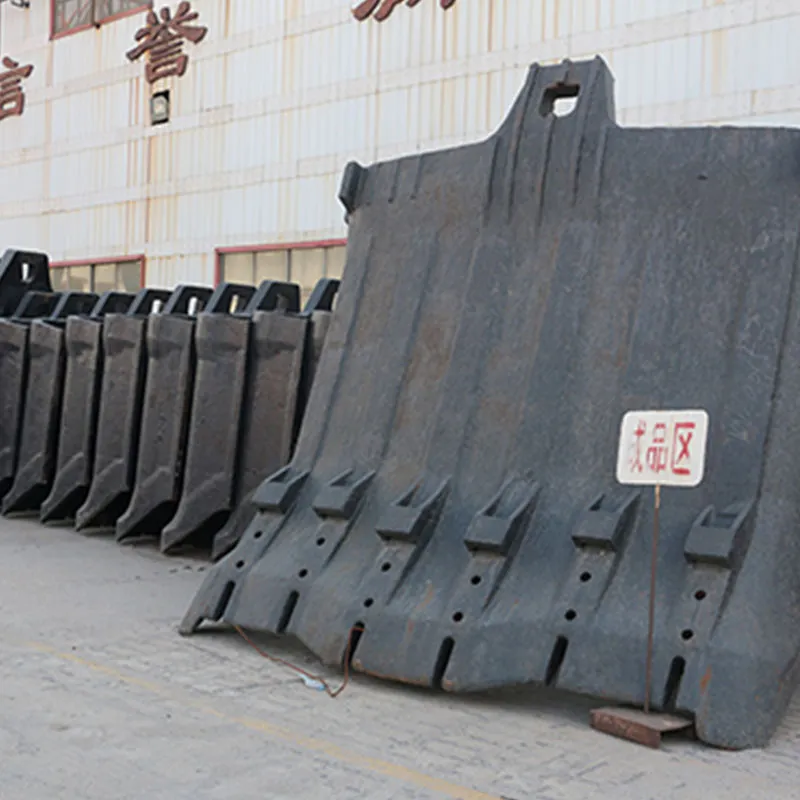
Balancing efficiency and durability is a core challenge. While a high-efficiency design may prioritize reduced energy consumption, it should not come at the expense of the pump's longevity. Incorporating features such as replaceable liners or wear plates can prolong the pump's operational life and reduce maintenance costs. Understanding the trade-offs and making informed decisions about these elements are where expert knowledge truly shines.
Another pivotal design consideration is maintaining operational versatility. Industrial settings are dynamic; the pump may face varying operational conditions. Providing flexibility in the design, such as adjustable impeller clearances or variable speed drives, can help adapt the pump to different slurry characteristics or flow requirements. This adaptability enhances the pump's utility across a broader range of applications.
Design of centrifugal slurry pump
From a trustworthiness standpoint, employing rigorous testing protocols is essential to validate the pump's performance. Standard tests like Hydrostatic Testing for leak prevention, and Performance Tests under simulated operational conditions, ensure the pump will meet the desired performance metrics. Documenting these procedures and certifications fortifies the pump's credibility in the market.
Additionally, expert feedback from field engineers and maintenance crews can be invaluable. These professionals offer insights into practical challenges faced during installation and operation, allowing for continuous improvement in subsequent designs. Such feedback loops are a testament to the authoritative approach of a manufacturer committed to excellence.
A company designing centrifugal slag pumps must also provide comprehensive after-sales support, including detailed maintenance guides, readily available replacement parts, and technical support. This not only heightens customer trust but also secures brand loyalty in the competitive industrial equipment landscape.
In summation, the design of a centrifugal slag pump is an intricate process that demands detailed engineering knowledge, attention to material science, and a keen understanding of the operational context. Achieving success in this field relies on a blend of cutting-edge technology and real-world application, underpinned by a commitment to superior quality and reliable performance. Such achievement positions a manufacturer as a leader in the market, able to meet and exceed customer expectations with every product they deliver.